Testbed
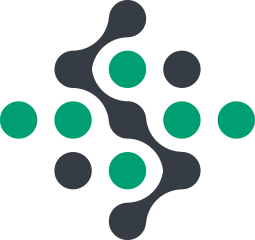
Development of testbeds
SMI supports you in the design of test systems, control equipment and complete test benches, thanks to the varied skills of our team.
With more than 30 years of experience in mechanical design, industrial automation, physical measurements and data acquisition, we develop from A to Z according to your needs instrumented, robust and precise test systems.
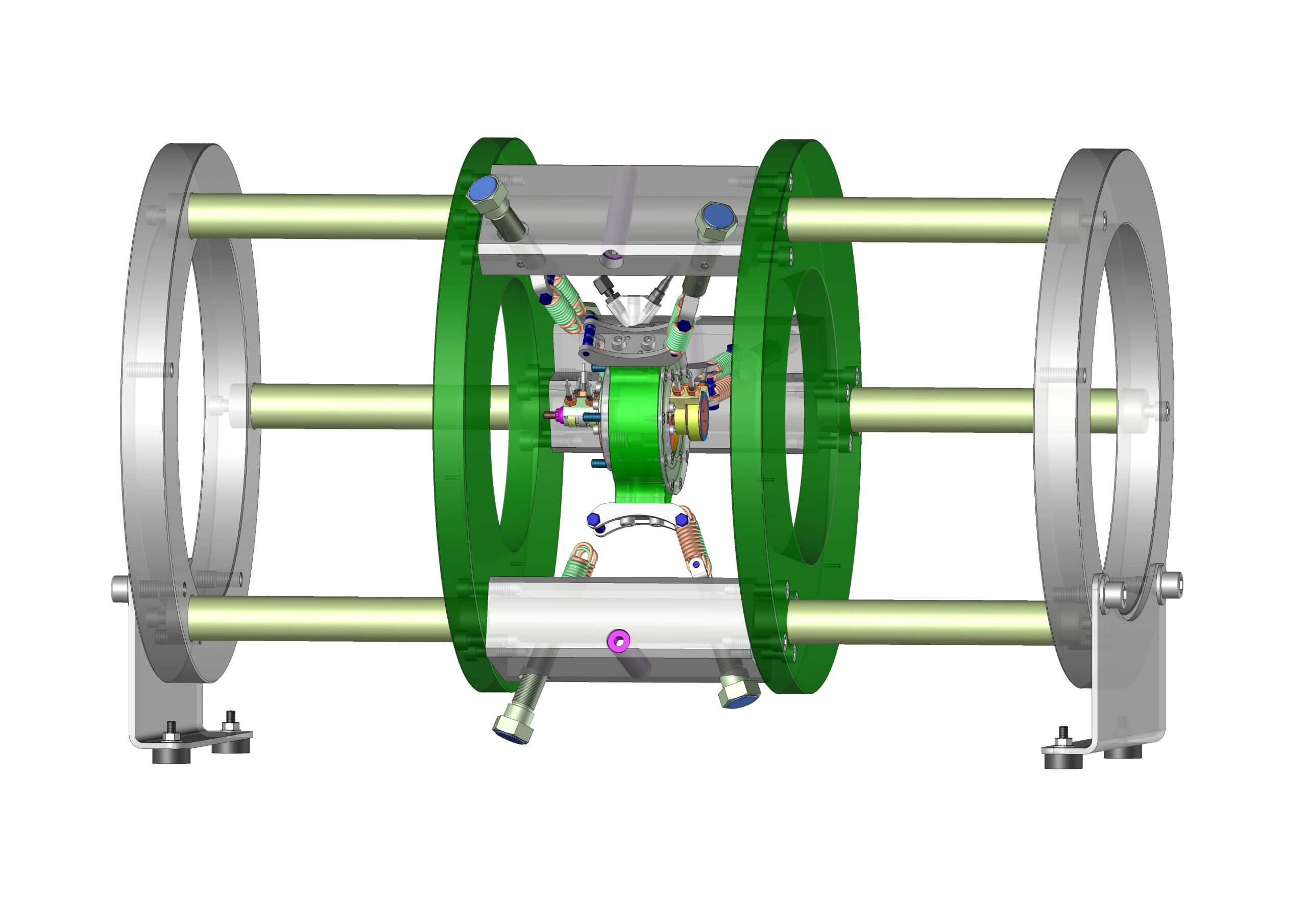
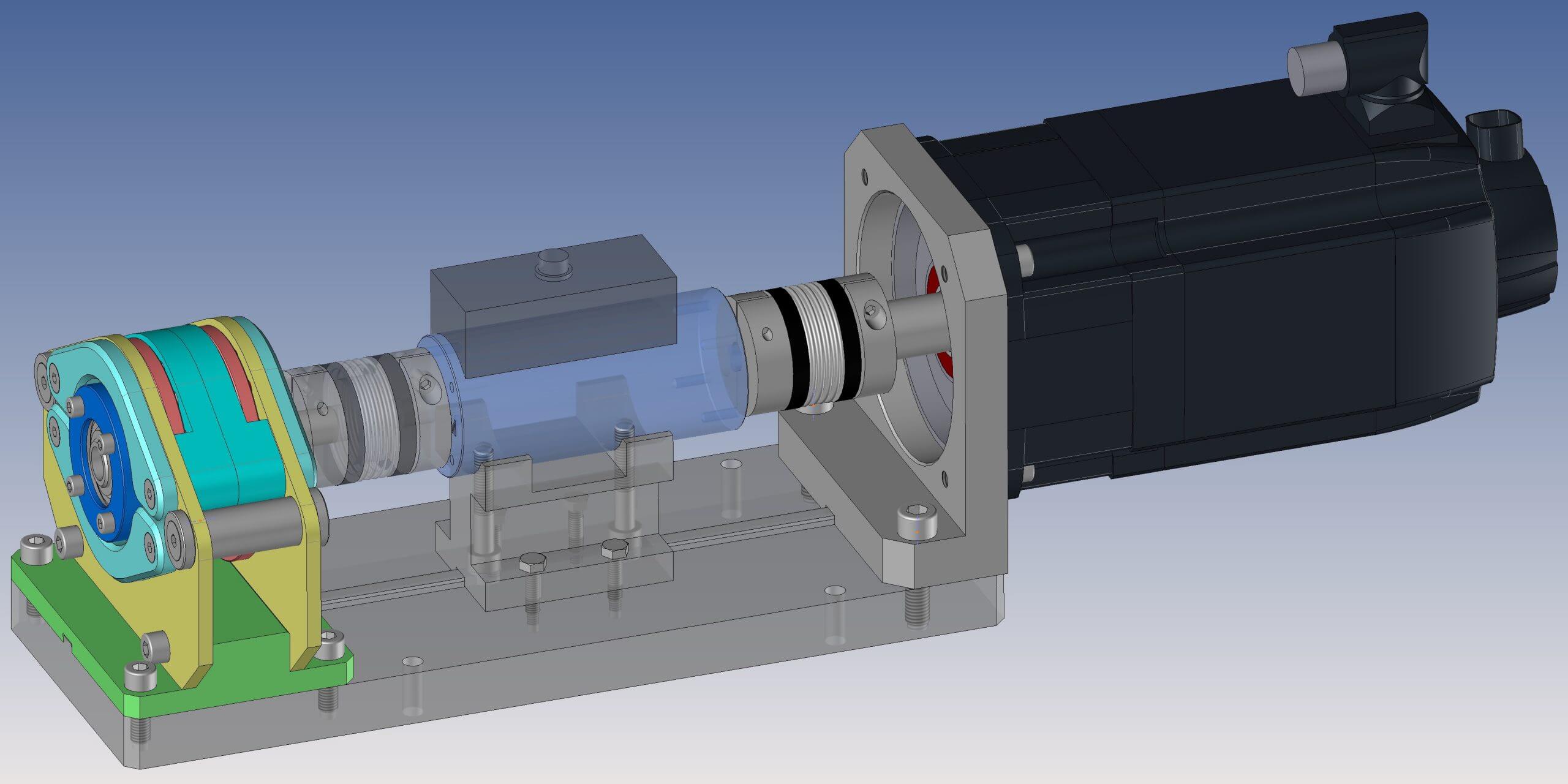
- Digital simulation occupies a very important place in companies today and offers fantastic prediction capabilities. However, it is necessary to recalibrate a model with real tests, because not all physical parameters can be modelled with certainty (fatigue laws, thermal cycles, cracking phenomena, oxidation of parts, etc.)
