Measurements and controls
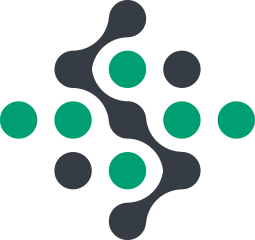
Controlling and measuring product characteristics
Are you looking to make your equipment or production more reliable? Would you like to improve the quality and consistency of your manufacturing or assembly processes?
SMI is your partner of choice in the Grand-Est region to help you with all your projects involving the selection, integration or creation and implementation of measurement and control equipment.
We are a design office based in the Vosges, in the heart of the north-east quarter of France. We offer detection and monitoring solutions to be integrated into machines. We also develop complete control equipment for all industrial companies in the Grand-Est region, Alsace, France and abroad.
We take a neutral look at your problems and select the best technologies and products to meet your detection, monitoring and measurement needs. We also create complete, innovative solutions when existing equipment reaches its limits.
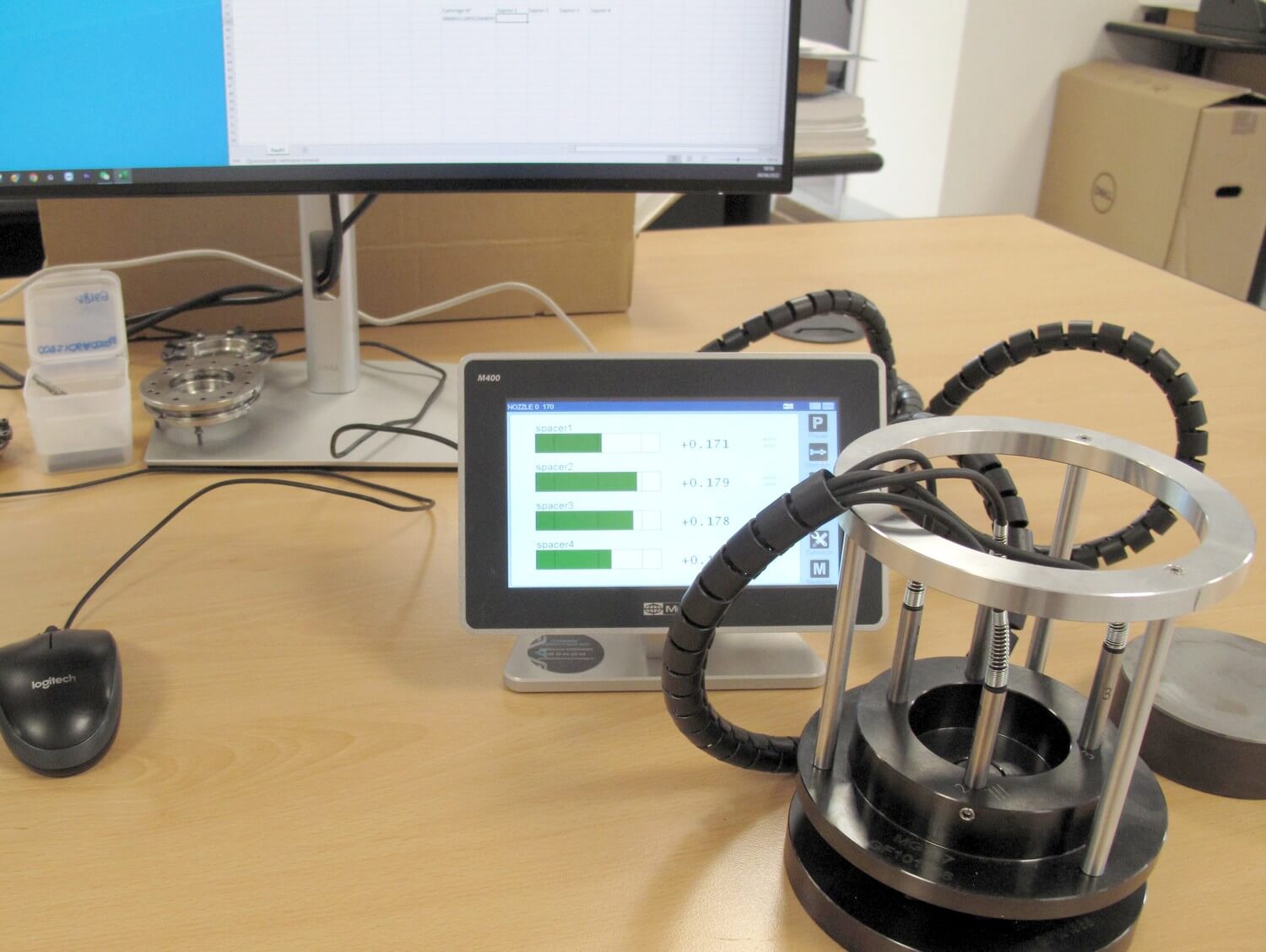
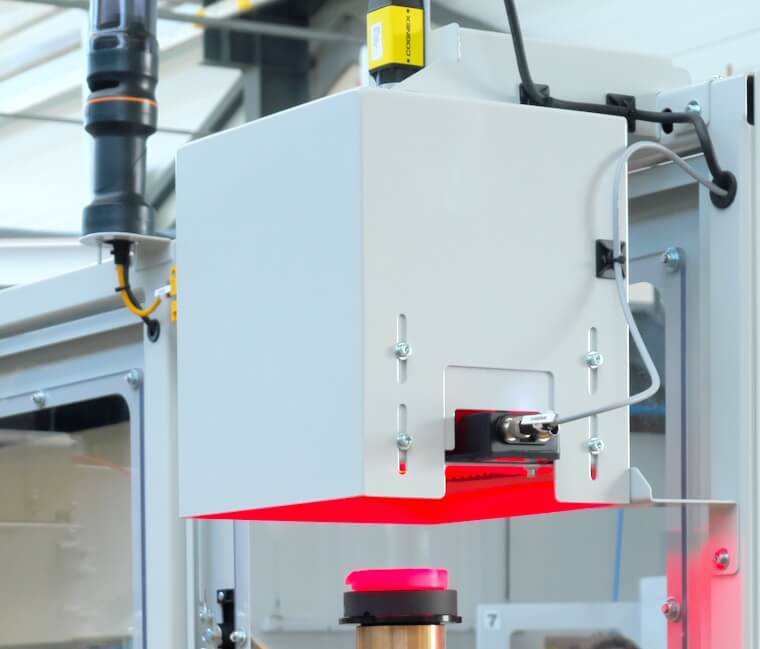
Our expertise at your service
It’s sometimes difficult to choose the right type of sensor, the right product range and the right technology for a given application.
We are experienced in researching and selecting or creating technical solutions to meet your needs. Depending on the manufacturing range, it is often vital to detect an anomaly as early as possible in the process on the production line. This means that the part in question can be evacuated immediately, avoiding the need to carry out a series of operations on a product that will ultimately be defective.
Depending on the characteristics you want to monitor, we define the appropriate system, equipment, sensors and detection principles to measure the right quantities. We work with you to establish how the information collected is to be presented, stored, transmitted to other systems, etc. We also define the thresholds or levels above which an alert or alarm is to be generated. This signalling of an anomaly enables the operator to react quickly and appropriately to restore correct operation.
