Automated and robotised production line
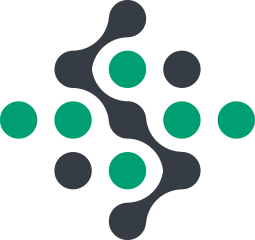
Integration and programming of industrial robots
- Technical comparison and choice of the brand and models best suited to the application
- Precise determination of references according to needs: load moved, requested rate, reachable work area, mechanical layout on the line, etc.
- Integration of robot arms into CAD and animation of the different work positions and trajectories.
- Programming of robot controllers, trajectories, management of product variants, management of safety zones and interfacing with the line’s PLC (inputs, outputs, safety loop, operating mode, etc.)
- Development to optimize cycle times, improve and make reliable exchanges with the line’s automation
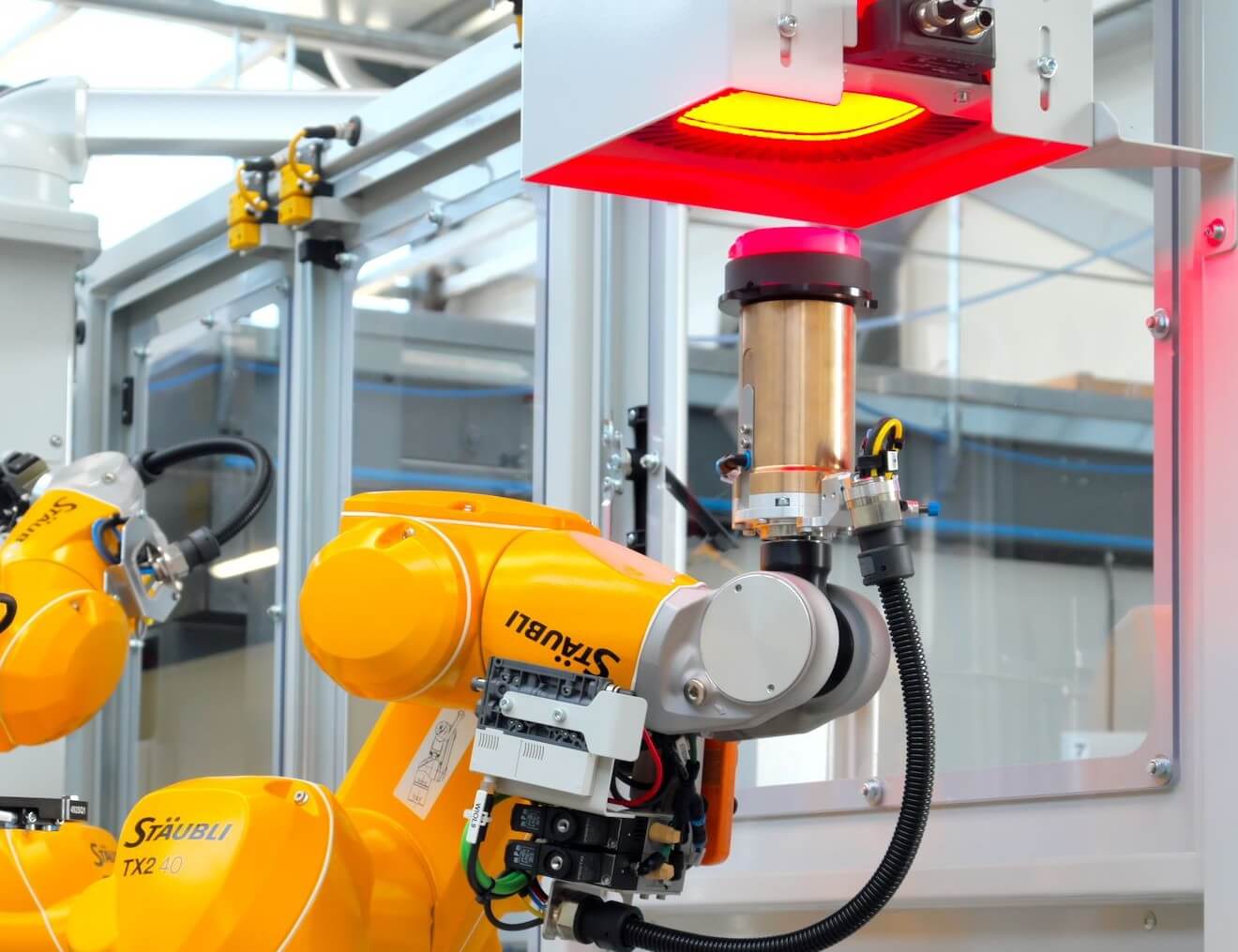
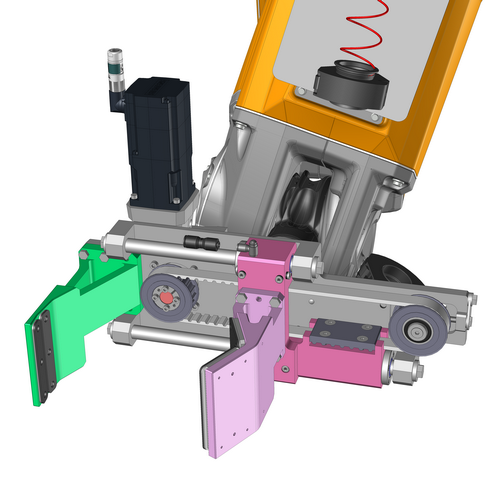
Development of very special grippers
- Suction cup gripper with vacuum level monitoring and clogging monitoring
- Pneumatic gripper with parallel jaws and special elastomer fingers
- Mechanical gripper controlled by a servo motor for managing positions and clamping forces on flexible products.