- The physical quantity to be measured cannot be modelled, the system is too complex or you do not have the necessary software and resources (license cost, complex training)
- You want to quickly identify the parameters influencing your product from an empirical point of view, in order to provide pragmatic solutions to your need.
Depending on the quantities to be monitored, the parameters to be tested and the precision sought, we choose and offer you the appropriate principles and materials. We establish a quote for the service according to your needs (complete new equipment, modernization of existing equipment, instrumentation only, etc.)
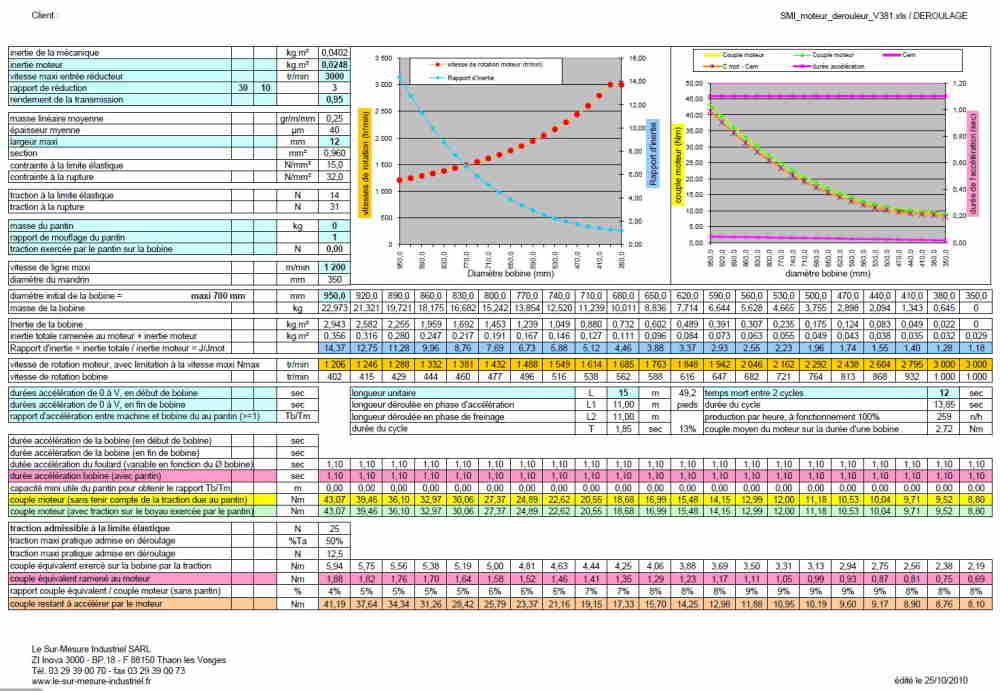
Data acquisition
The dynamics of your system that will guide the choice of the type of data acquisition. We support you in defining the equipment adapted to the tests you wish to carry out.
The signal sampling rate is the factor that will determine the equipment to use. The higher it is (several kHz or MHz), the higher the cost of the installation will be. Below these frequencies, the equipment is generally inexpensive. For good quality data extraction, it is generally practiced to choose cards 10x faster than the frequency of the phenomenon.
We guide you in defining the equipment according to the number of channels, whether they must be multiplexed, whether the acquisition must be simultaneous or sequential, etc.
