Percussion cable deicer
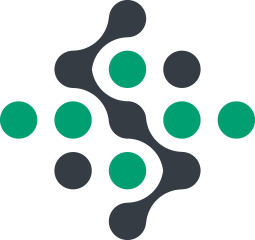
Custom-made autonomous and portable tools
Here’s a look back at this innovative prototyping project…
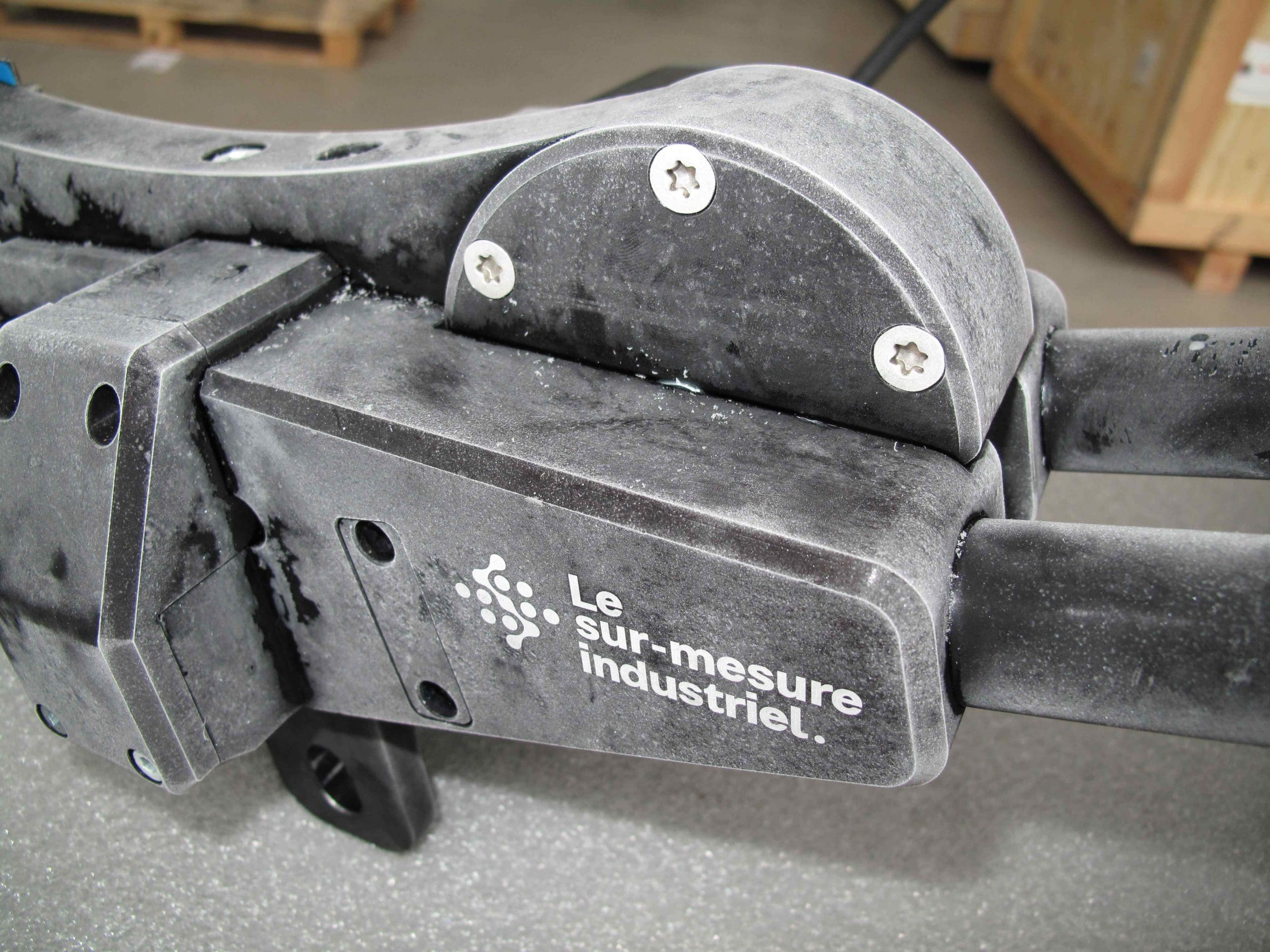
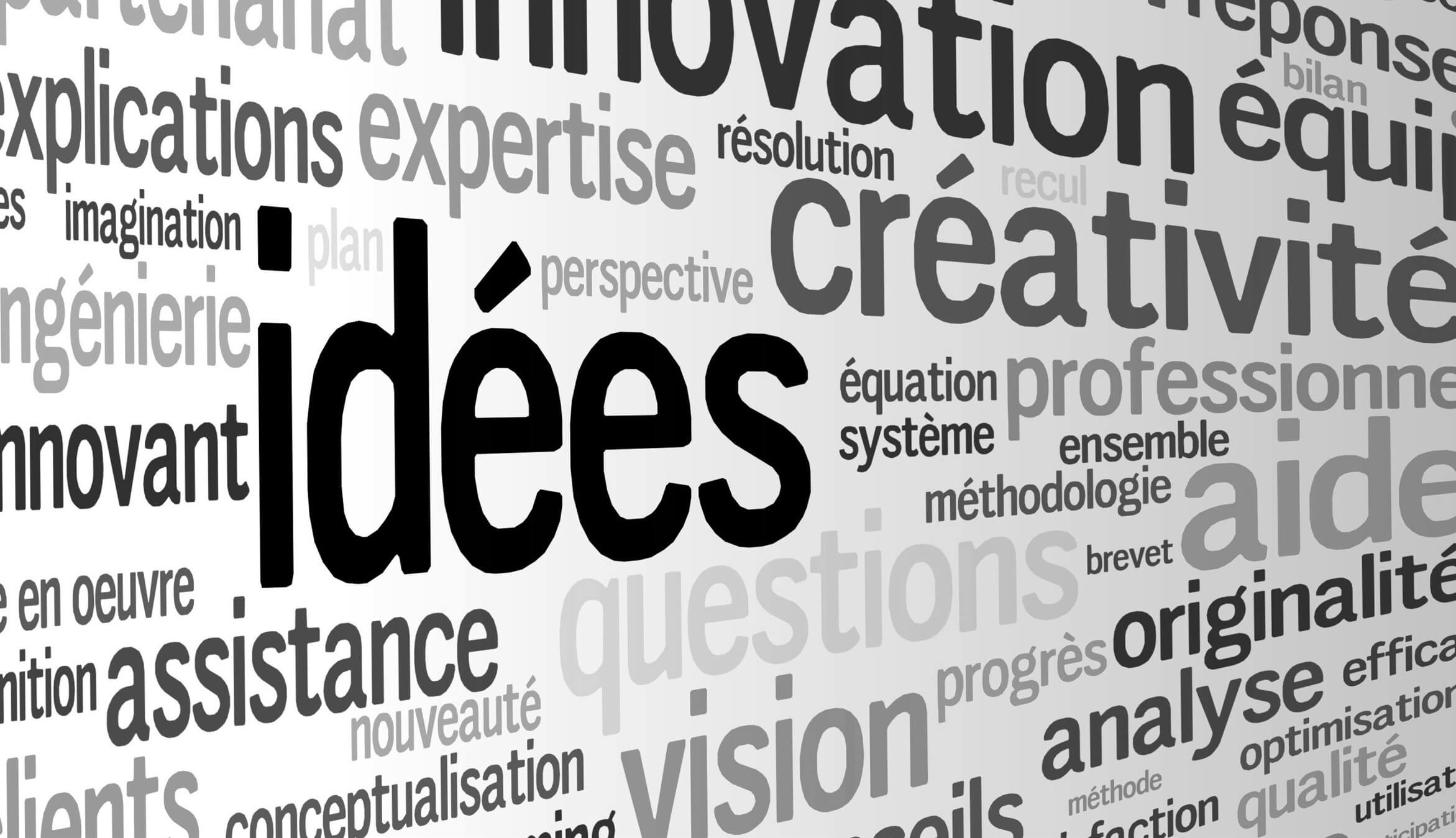
Search for principles
After comparing different techniques, the most suitable and promising one for testing was:
De-icing and breaking the ice through impacts and vibrations applied to it.
Monitoring technological developments
Through analysis of technical documentation, construction blueprints, exploded views, and the disassembly and measurement of a device to understand its functioning and design, we began the development of our percussion cable de-icer.
