Assembly hall
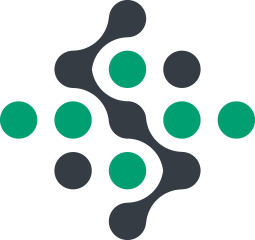
An assembly workshop adjoining the design office
Since 2018, we have had our own assembly hall to assemble all our machines and equipment and fine-tune them before dispatch.
This 650m² workshop is adjacent to the design office to ensure maximum proximity and responsiveness. It is equipped with a range of lifting equipment (8-tonne bridge crane – 6m under hook; forklift truck).
We also have an electrical power and compressed air distribution network that enables us to test equipment and machines in operation. The machines can also be connected to our company’s IT network to test remote access, traceability and production reporting functions.
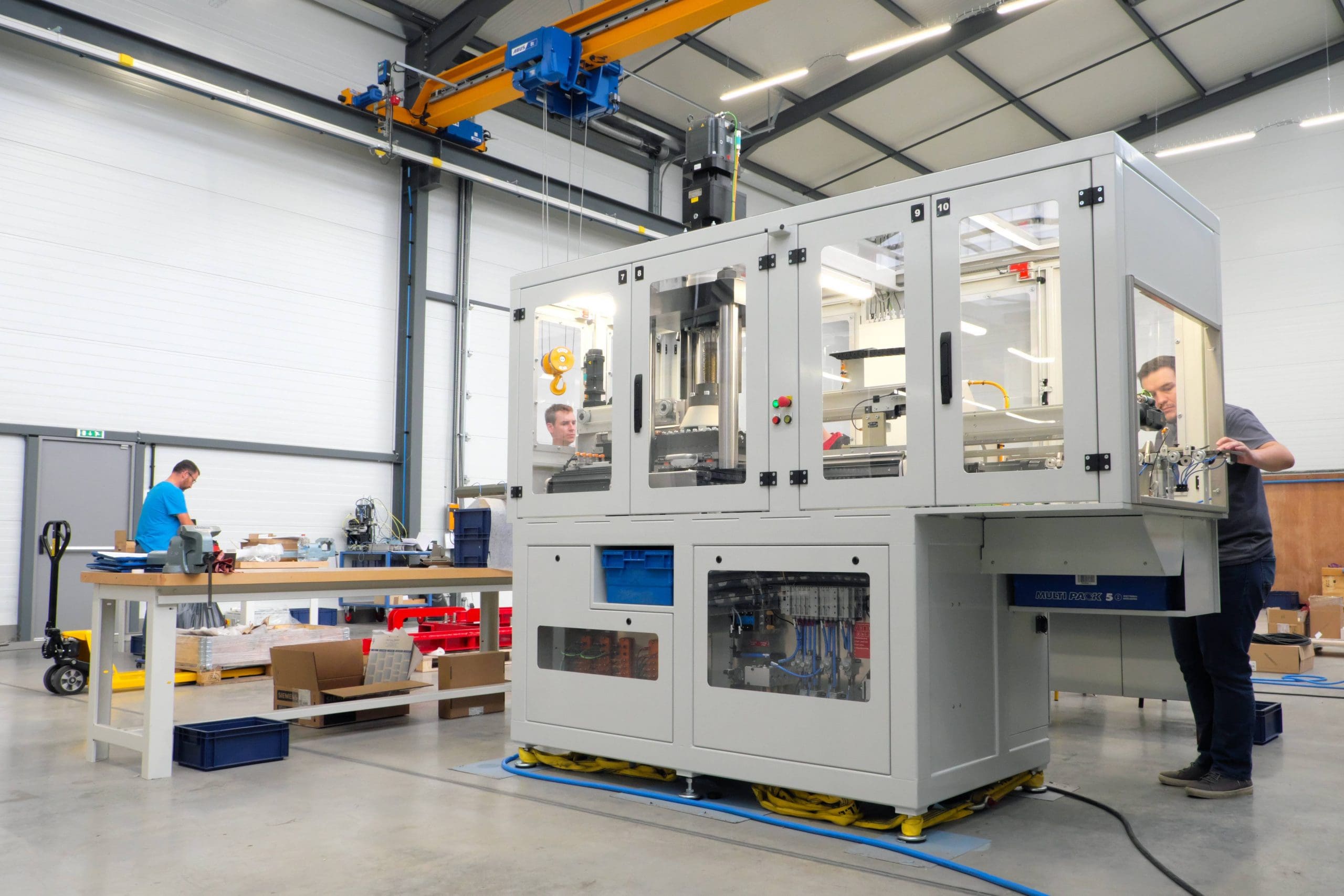
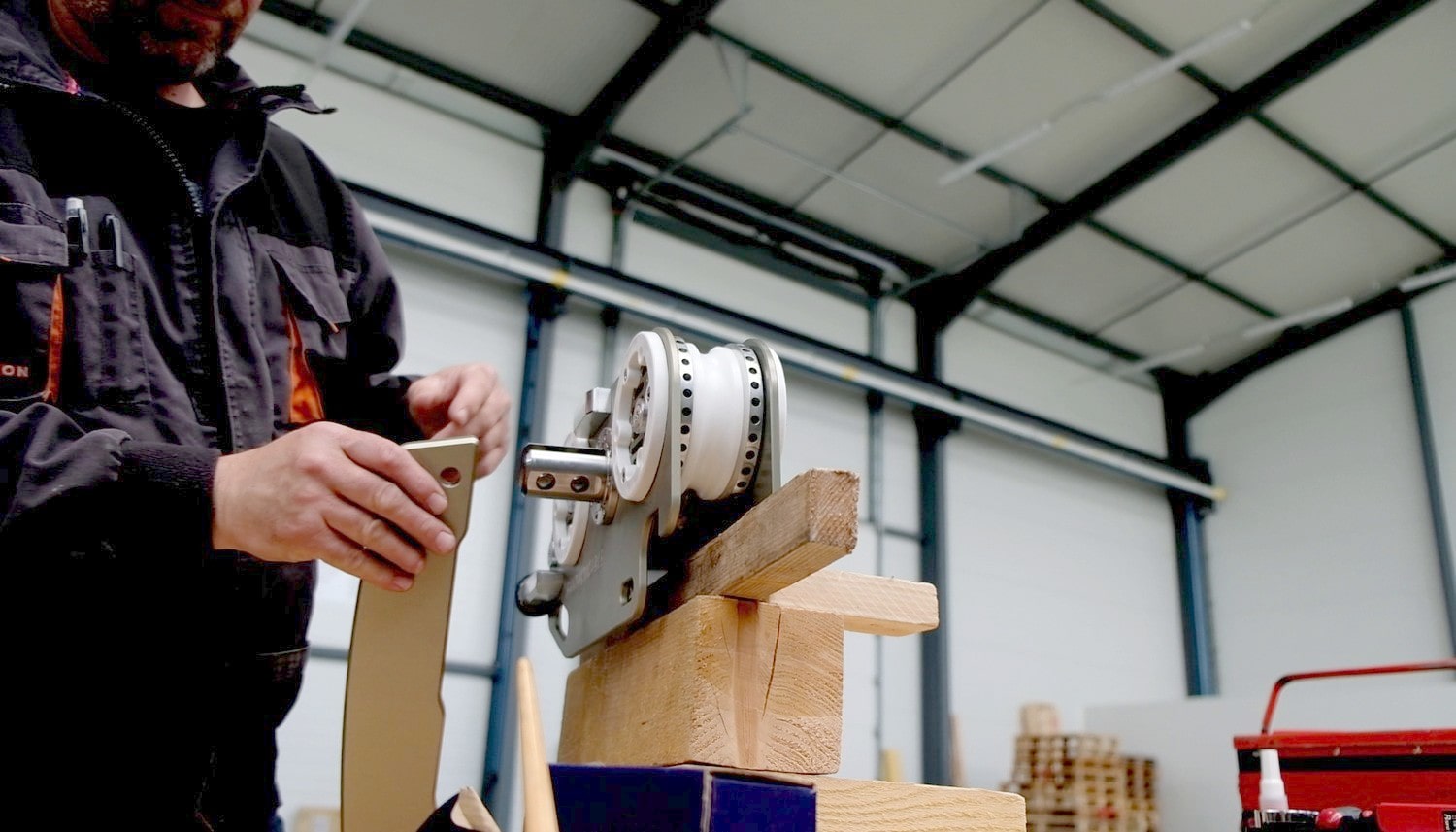
Thanks to its reasonable size, Le Sur-Mesure Industriel is unique in that the people in charge of designing your machine will also carry out its assembly, programming and fine-tuning. The project managers are therefore involved from A to Z, and are your sole contacts right through to the installation and commissioning of the equipment.
This project follow-up gives us greater expertise in the design or programming details and the finesse of the systems developed. We benefit from direct feedback between design and implementation. This enables us to continually improve our teams’ design and programming methods, as well as the choice of concepts to be implemented depending on the application.
Controlled supply of spare parts
All mechanical parts are made from our detailed drawings. They are supplied by us from our suppliers specialized in their field of manufacturing (machining, sheet metal work, mechanical welding, heat treatment, coating, painting, etc.)
We deliberately favor local partners. Indeed, proximity ensures that we can exchange information in complete confidence in order to meet manufacturing deadlines and ensure the quality of the parts produced. For an assembly requiring precision and adjustments, we have the capacity for rapid and quality response thanks to our industrial partners. They carry out the adjustments for us in the case of position adjustments or mechanical clearance in equipment.
We define and size all commercial references and accessories appropriate for your application: motors, actuators, detectors, cylinders, standard components, electrical items, etc…
We are completely free to use and integrate the brands of our choice or according to the preferences and standards of our customers. We do not hesitate to supply the best components, directly from renowned manufacturers, from abroad if necessary.