Quantities to be measured, technologies and sensors
Generally speaking, it is necessary to distinguish between 2 major categories of technology. Contact and non-contact measurements. Both solutions have their advantages and disadvantages: the first is always less expensive and often easier to set up, but nevertheless represents disadvantages that the second overcomes: heating of the sensor due to contact, wear of the sensor or of the part to be measured, interaction of the sensor on the measurement itself.
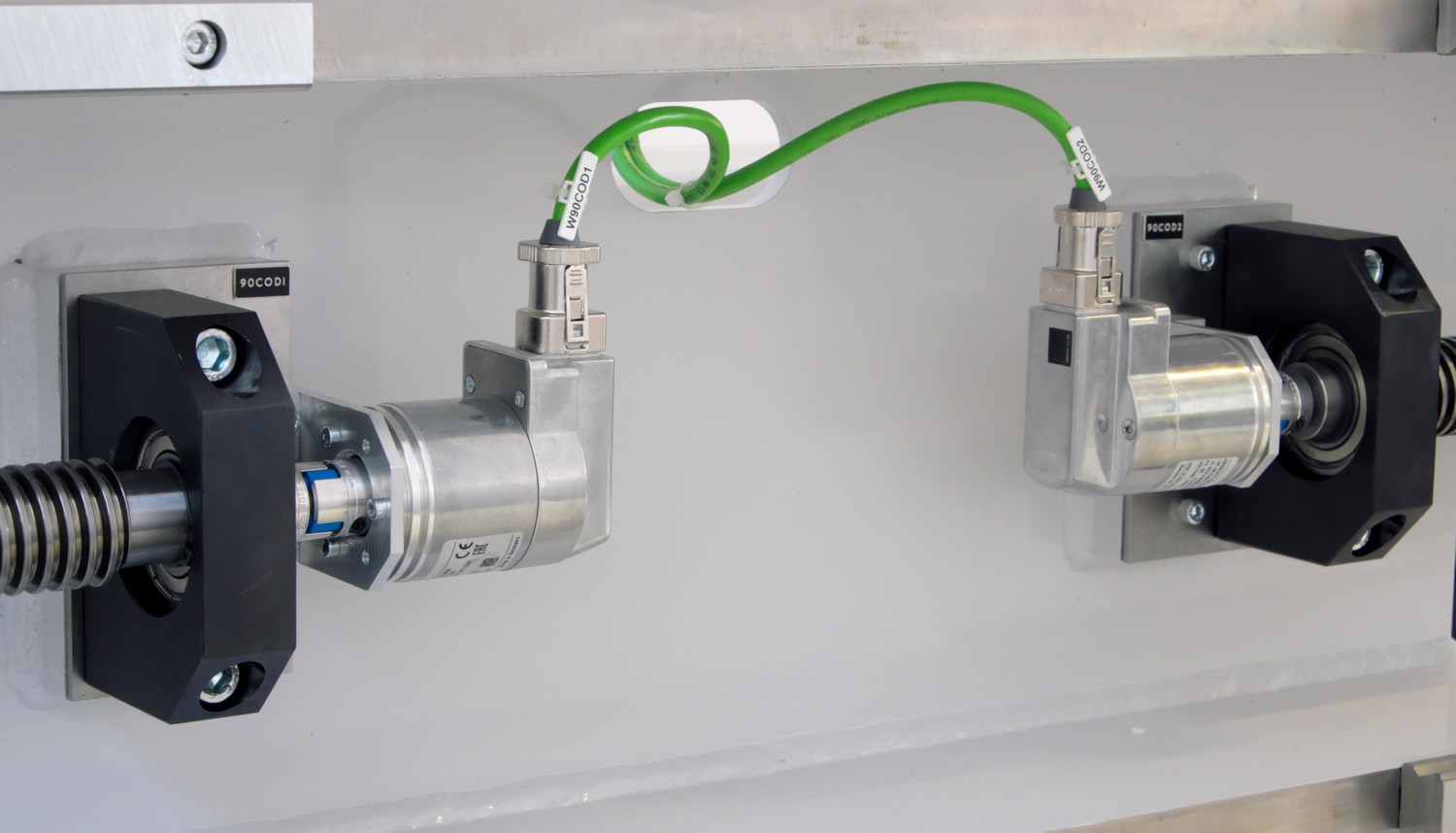
Overview of current technologies on some measurable quantities:
- Torque: use of a torque meter, static or rotating. We also design non-contact and indirect measurement systems, using force cells. Frictionless systems are developed so that friction does not disturb the value read. In the ultra-precise case of high-speed rotating machines, it is possible to carry out a strain gauge technique on the rotating shaft communicating in telemetry by a transmitter bulb and a static receiver.