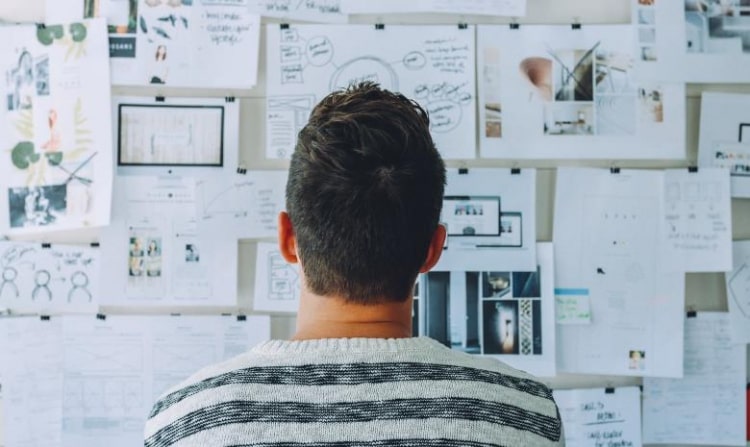
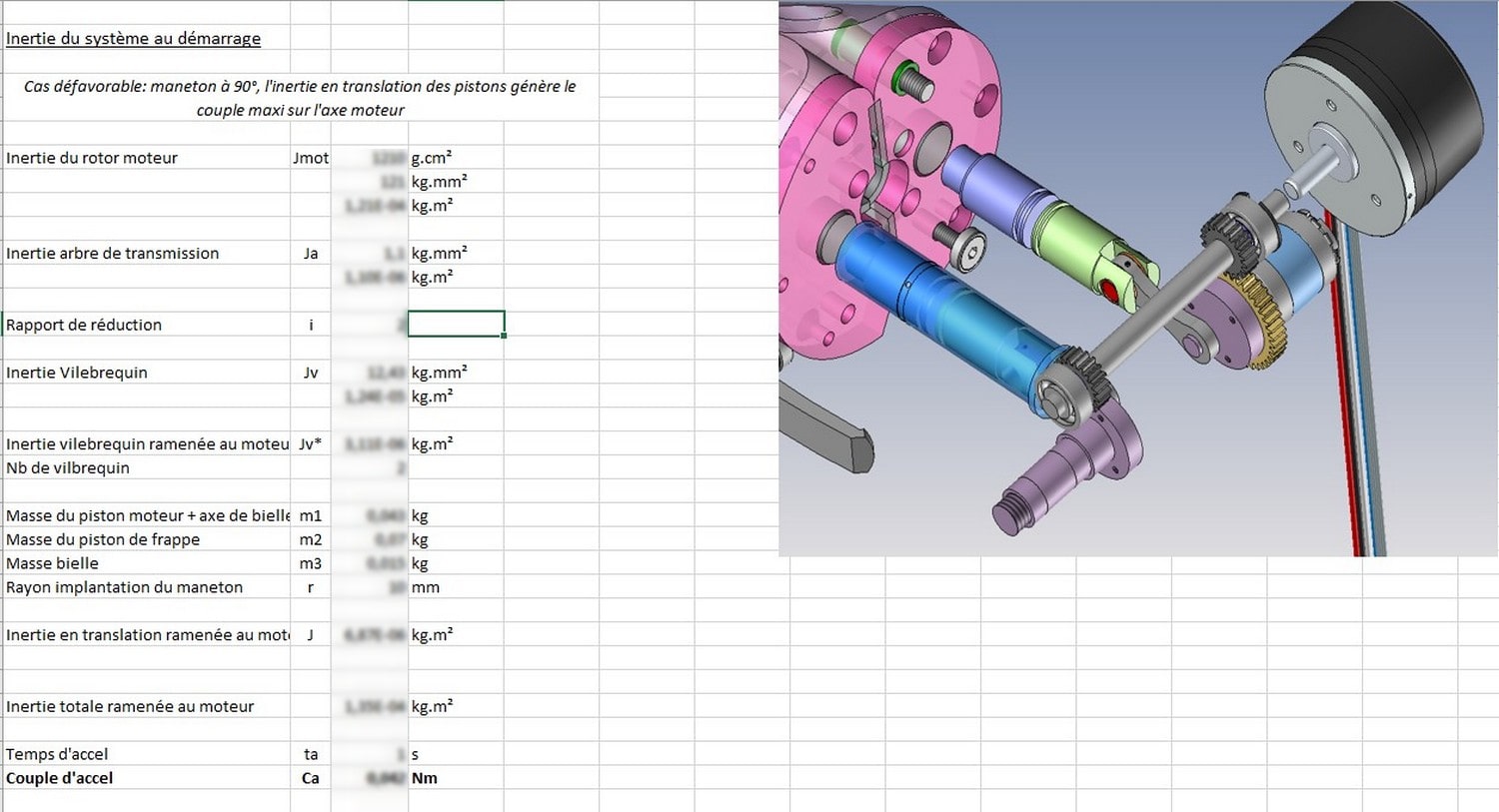
Calculations and sizing
We defined the motor’s operating speeds and torques, battery capacity, and the kinematics needed to meet the performance objectives we had set.