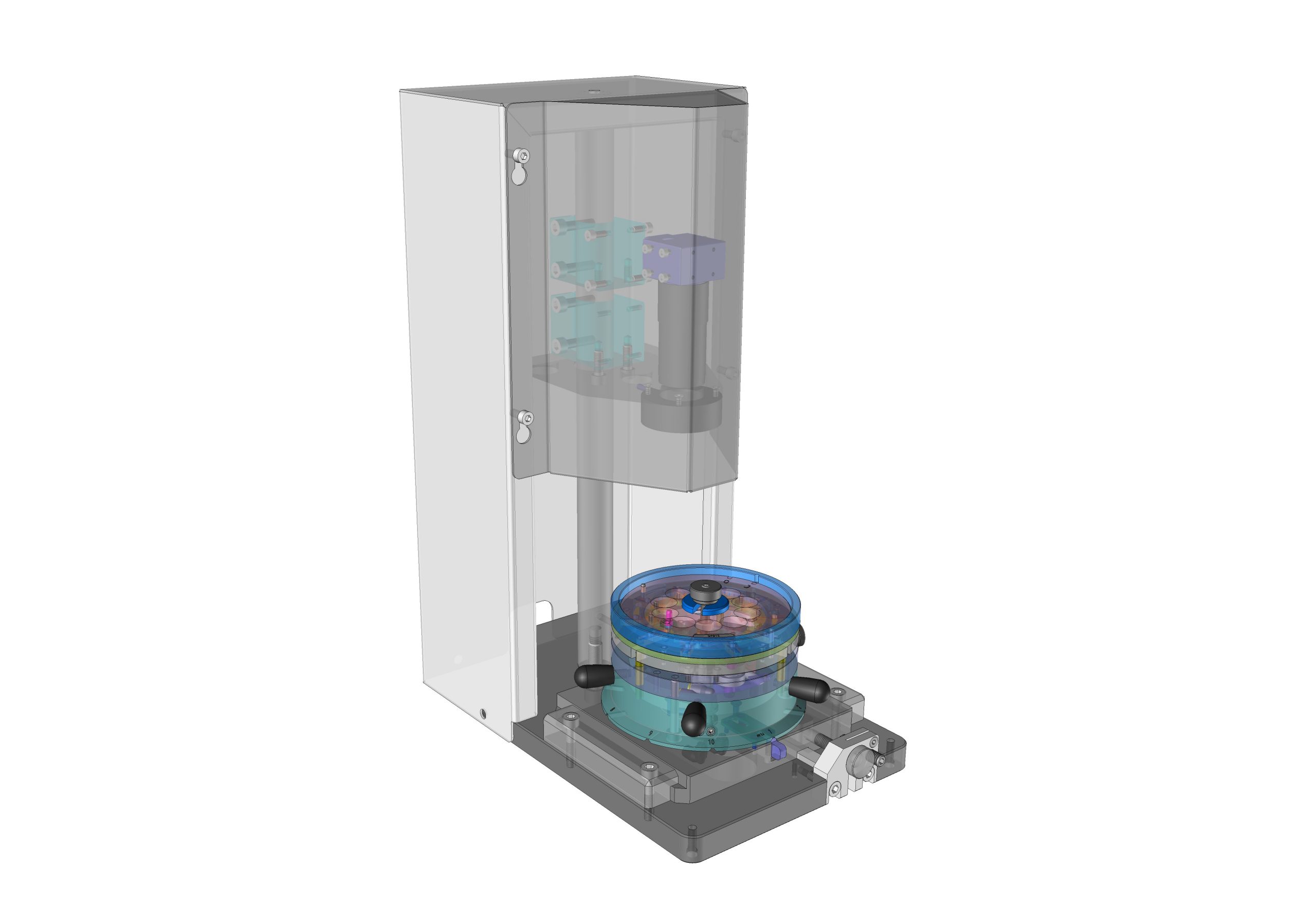
Examples of acquisitions and measurements :
Here are a few examples of how control functions can be integrated into production equipment:
- Weighing and dosing of products
- Counting of parts, presence verification
- Recording and plotting of force/displacement curve during riveting or clipping
- Determination of part lengths for validation at the machine exit
- Electrical continuity testing
- Monitoring of temperature, pressure, flow, speed
- Deformation verification during the manufacturing process
- Single beat acquisition system on a loaded part with a specially developed fluid bearing (repeatability < 0.5 µm)
Integration of visions controls
Depending on the application and the elements to be inspected, we are able to integrate and program functions using machine vision. This inspection method uses, a camera, lighting, software, and image analysis tools, all of which we define and program.