- Speed: it is almost the most common to achieve, in low speed rotating machines, the use of contact brushes is common. This technique is on the decline for the reasons mentioned above. In the majority of cases, the use of non-contact proximity sensors or magnets generating a rotating field is predominant. Modern sensors directly give analogue or digital signals proportional to the speed. In the case of more difficult to achieve or laboratory-type measurements, the FFT of a periodic signal is calculated.
- Force: it will be necessary to distinguish static measurements where gauge bridge type sensors are used, from dynamic measurements in which piezoelectric type sensors are found.
- Temperature: the most common sensors are thermocouples, thermistors, and PT100. These phenomena are generally slow, of the order of hertz, and do not require an expensive acquisition card. In very specific cases requiring contactless, optical or laser measurement technologies can be used.
- Distance: here it will be necessary to distinguish between contact measurements using LVDT type sensors (probes), capacitive and inductive sensors or even laser. A wide range of suppliers exists as well as a wide range of use and precision to be chosen carefully according to the applications.
- Pressure: the technology is similar to that of force sensors and we help you choose the type of sensor between static and dynamic pressure, depending on the frequency of the phenomenon and the type of media.
- Level measurement: depending on your application, a bimetallic sensor type may be suitable if a high or low level threshold is expected. In the case of continuous acquisition, we will guide you towards the selection of a capacitive or ultrasonic sensor for example.