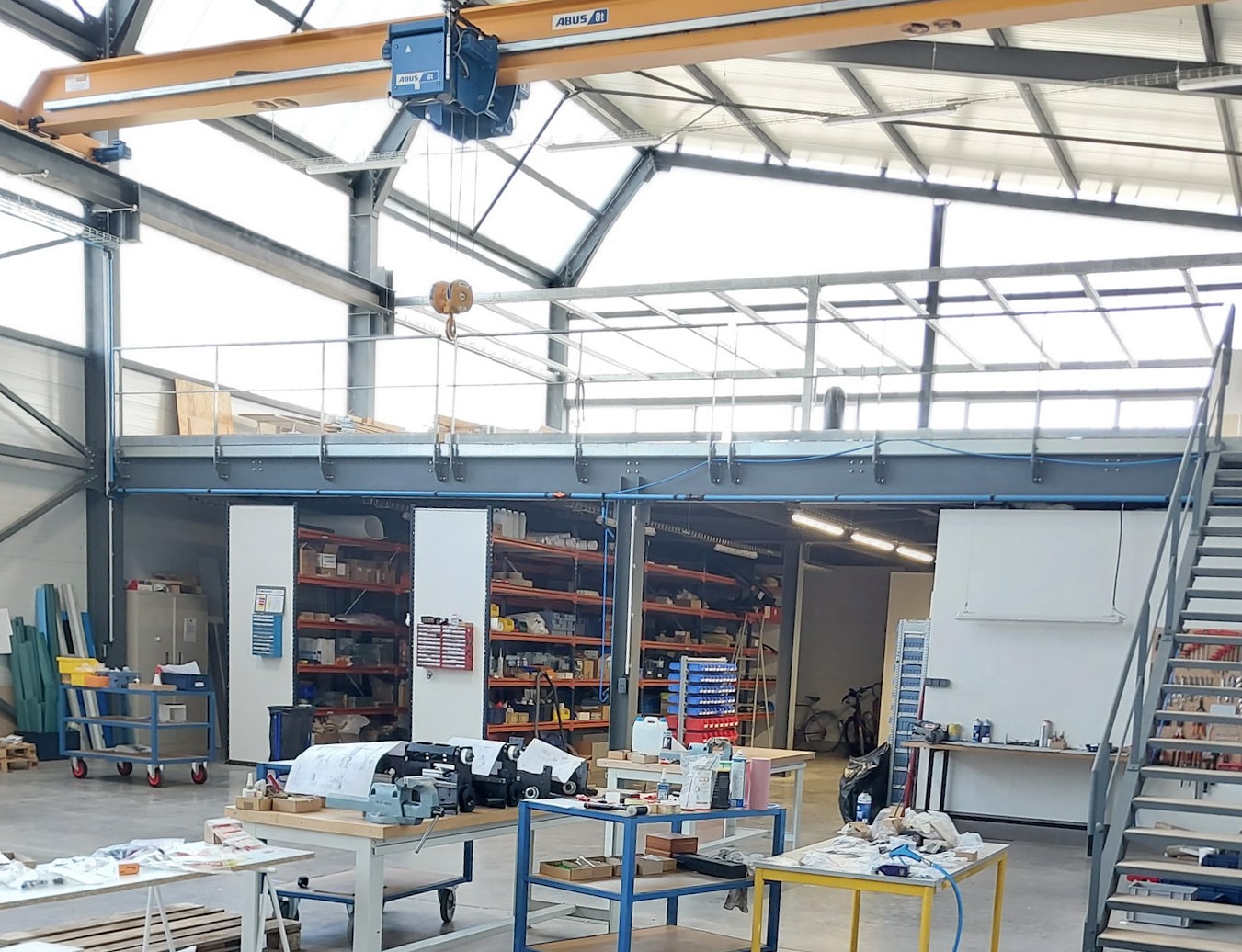
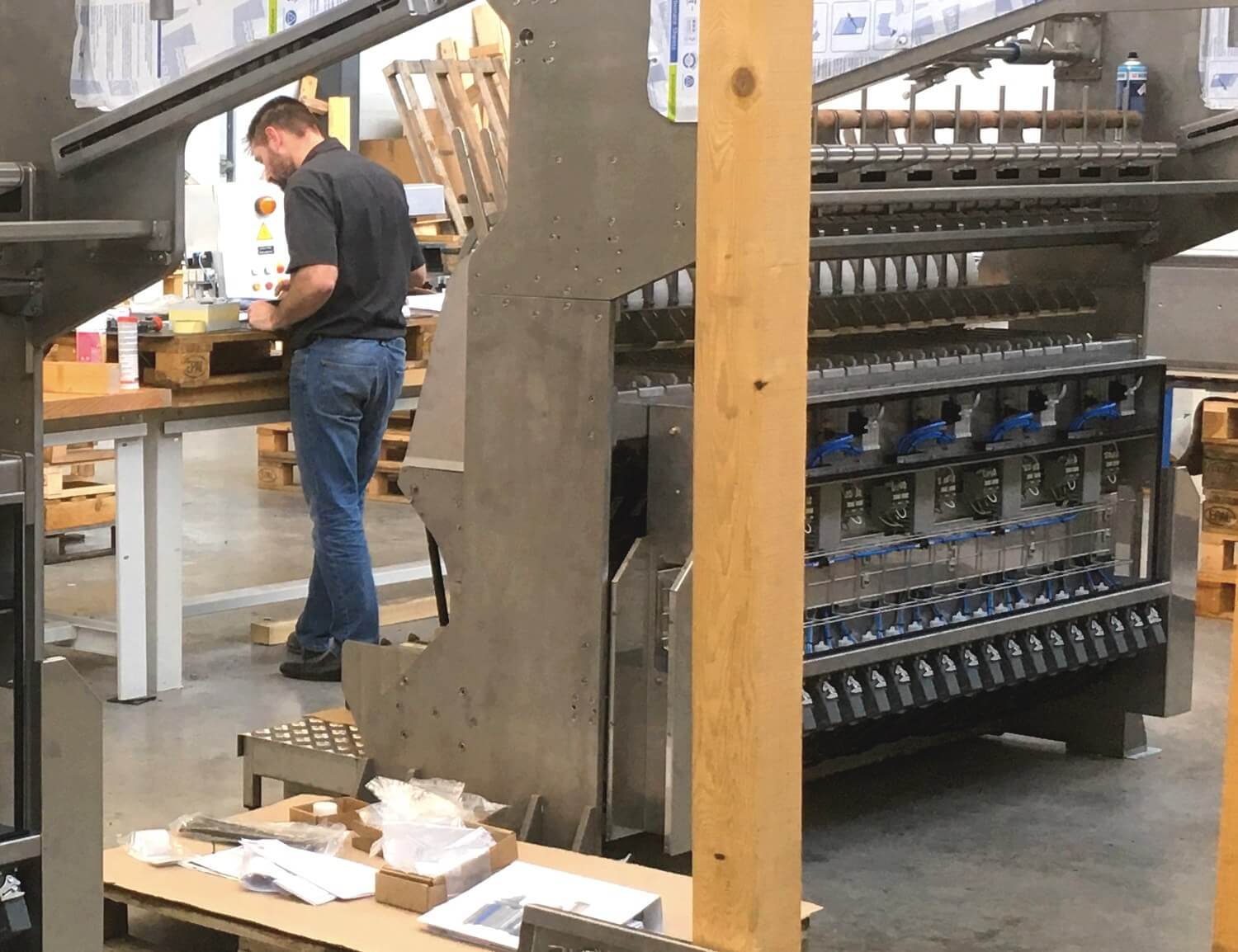
Mechanical assembly of all dimensions
Our assembly capacity, space and resources cover a wide range of needs:
- Assembly of complete equipment weighing several tons and several meters: machines equipped with large mechanical welds for the chassis, for example. The various handling equipment we have at our disposal (overhead crane, forklift) assist us in handling heavy and bulky assemblies.