Here are some examples of applications that allow us to evaluate a characteristic and determine product conformity:
- Dimensional control, part length, distance between parts, gap measurements
- Geometric control, part orientation, part misalignment
- Verification of component distribution and positioning
- Integration of suitable lighting
- Design of backlights and specific lighting systems
- Leak detection through image comparison
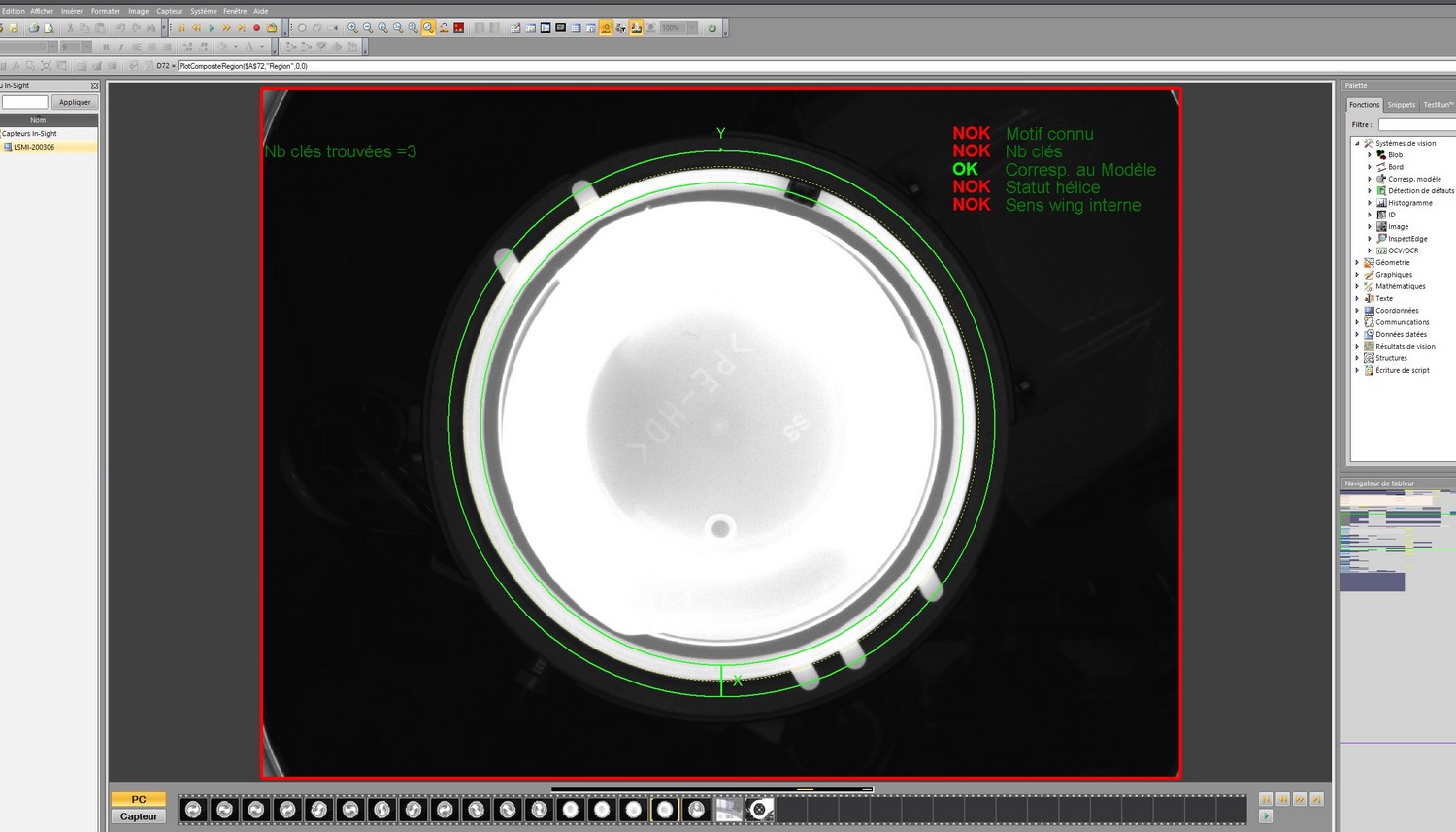
In pictures
Creation of new equipment or machines to specifications
Industrial production is subject to increasingly stringent requirements for precision, quality, and consistency. This necessitates the use of high-performance machines equipped with technologies that enable the measurement and quantification of key characteristics to ensure the quality of the final products.
When designing a special-purpose machine, we almost always integrate hardware, sensors, and monitoring systems to track important characteristics of the product processed by the equipment. Data acquisition allows for complete control of equipment operation, the collection of useful and necessary information for diagnostics, or for understanding phenomena and deviations.
With the measured data, it is also possible to automate certain adjustments or compensations. It becomes possible to track defect rates, frequency of defect occurrences, and the affected components. All these analyses are very helpful for defining the right settings, finding effective improvement solutions, and ensuring controlled, high-quality production.