- Flow measurement: depending on your company’s sector of activity, the type of fluid (water, air, oil, refrigerant gas or other, etc.), we select the best type of device for you. Choice: Hot wire flow meter, often used on vehicles, rotary turbine or Coriolis flow meter on benches, they will meet the needs in all types of flow measurement (mass or volume) and all precision ranges depending on the application.
- Acceleration: the accelerometer allows the measurement of vibrations, shock, acceleration of a mobile, the detection of faults in machines, on one or 3 axes simultaneously. The most widespread accelerometer is the piezoelectric which allows measurements in a wide range of frequencies and with great compactness.
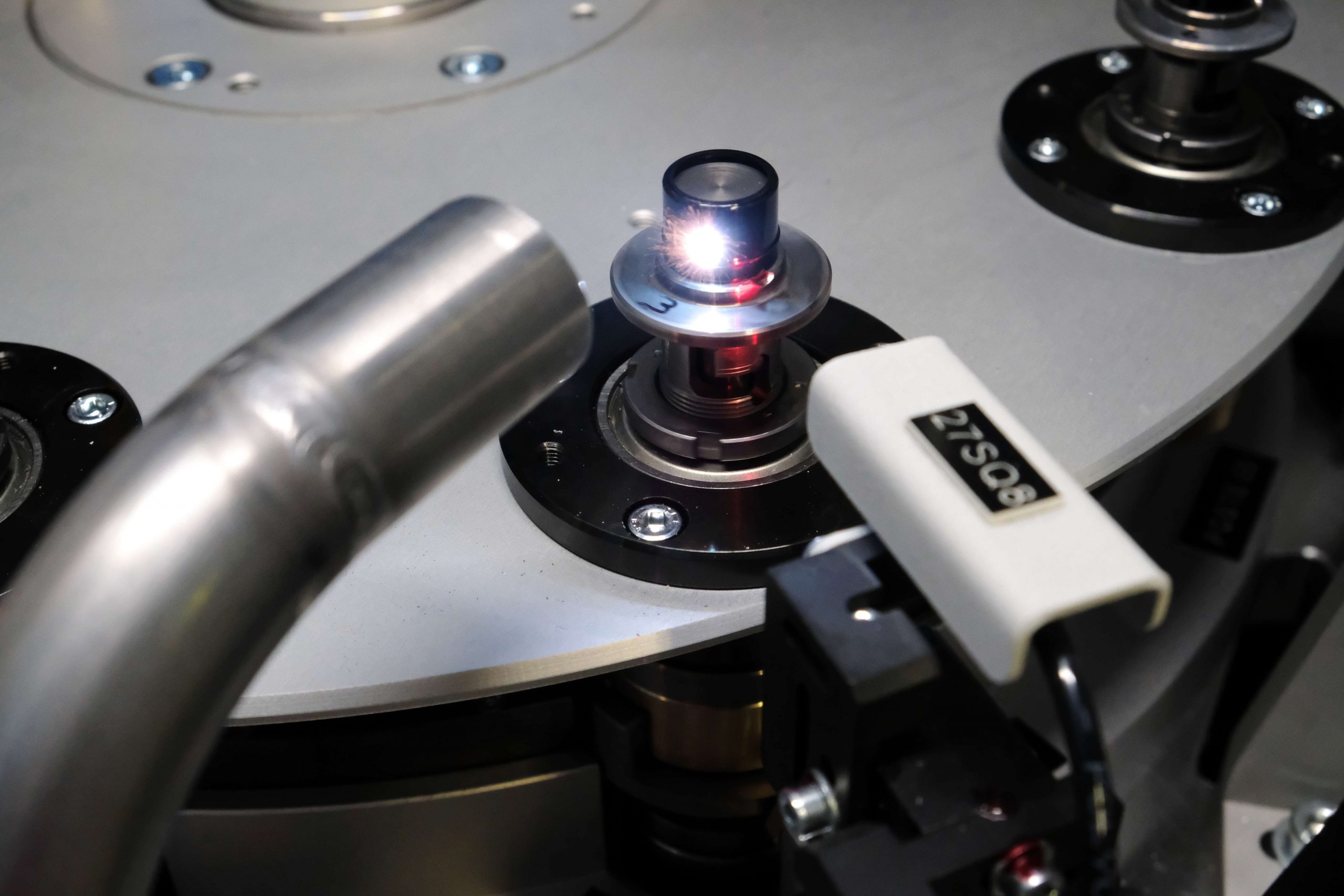
Our main testbeds achievements
For the automotive, food, aeronautics, pharmaceutical and medical industry, we design and produce a variety of test benches and provide a precise and reliable response for your measurements and tests.
- Vibration transmissibility test bench: For the development of high-speed rotating machines, we have created a test facility allowing the speeding up of a shaft mounted on fluid bearings, and the measurement of operating pressures and temperatures. Using accelerometers, synchronous and sub-synchronous vibrations are measured and the rotating unbalance is identified by the influence coefficient method.
- Resistant torque test bench: in the leisure sector, we developed this bench in order to know the resistant torque generated for the braking of large zip line trolleys, according to the different influence parameters. Indeed, depending on the slope of the cable and the weight of the passenger, a braking configuration is sometimes required. This bench, entirely designed, programmed and instrumented by us, allowed us to build braking charts for our client. But also to carry out data acquisitions in order to measure the heating of the rollers according to the speed. These experiments teach us more about the phenomena and the limits of use and then allow us to ensure a design that optimizes operation and maximizes the service life of the parts.