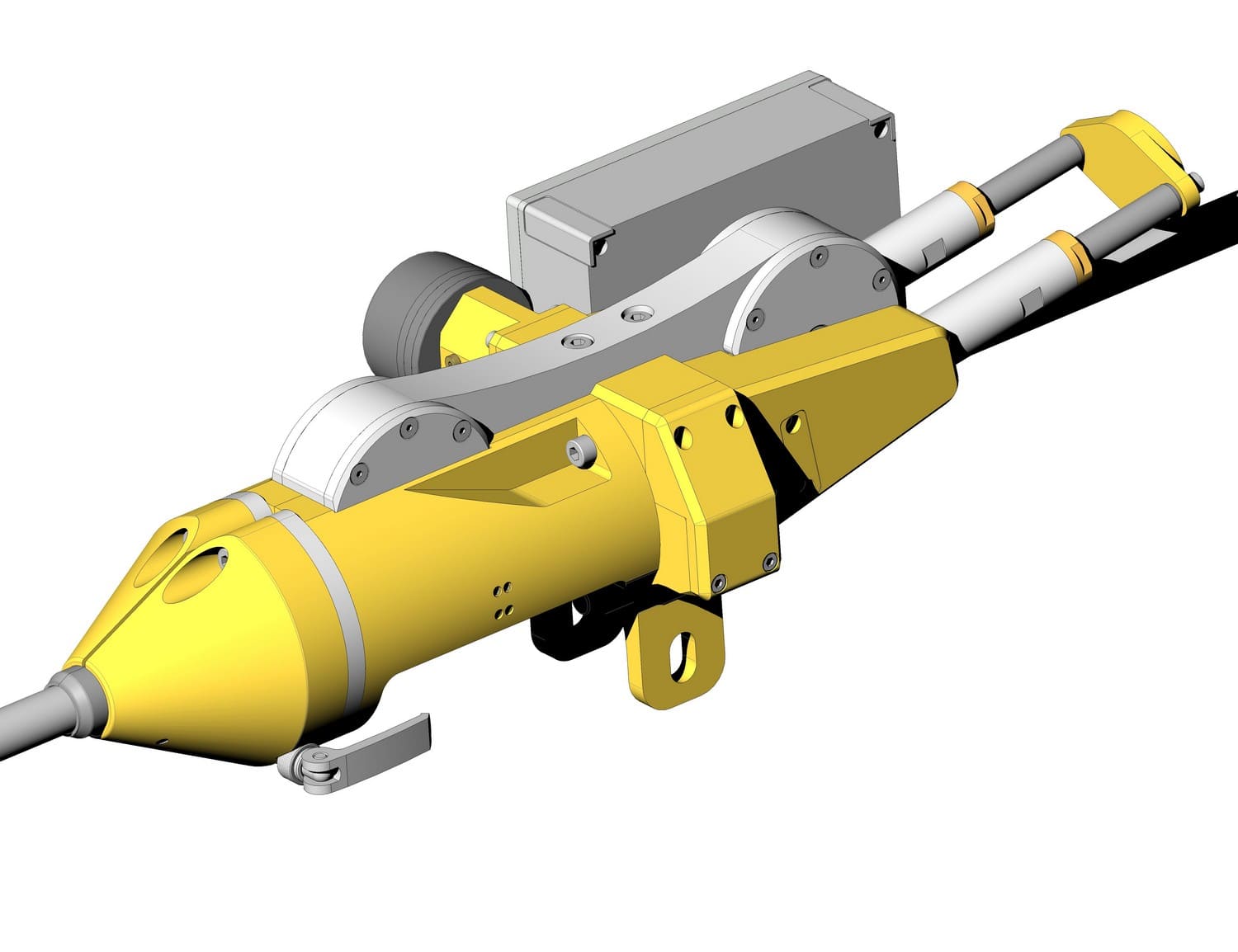
Mechanical and electrical design
The device is autonomous, powered by a rechargeable and easily swappable battery, ensuring operational flexibility.