- Assembly of tools, grippers or any system with small parts and precision adjustments
- Checking all mounting interfaces of parts, assemblies and accessories
- Reception of your parts or equipment for disassembly, transformation, modification, adjusting or installation in a new assembly. Reassembly and testing once modified.
Wiring, piping, quality marking
We ensure the electrical and pneumatic wiring of our machines with care:
- Separation of the power part and the communication part in the electrical connections,
- Networks and components identified precisely and durably in accordance with the electrical technical diagram,
- Organized, protected, attached cable and pipe routing.
This rigor provides our customers with the guarantee of a reliable, organized and visually finished machine. It also facilitates maintenance during interventions.
Our machines are equipped with standard or custom-made labels and information plates. They are glued, screwed or riveted near the area concerned and allow the durable display of various instructions, limits, settings, warnings related to safety, to be transmitted to the person using or working on the equipment.
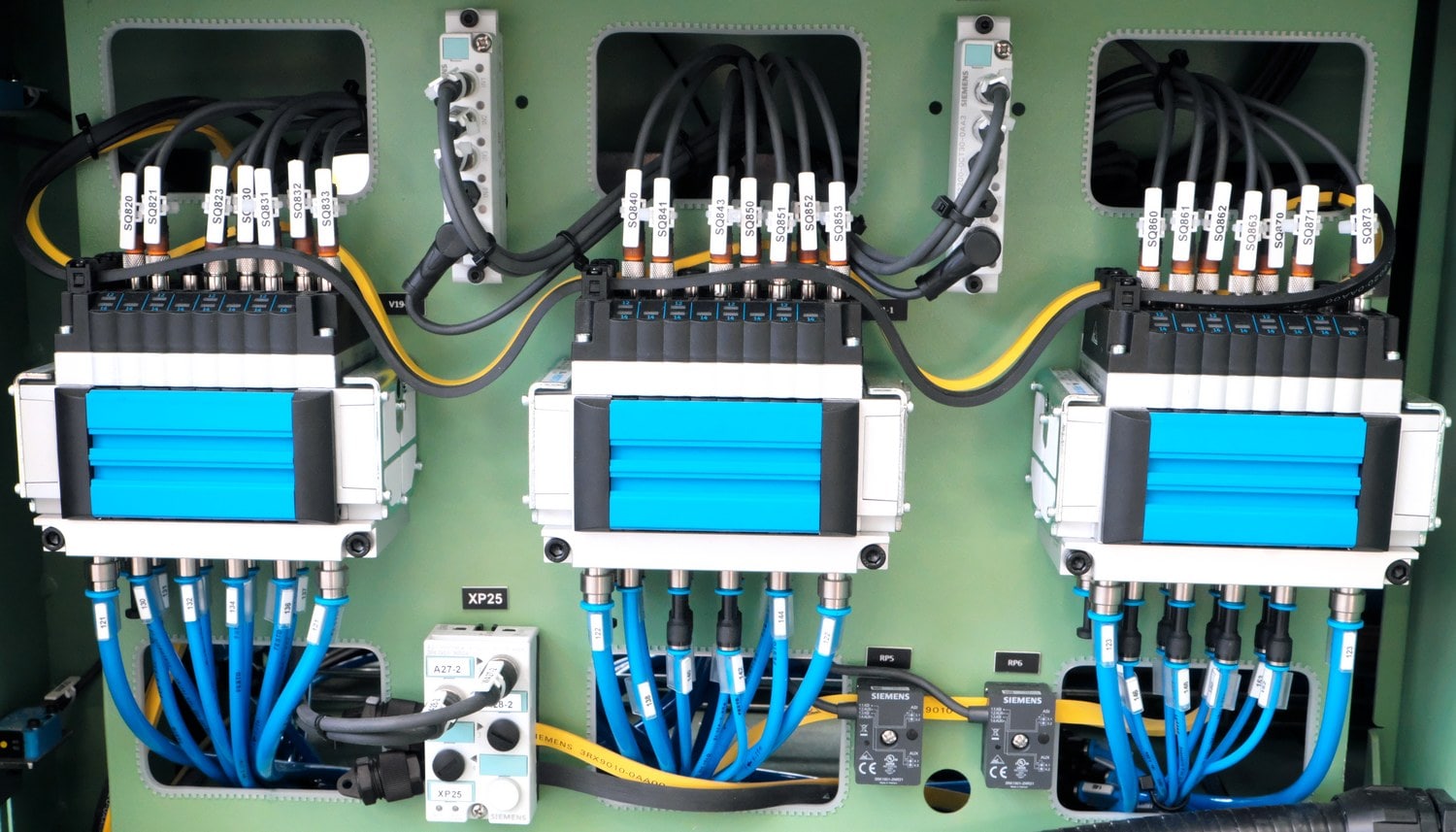
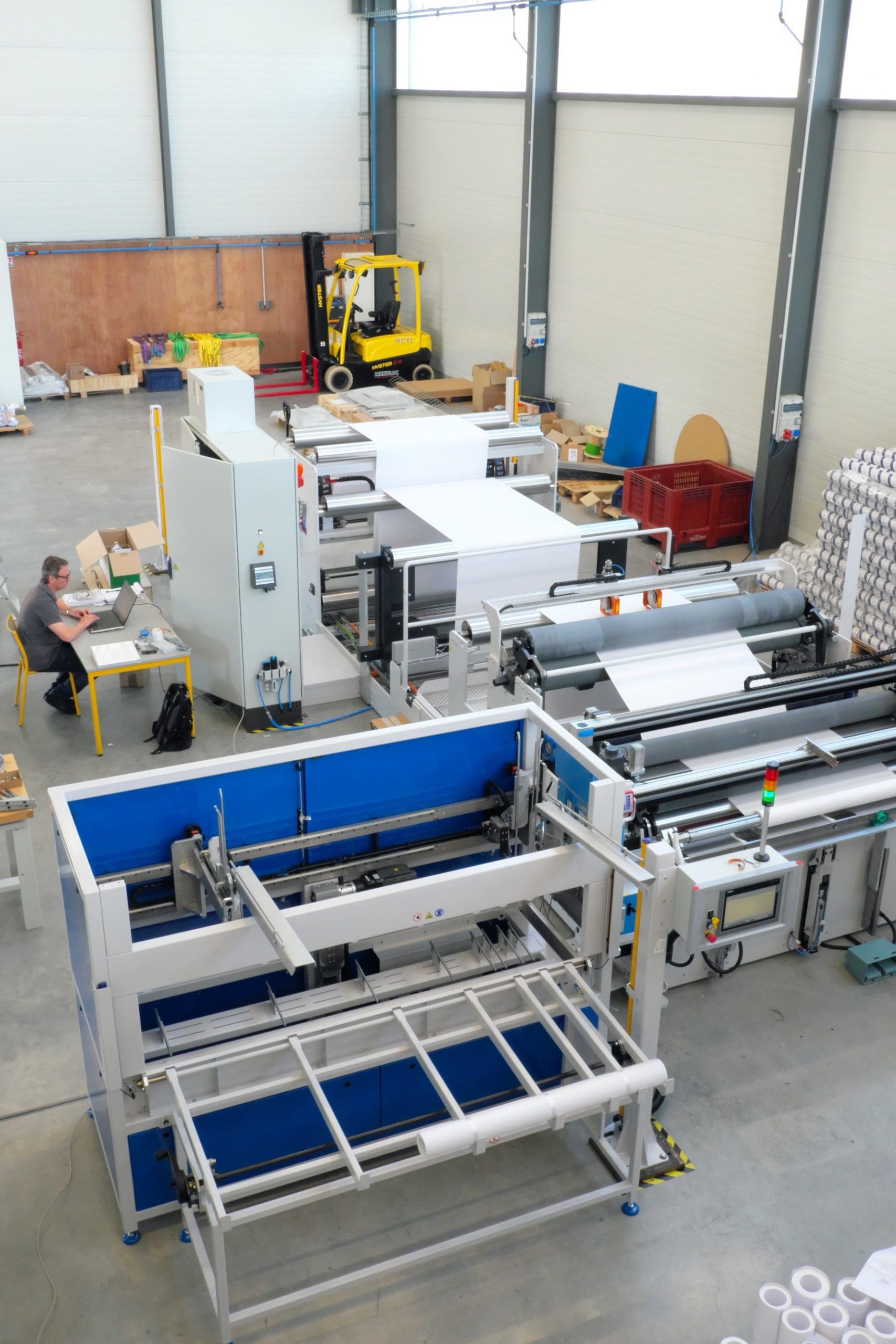
Guaranteed commissioning
In order to guarantee the operation of the equipment in your company, we usually test them in our premises before shipping. This important step before installation in your premises allows us to validate the operation and settings with your products and provides answers to any final questions.
If the machine requires PLC or robot programming, we take care of and validate operation and the various settings and adjustments directly in our assembly hall, adjacent to the office:
- Adjustment of alignments, positioning, movements and mechanical stops
- Adjusting strokes and speeds of cylinders and other actuators
- Configuration of servo motors: initialisation, speed and acceleration, position or torque control
We also test the machine’s various operating modes and grafcet sequences: initialisation, automatic cycle, emptying, manual mode, etc. Tests for changing series or thinking about optimising the machine’s cycle times can be carried out during this stage.
The machine can be delivered once we
Once we deem the machine functional, it is ready for acceptance.