- Gripper with quickly interchangeable tools to adapt to different products. Telescopic degrees of freedom with pneumatic return for handling and free extension without releasing the part in the clipping station
Machine vision by camera
We also used and programmed different industrial cameras for this application. We also carefully tested and determined the most suitable lighting to guarantee the reliability and stability of the analyses. We then interfaced the cameras with the PLC for data communication and synchronization with other operations: program selection and parameter entry, shooting and transmission of the different results, fault and status communications.
- Deburring and positioning of parts: 100% of parts tested to validate that the model is correct and orient the part using the image and the robot manipulator.
- Quality check on positioning of parts after assembly, determination of acceptance criteria and thresholds, data recording to generate statistics.
- Leak detection by image comparison.
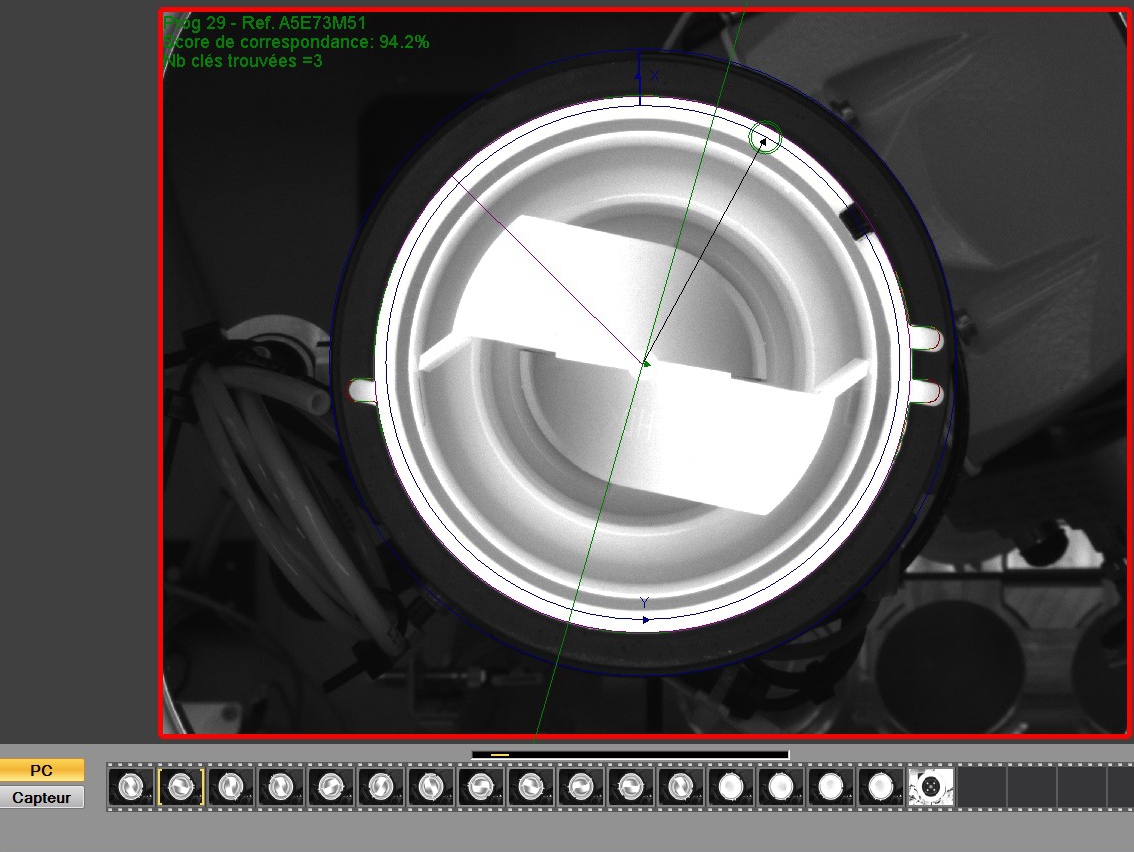
Development and implementation of automation technology
- Conveyors, custom-designed for the needs of the application to ensure the movement of products from station to station and the supply of components.
