Mechanized assembly station
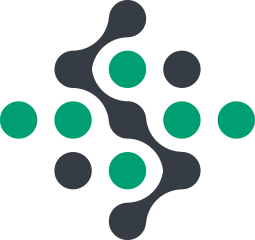
Optimizing the ergonomics of an industrial workstation
- Do you want to improve the comfort and ergonomics of your employees’ workstations in your production workshop?
- Do you want to improve the precision or repeatability of manual operations?
- Do you want to increase your production capacity?
- Do you want to reduce the risk of injury or MSDs in repetitive operations involving significant manual effort or uncomfortable postures?
Do not hesitate to let us know your specific needs and call on our know-how and imagination to study with you the best solutions, ergonomic and adapted to your conditions and your products.

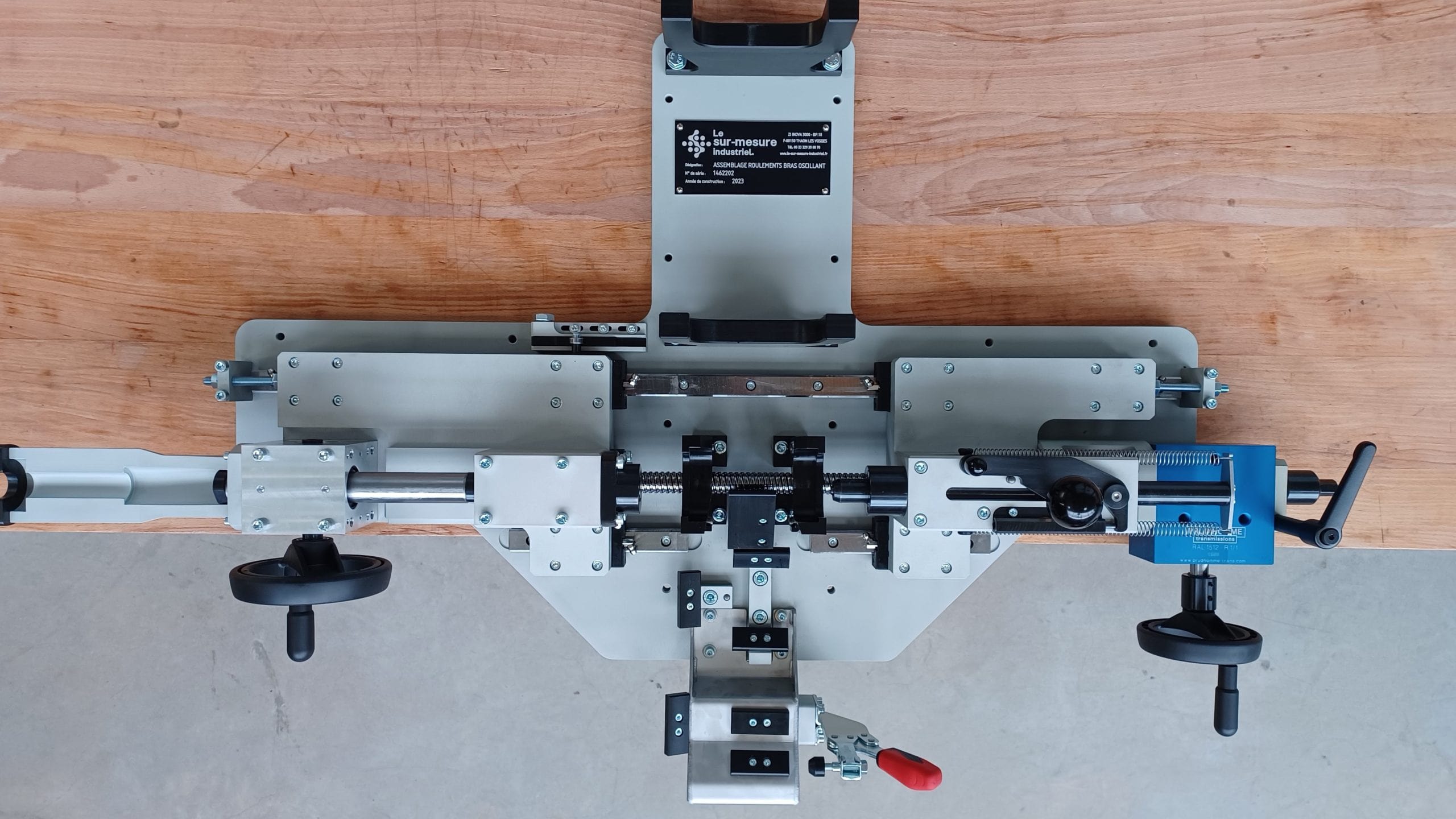
Creation of a new ergonomic workstation
Here is a good example of the study and production of a mechanized assembly equipment: This is a mechanized station for the fitting of bearings. This particular example of an industrial station concerns the installation of a hinge pin and spacers as well as the fitting of the bearings in their housing with a tight fit. The operations are entirely feasible without special tools, but greatly facilitated, optimized and made more reliable with custom-made assistance equipment, while minimizing the effort provided by the person for pressing the bearings.