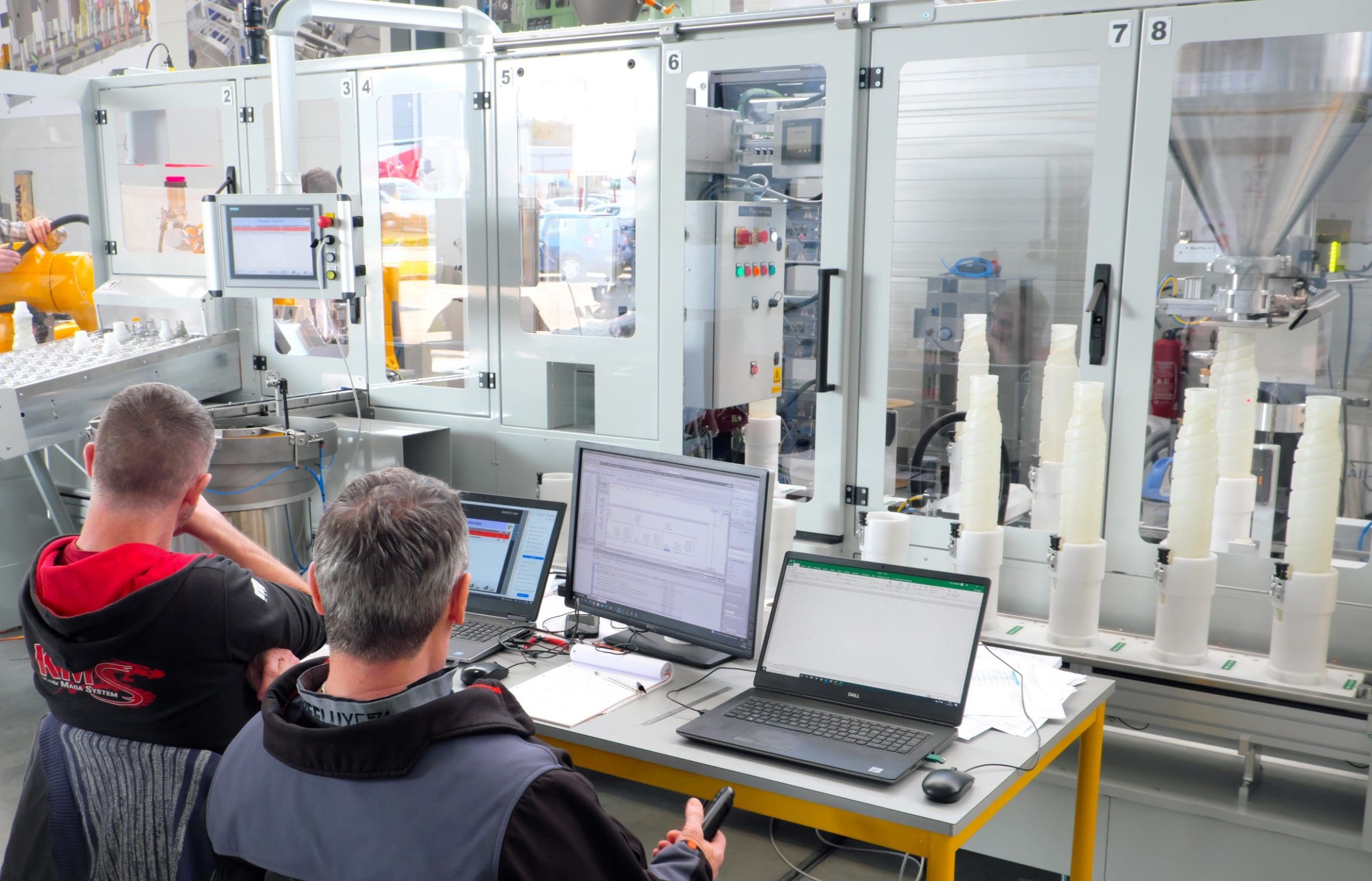
Reception at our premises
Once the machine has been fully assembled and programmed, you can come to our workshop for commissioning. This stage will allow you to fine-tune certain parameters according to your experience, and will give you the guarantee of a machine that meets your needs and can be used as soon as it is installed in your premises.
All our machines come with our manufacturer’s guarantee against any manufacturing defect. This guarantee is supplemented by CE certification of the machines, which indicates that they comply with current regulations. If required, an external inspection body can be called in to draw up a verification report. An identification plate is affixed to the machine, showing its designation, year of manufacture and CE certification.
Packaging, shipping and installation
For delivery, we provide the packaging, cushioning and handling supports required for each piece of equipment. Depending on their size and weight, our machines and equipment can be transported by van, semi-trailer or container.
We transport products by land, sea and air, depending on space, cost and timing constraints. We can produce packaging in wooden crates, with watertight covers, to meet the requirements of sea or air freight for overseas deliveries.
Once your equipment has been handled by our crane or forklift and placed on its transport vehicle, it’s ready to be delivered to your business.
The next step will be installation, commissioning and training by our teams on your premises.