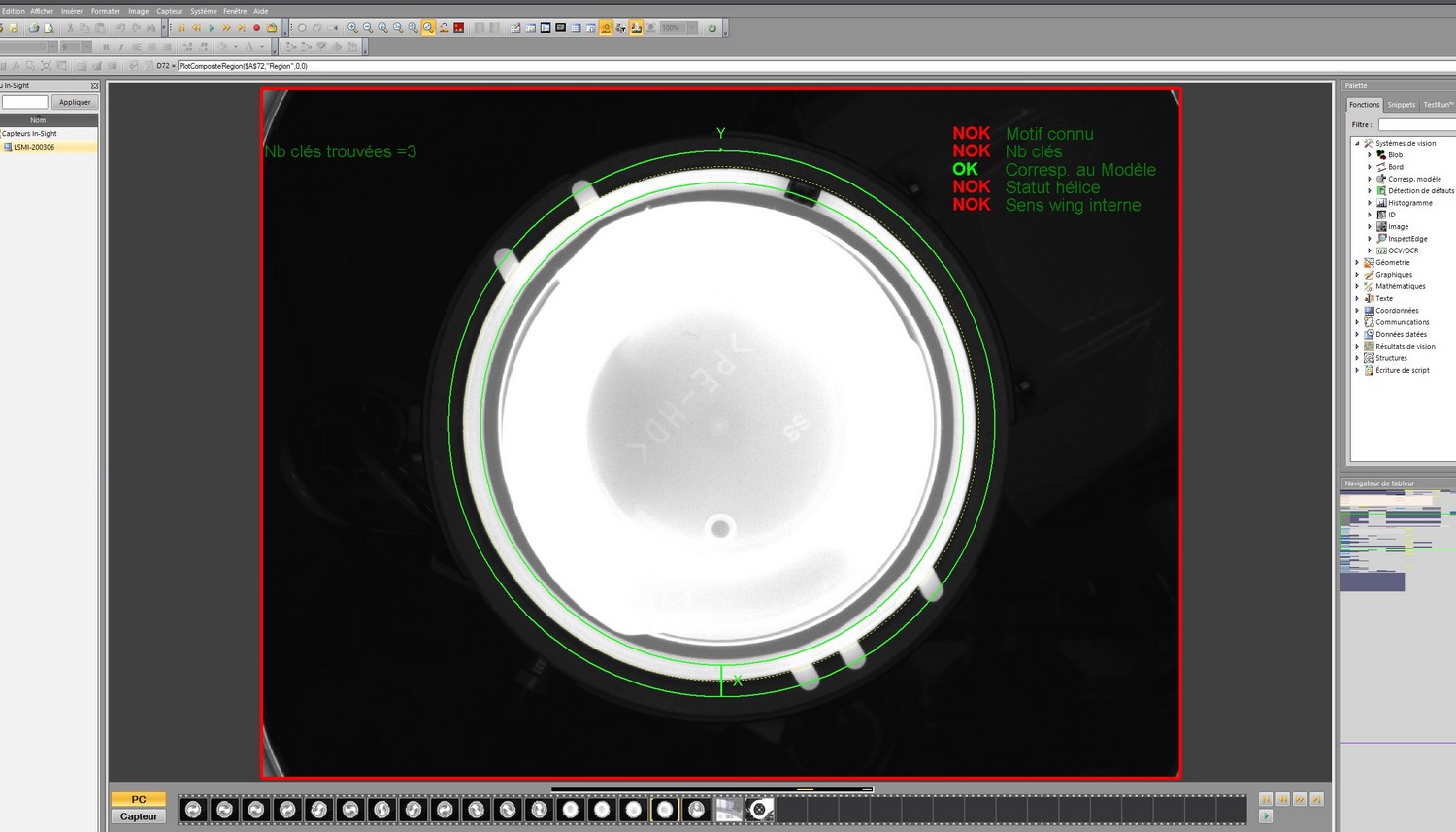
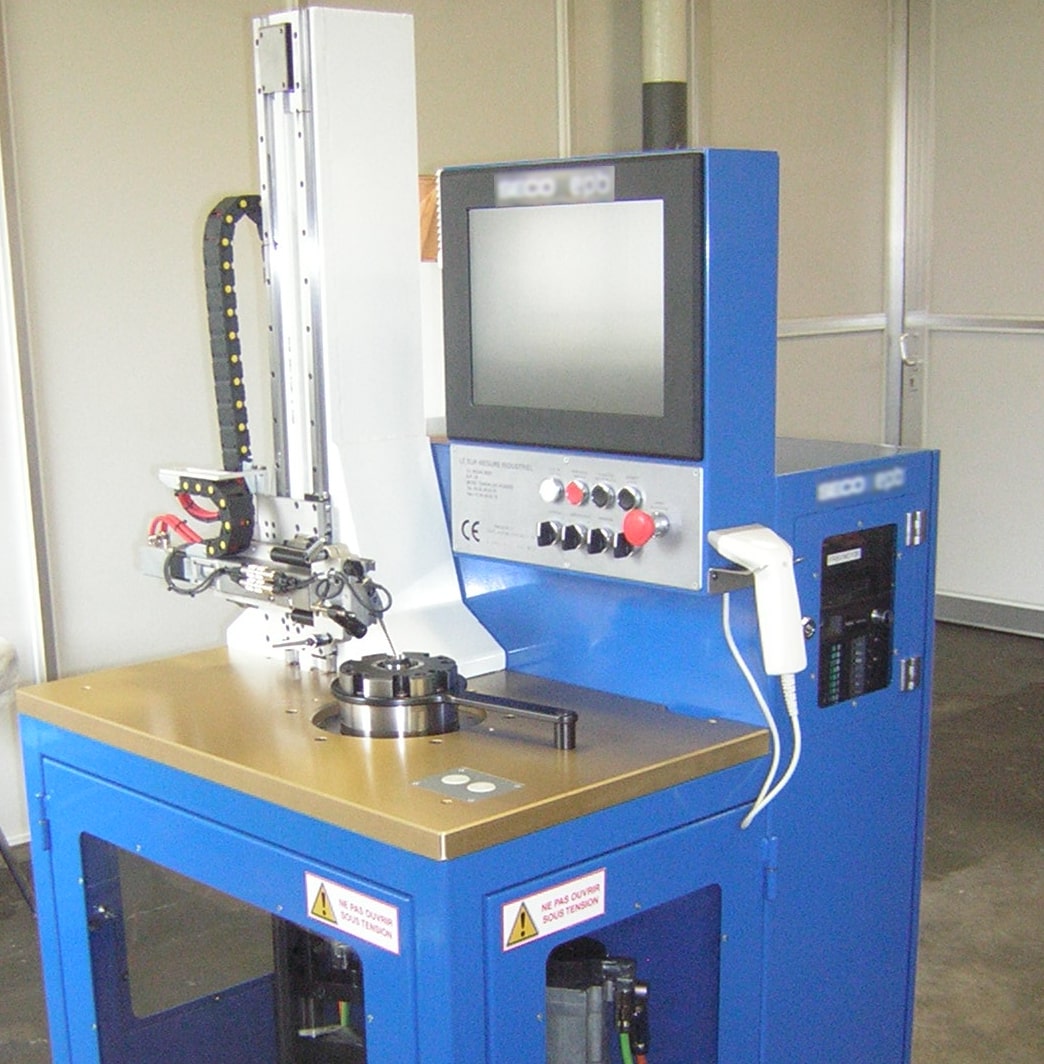
Evolution and improvement of existing machines
We also frequently work on upgrading existing equipment or production lines by adding new measurement and monitoring functionalities.
Some machines operate without real control over quality or settings. Others rely solely on the expertise of employees who possess the know-how required for their proper functioning. With the invaluable expertise of these individuals, we support you in choosing, integrating, and programming new control, monitoring, and quality verification solutions.
By using our services, you can automate tedious, repetitive inspections that are often prone to errors. By integrating relevant control systems, whether systematic or not, we help you make verifications more reliable, reducing reliance on visual interpretation alone.
Our engineers and technicians have a comprehensive view of the range of equipment that will meet your needs. With the right detection method, you will obtain rational, reliable, measurable, quantifiable, and actionable data.
Development of solutions from A to Z
Tools have been fully studied, designed, and manufactured by us to integrate an ultra-precise air jet distance measurement technology, meeting the specifications of our client.