The equipment makes it possible to position the various components in a stable, reliable, ergonomic and repeatable manner, in order to carry out the assembly operations. The movements are precisely guided, the actions requiring significant effort are multiplied by the mechanization and the judicious choice of transmission.
The result is a set developed to measure in close collaboration with our client, 100% adapted to their needs and their products. Delivered turnkey, to be positioned on an equipped workstation, existing in the workshop, the equipment helps the operator and facilitates assembly operations.
The component positioning elements are placed at an ergonomic height and take into account manufacturing tolerances. They offer small compliance movements in order to always adapt to the products. Clamping elements are used to immobilize the components during certain operations, particularly for screwing. The ergonomic layout of the components is designed to allow free and practical access to the different areas of the products for assembly.
The efforts made by the operator are optimized, respecting the values recommended by ergonomics specialists, eliminating the risks of MSDs and making assembly operations more pleasant and comfortable.
Markers and position indicators indicate in a simple and visual way that the components are correctly positioned, ensuring quality control during the operation.
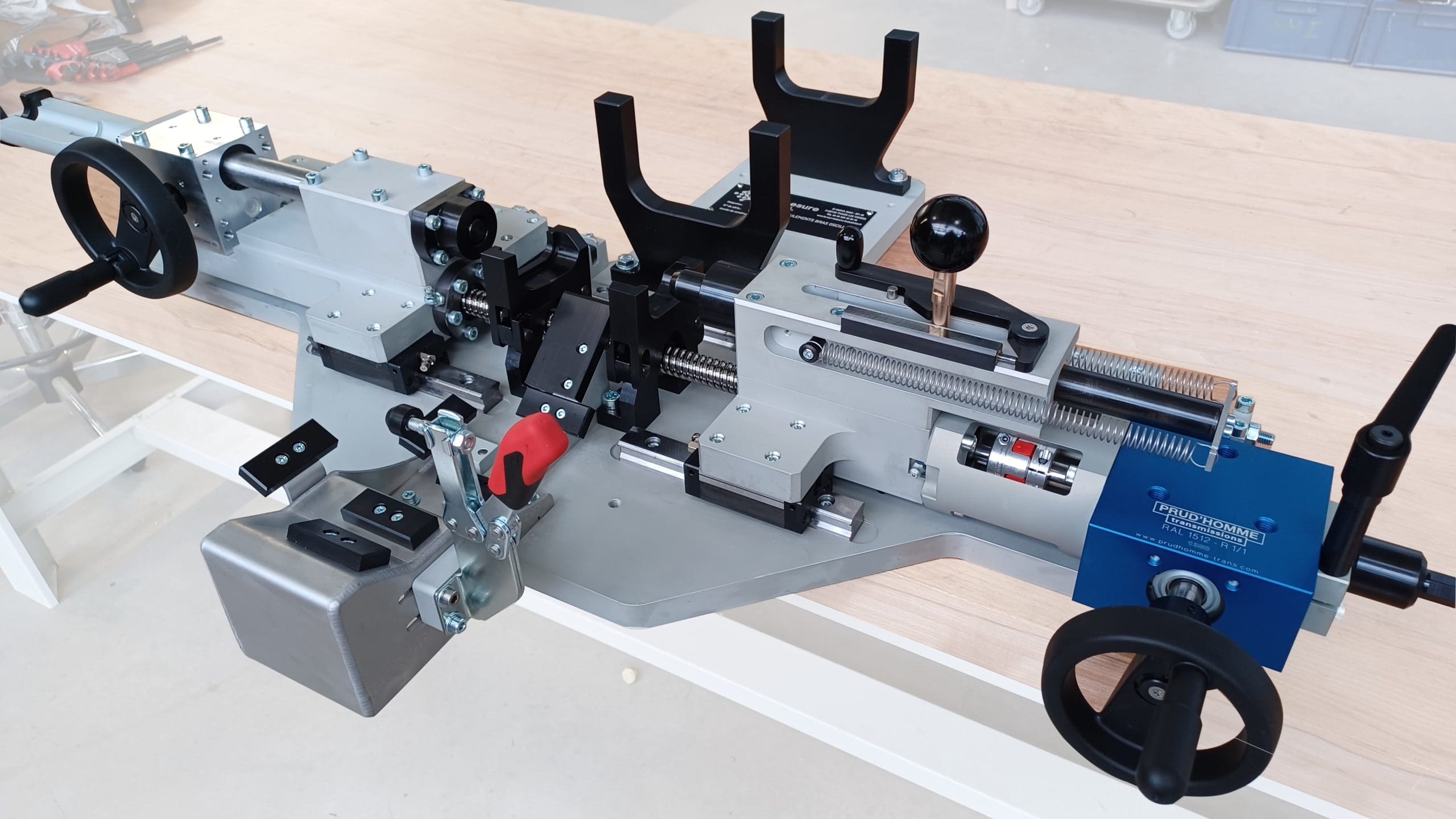
Safety of industrial equipment
We also pay very particular attention to the safety of the equipment user.
From the research of ideas, then throughout the study and design, we pay particular attention to preventing any injury by designing anti-pinch, anti-crushing systems, by minimizing the manual efforts required and by integrating warning and prevention signs if necessary.
Our requirement for safety is also evident during the production and manufacturing stages. The parts are systematically deburred, the protruding edges are chamfered, the corners are rounded, etc.