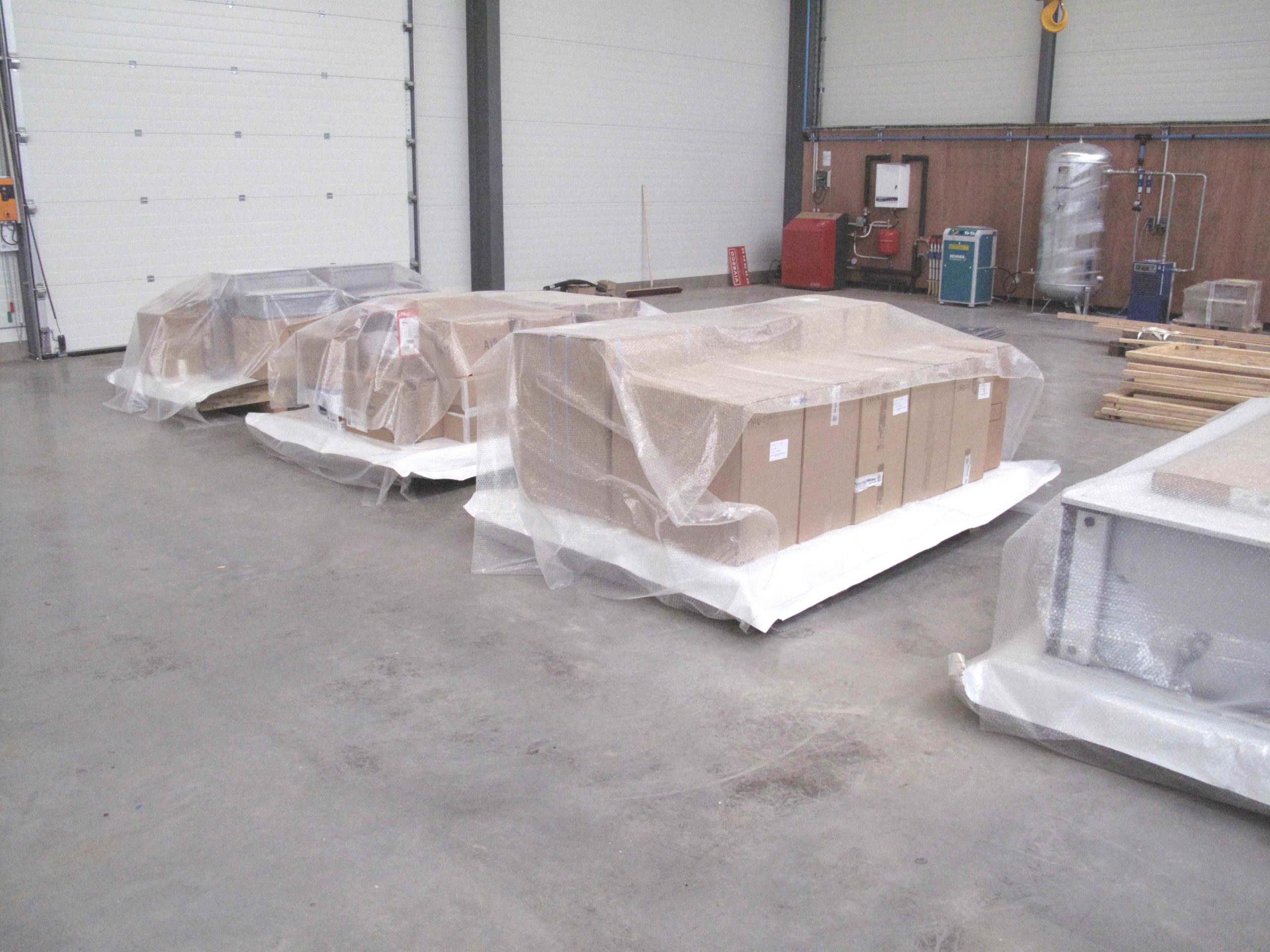
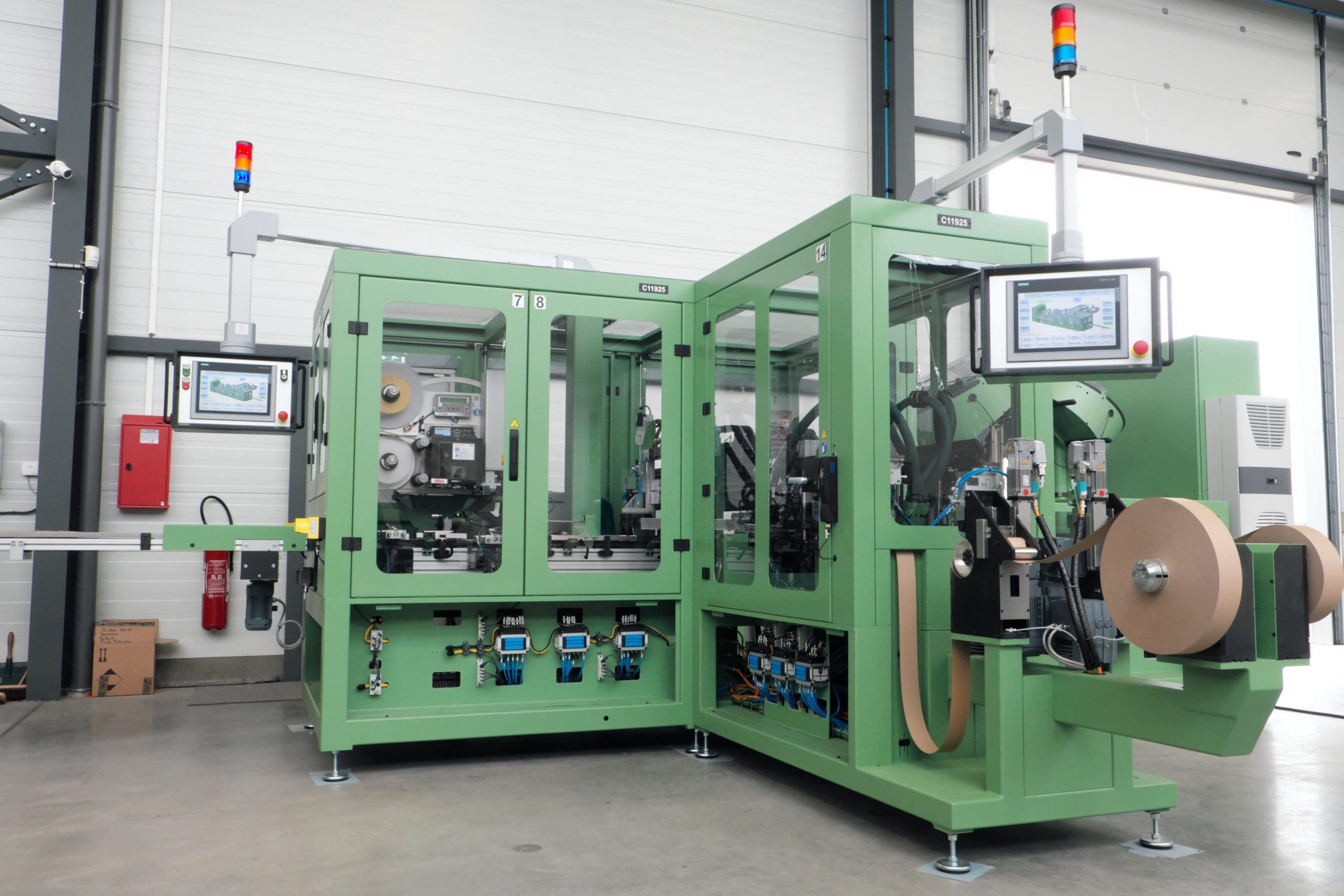
SMI, the answer to your machine needs
Design, manufacturing, installation
Do you have an idea for a project but do not have the skills to make it happen? Tell us about your needs, we will be able to provide a complete response ranging from support in writing the specifications to mechanical assembly, delivery and installation in your premises. We cover all types of special requirements, ranging from simple tools to machines or complete production lines.