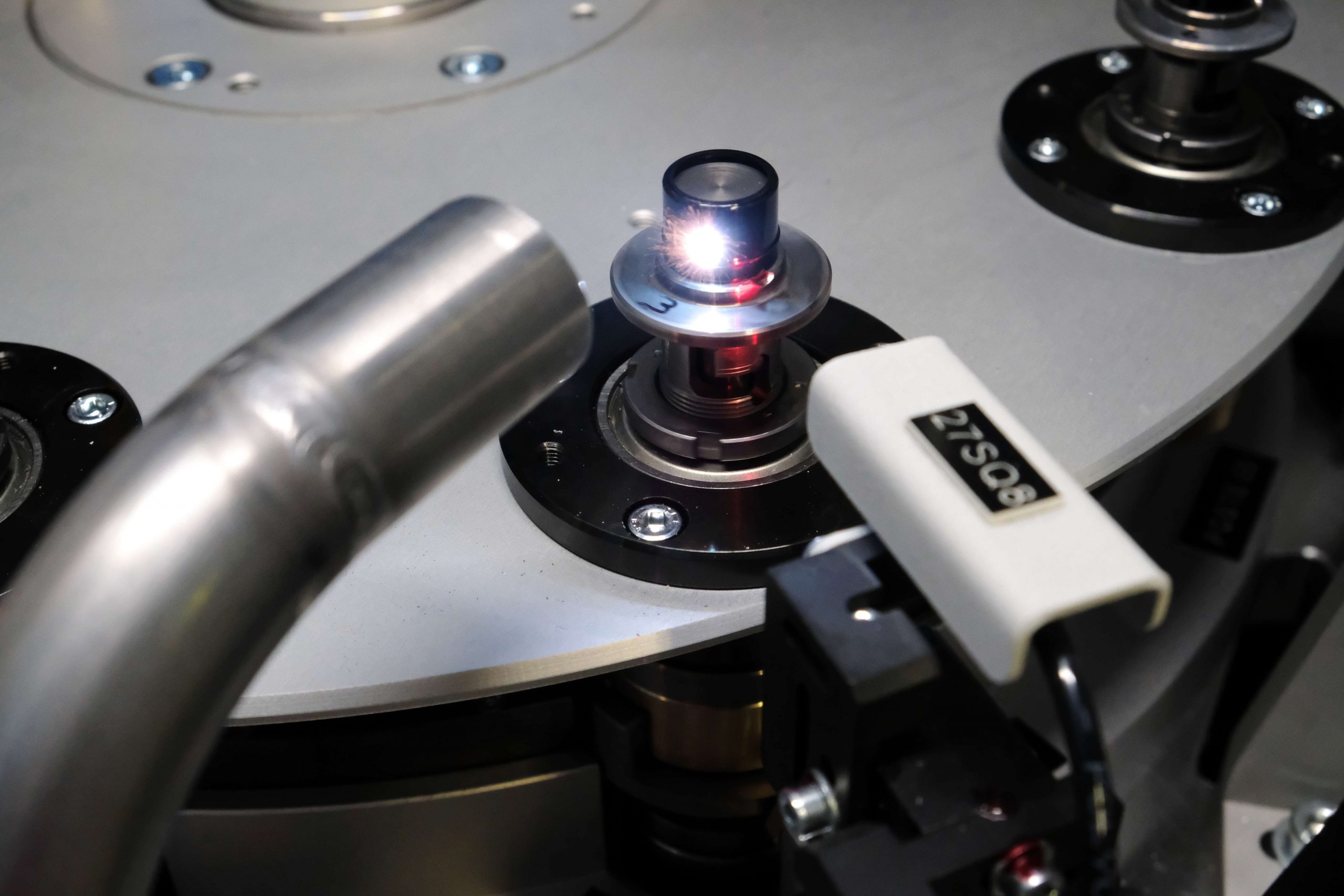
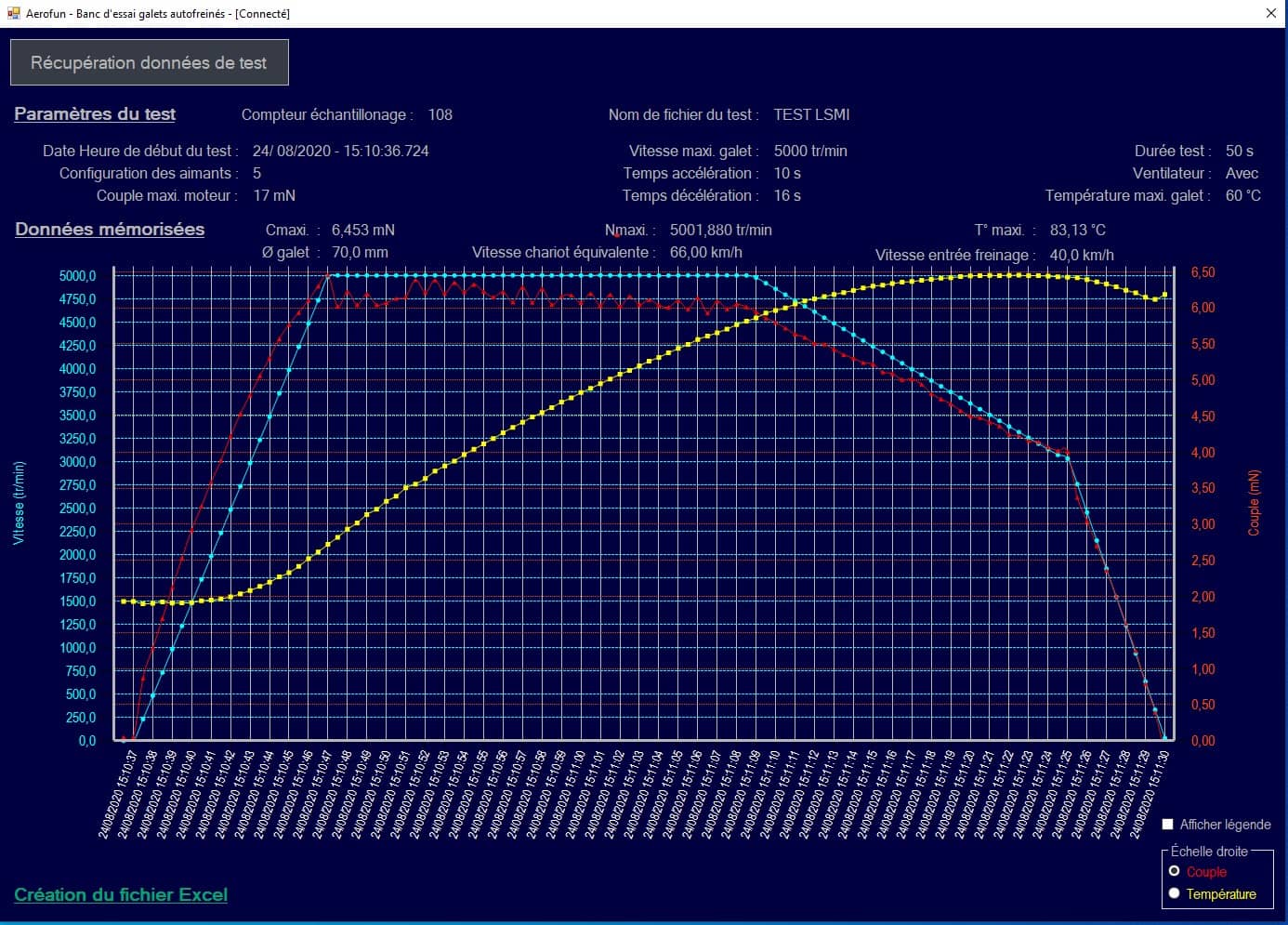
- Lifespan of automotive components: this test method enables the endurance testing of mechanical parts subjected to various kinematic stresses and in a saline environment at controlled temperature and humidity.
- Leak test bench in the medical environment: The parts are subjected to a control procedure defined by our customer, their resistance to bursting and their leak-tightness must be qualified. A recording and formatting of the test data is carried out automatically, in a file format chosen by the customer.
- Material bending strength test bench: in the steel industry, manufacturers want to test their different grades of material according to precise standards. We have therefore designed a test method enabling samples to be subjected to controlled loading in relation to their deformation. All encapsulated in a fully enclosed and secure machine, with data recording for post-processing and the creation of experimental charts.