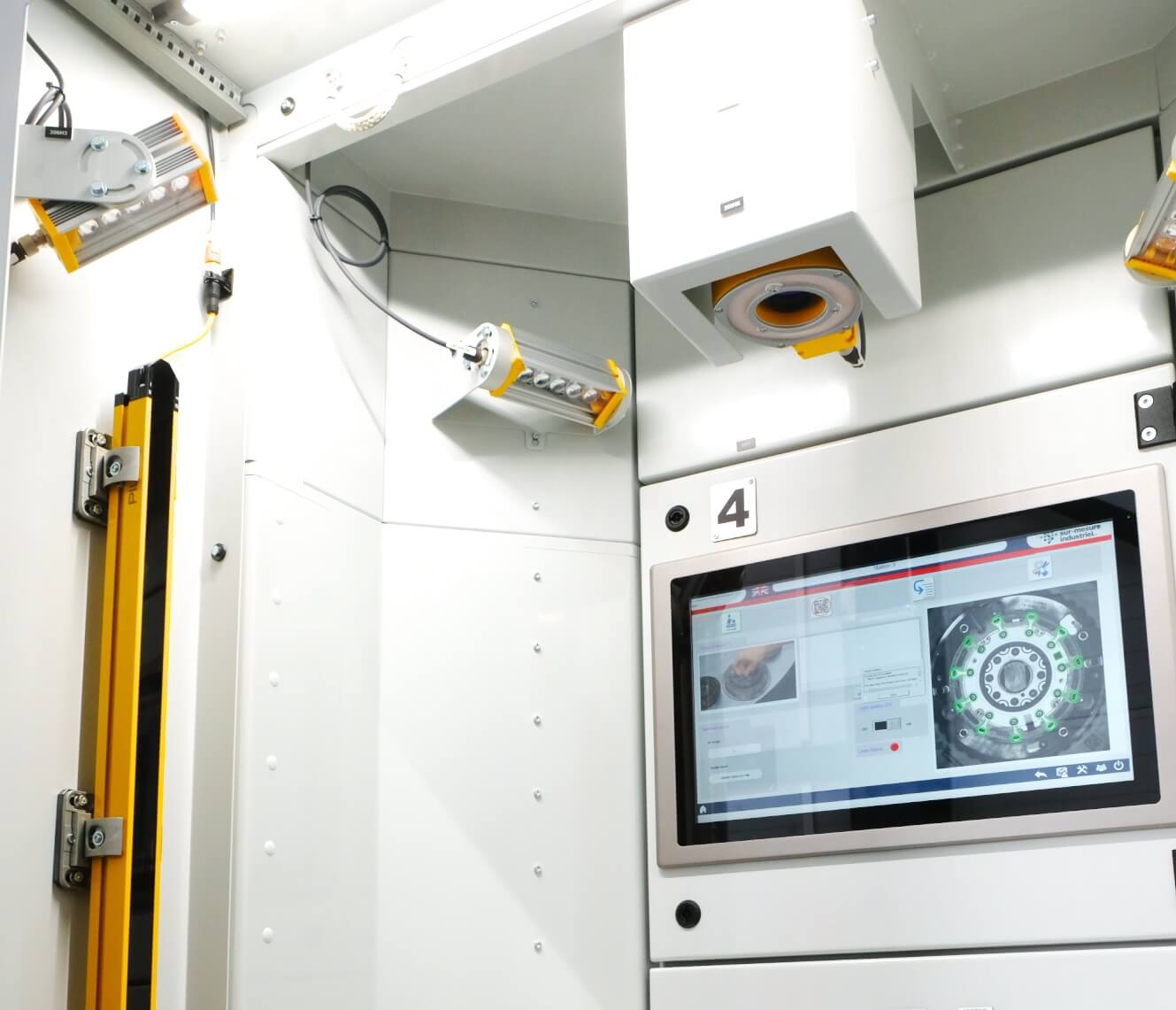
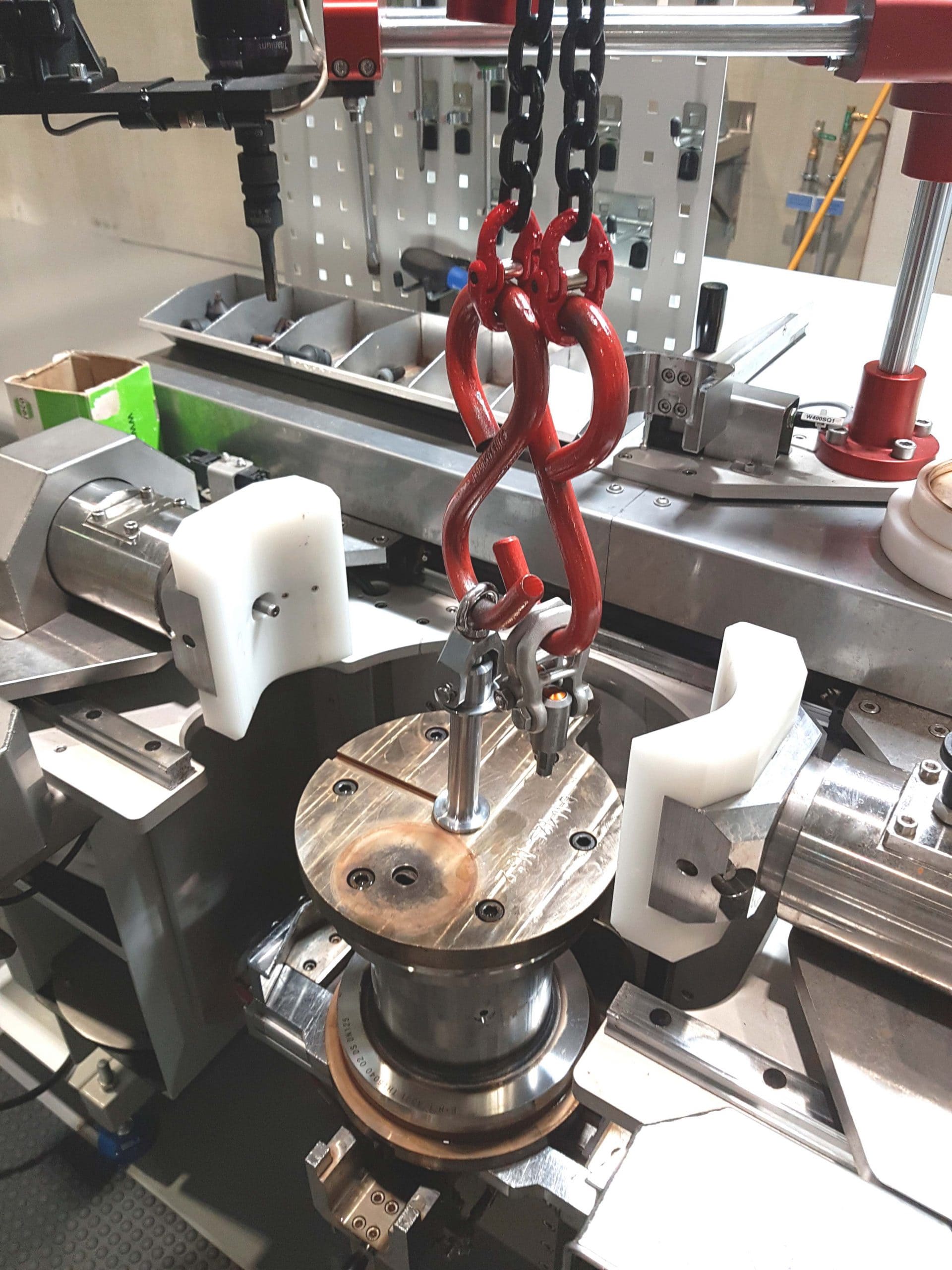
Ergonomics to improve working conditions
Within your company, some tasks can be difficult and unpleasant, repetitive or even dangerous. Le Sur-mesure Industriel is at your service for the creation of tools, the study of alternatives or more ergonomic improvements adapted to your production, your workshop and its environment, in order to reduce risks.
Generally speaking, many assembly, transformation, handling, etc. operations can be assisted or automated, entirely or partially in order to improve the ergonomics, comfort and safety of workers. The operations may or may not use additional electrical or pneumatic energy depending on the need of the application.
In any industrial field, other examples of function automation, workstation optimization, operator assistance, product handling tools and other ergonomic equipment can be found in our pages “Assembly“, “Consulting / Continuous Improvement“, “Robotics” for example.
This is the case for example with the study and production of this semi-automated station for the assembly and disassembly of injection molds.
The creation of this equipment made it possible to eliminate the need to carry heavy loads: lifting accessories, gripping of parts in a vice, rotating jaws for turning. The equipment also has a height-adjustable work surface and motorized movements for operations that require repeated and excessive effort. The integration of a screwdriver, a screen that guides the operator and adequate lighting makes the equipment pleasant and ergonomic to use.
All operations and manipulations were previously done entirely by hand. This development has therefore greatly improved ergonomics!
We have also already created other workstations or applications using height-adjustable devices, weight compensators, infrared industrial vision lighting (invisible light that does not dazzle).