Do you have a study and would like to obtain an external opinion in order to carry it out? Are you looking for implementation solutions to bring your project to fruition?
We can support you in finalising your design and launching component purchasing. We can receive them at our facility and carry out the assembly and fine-tuning of your assemblies.
An idea? A machine testing concept?
We design prototypes to test concepts and ideas. We custom design and create a system adapted to your needs while optimizing its cost.
The installation takes place in our assembly hall, providing all the necessary comfort and equipment to carry out various tests, modifications, and adjustments.
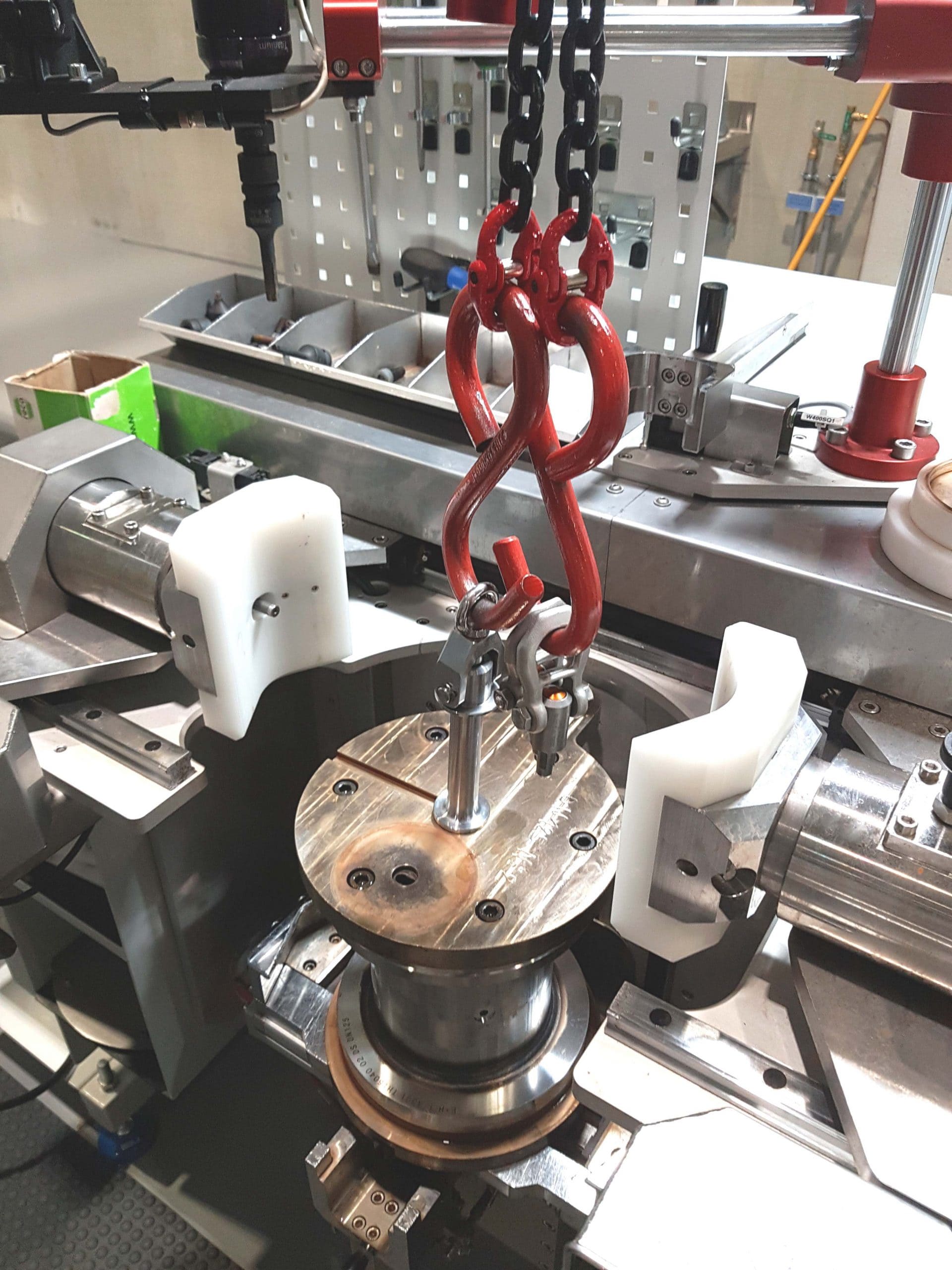