The measurement within these tools allows for the validation, with precision under a micron, of the positioning of components before their final assembly by welding. The high integration constraints, the required precision, the geometry of the parts, and the surrounding context led us to develop this innovative solution in order to meet the technological challenges presented by the request.
For other applications, the selection of the right detector, device, or sensor enables us to design the system that meets the requirements.
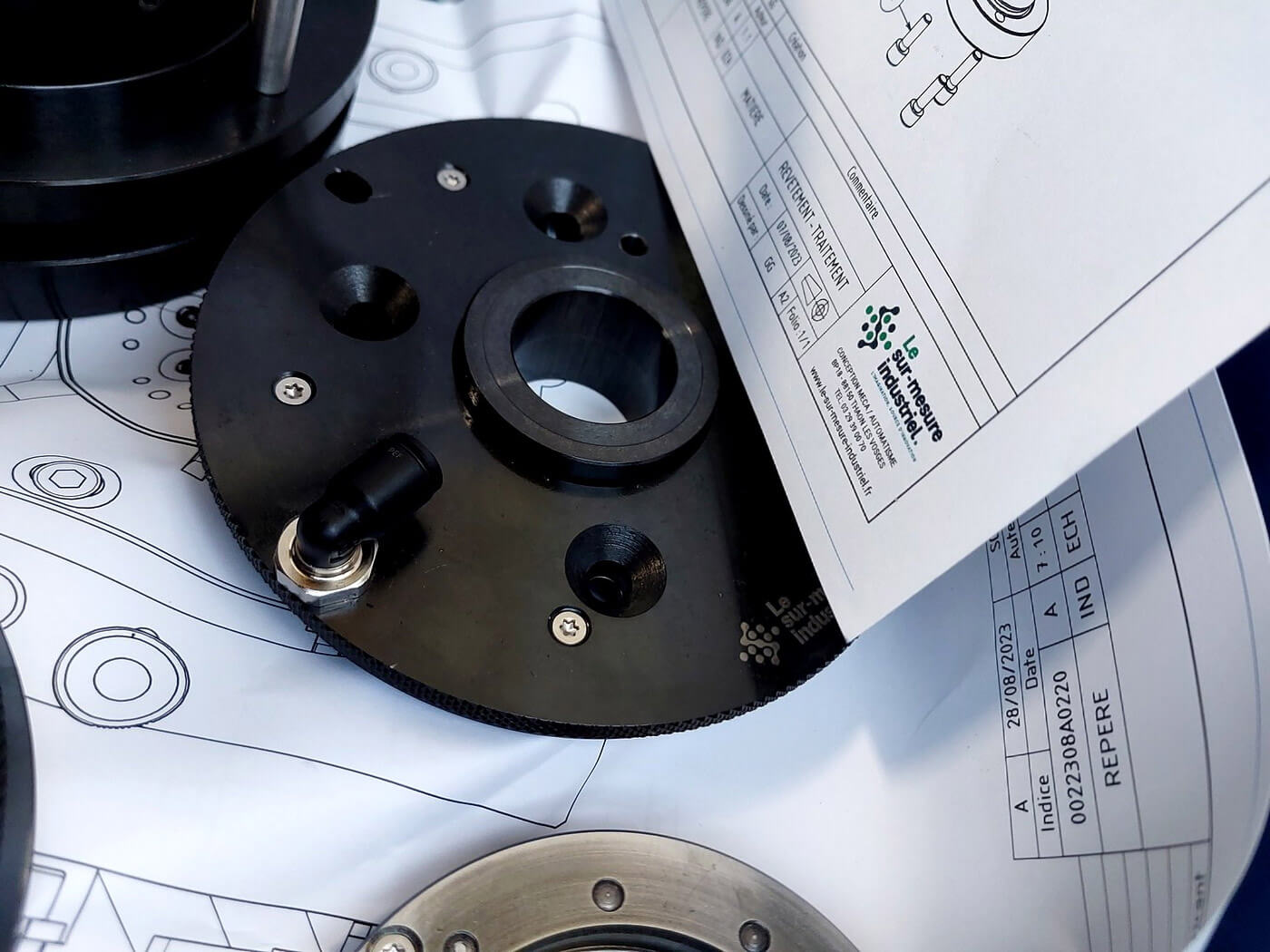
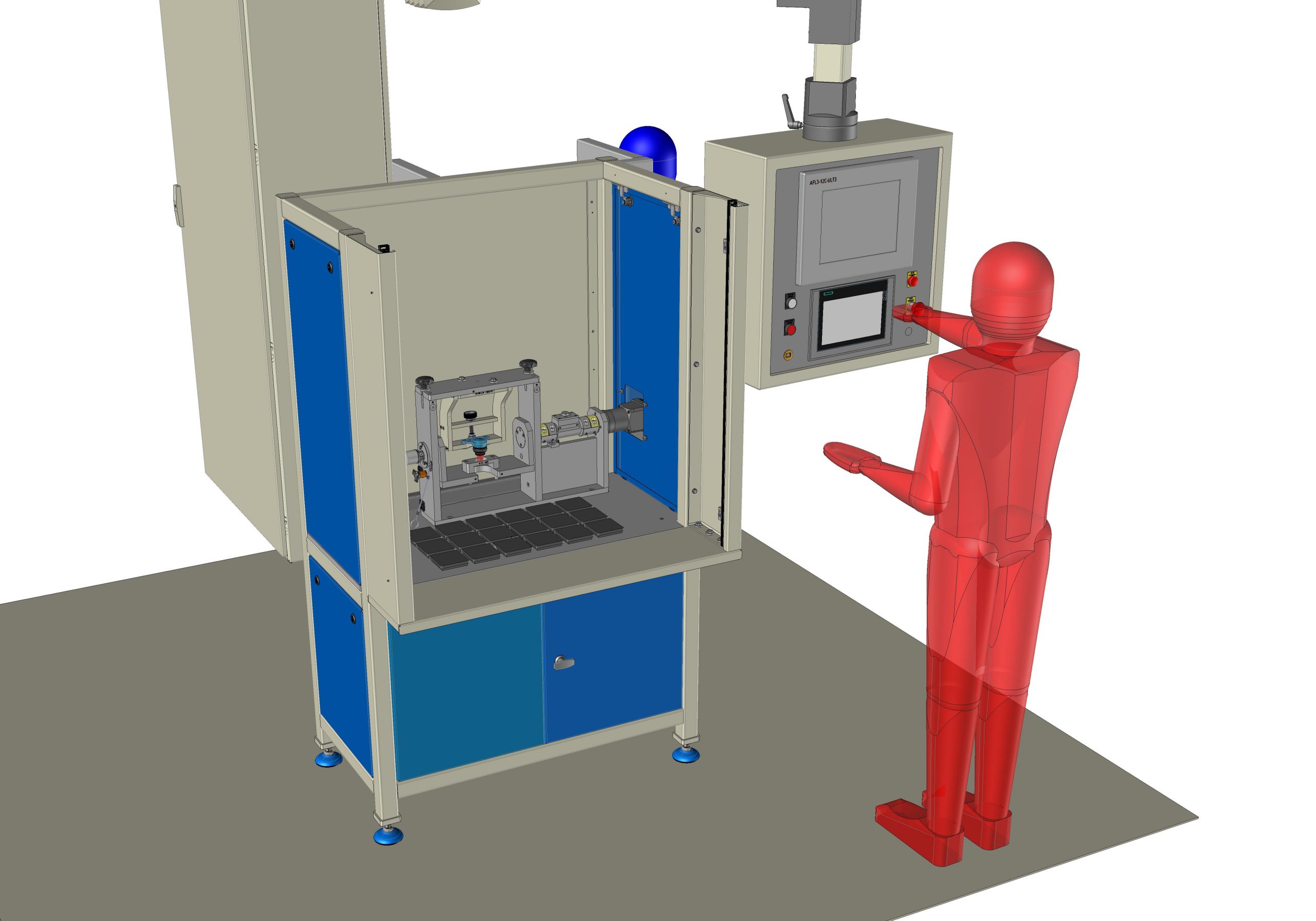
Testbeds
Testbeds developments are other examples that use all types of sensors and detectors for the quantification and recording of monitored parameters during tests. Depending on the different testing conditions, these test devices enable the collection of valuable information to characterize and qualify a product.
Recording of temperature, forces, vibrations, deformations, pressures, flow rates, component positions, speeds, etc.