And this is just a small overview of the possibilities!
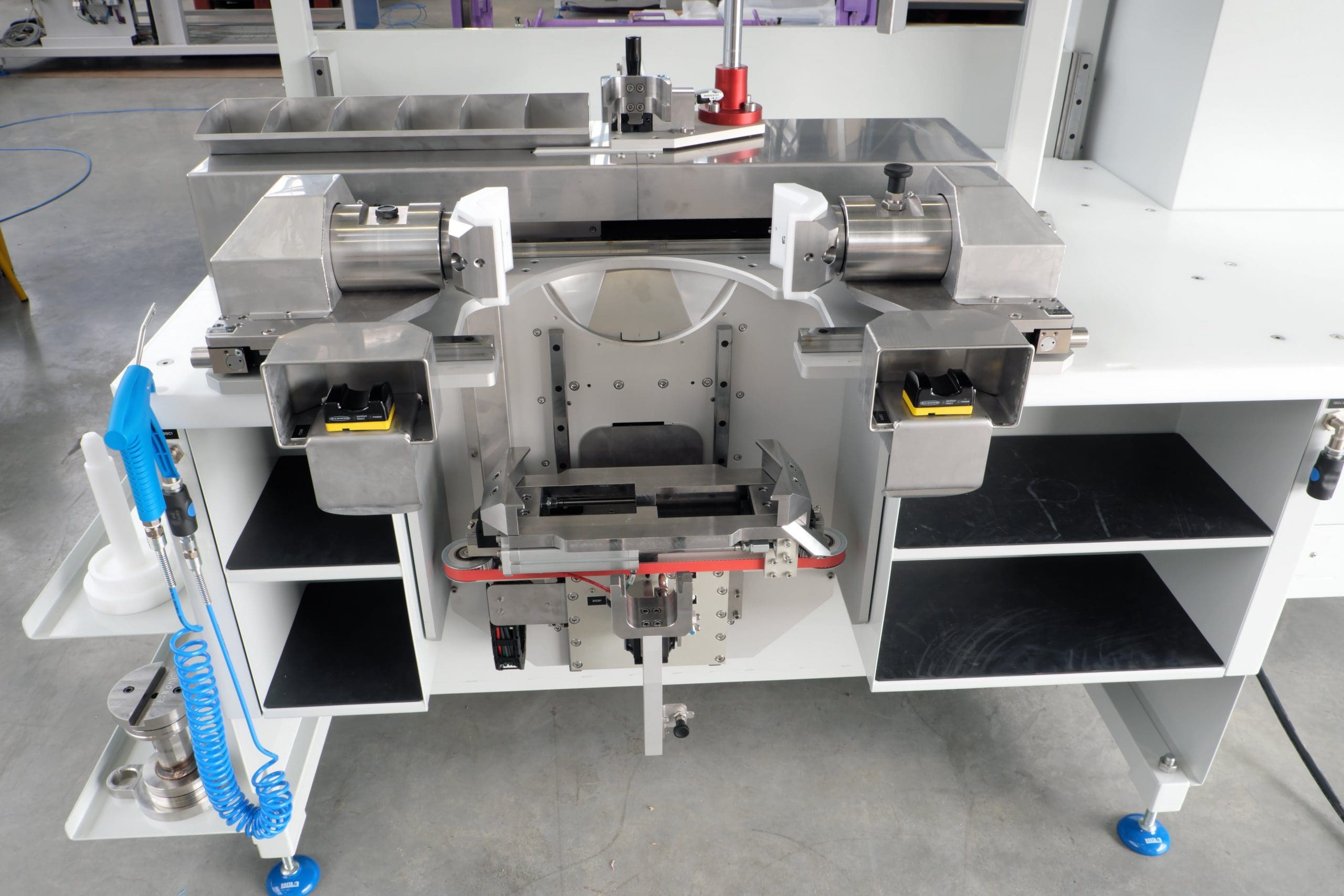