- Dimensioning, integration and programming of servo motors and brushless motors for the control of movements in torque or position.
- Implementation of measurement and monitoring solutions for weighing products
- Tracking and traceability of products in circulation via RFID
- State-of-the-art automation for the synchronization of operations, optimization of cycle times, production monitoring, communication with robots, cameras and distribution machines.
- Selection and use of numerous actuators and sensors
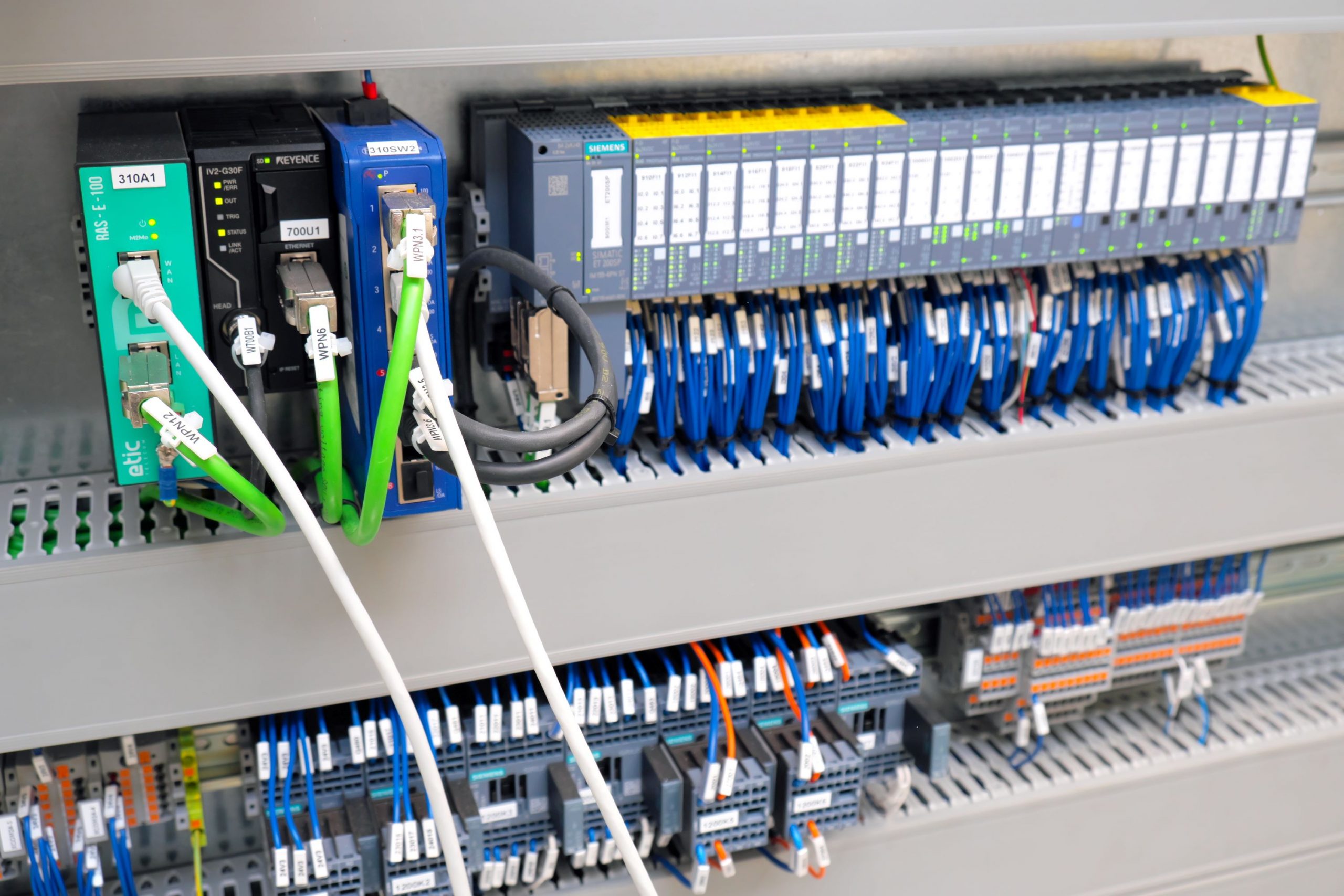
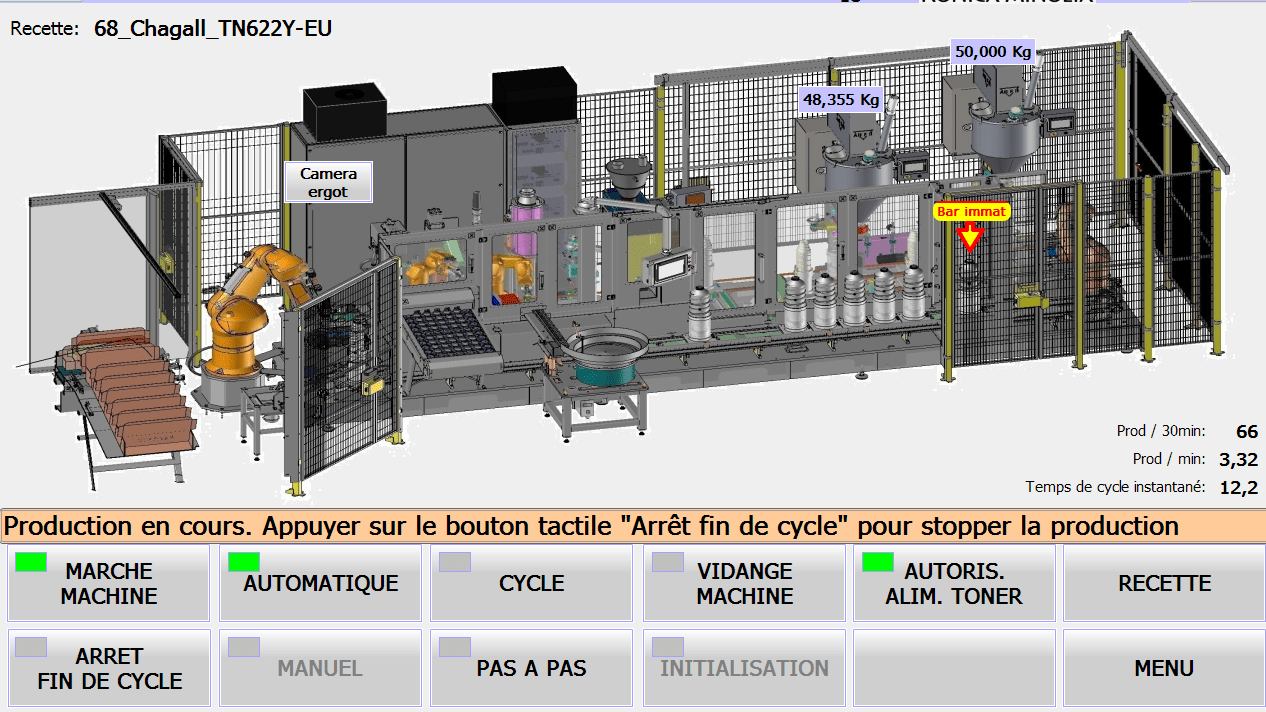
Detailed HMI
We take particular care to develop neat and sophisticated HMI interfaces so that the use of the machine is as clear and intuitive as possible. This allows our customers to easily operate and maintain the machines we supply.
The HMI of this production line allows to control the equipment in its different operating modes pleasantly. It includes all the production parameters in the form of configurable recipes. It also displays detailed information and messages on the operating status of the line and its connected equipment. These well-developed interfaces are very useful for the different users or maintenance personnel who quickly become autonomous.