Prototyping
Thanks to our local suppliers, stainless steel and aluminum parts were machined and treated based on our blueprints.
We supplied commercial components, then carried out the mechanical assembly and wiring in our own workshop.
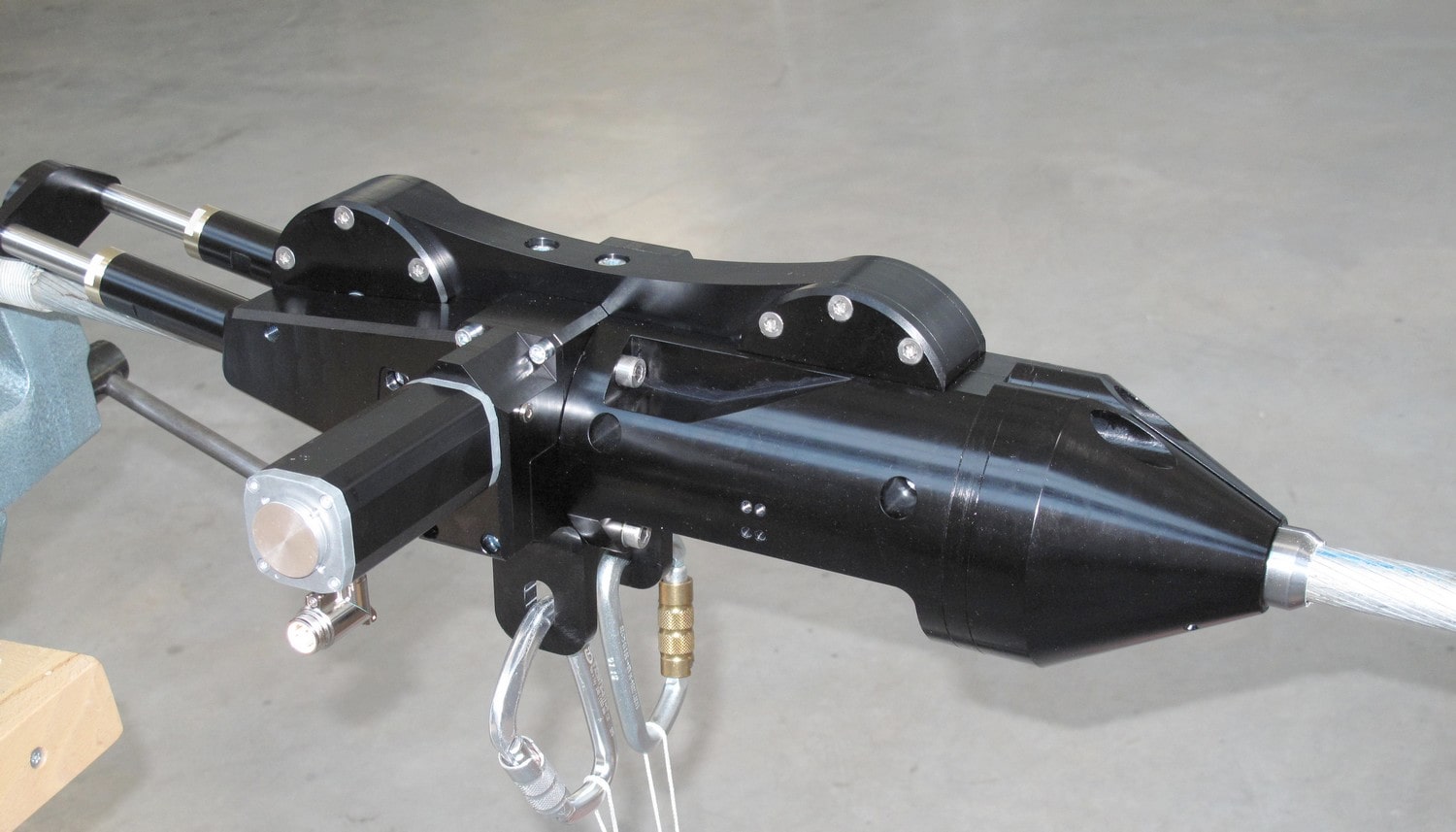
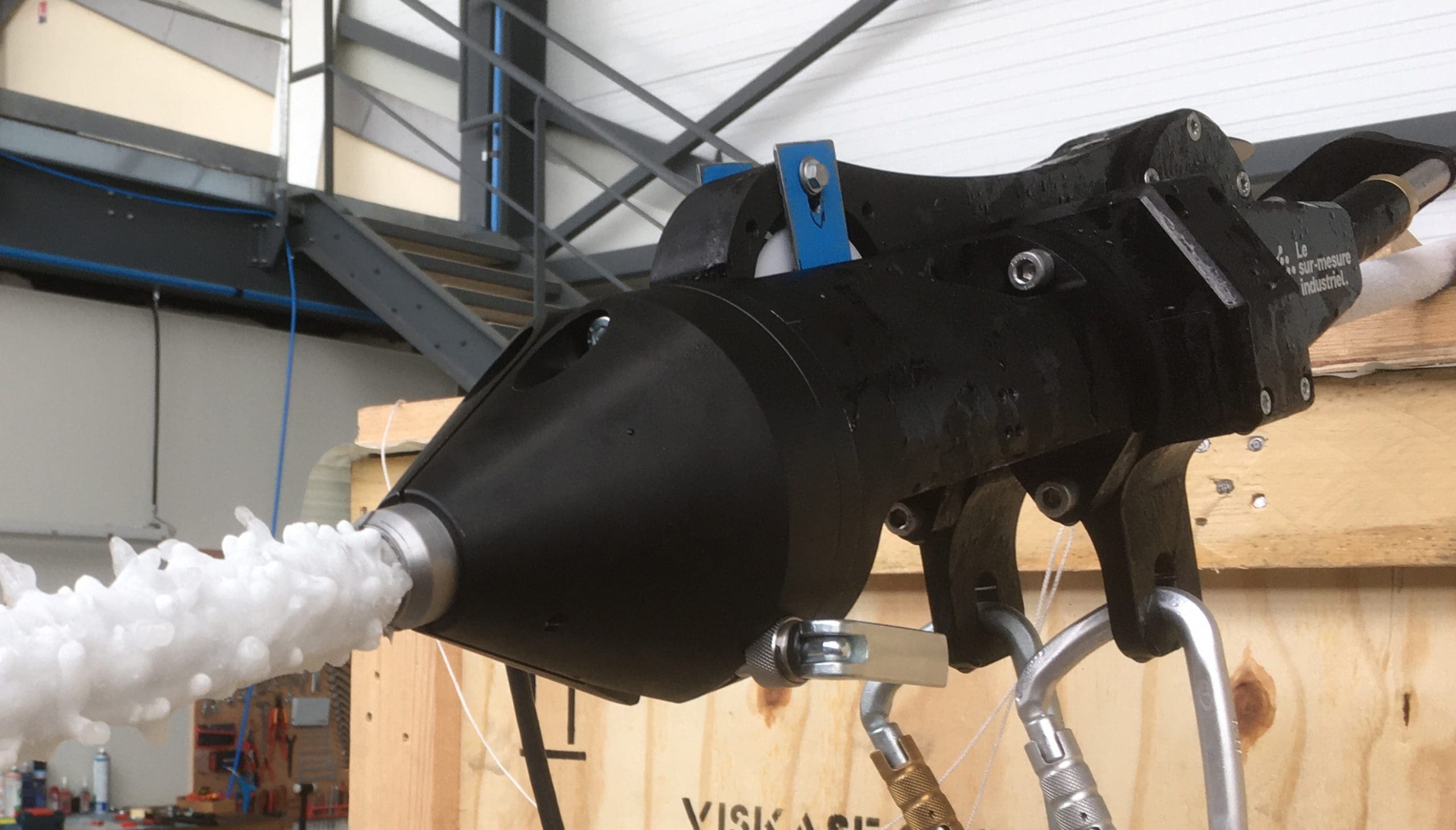
Functional testing
To simulate these conditions, we used a refrigerated truck set to around -30°C. This allowed us to verify that the de-icer’s functions remained operational even in such a frozen and humid environment.
We also created ice accumulation on a metal bar to simulate a cable section and analyze the percussion de-icer’s performance against ice. After a few adjustments, the system produced promising results!
Real-world testing
Result: The de-icer performed its job, successfully removing all ice and frost. The zip line could be immediately used afterward.
This trial also revealed areas for improvement to enhance the device’s performance and build quality.
Stay tuned for updates!
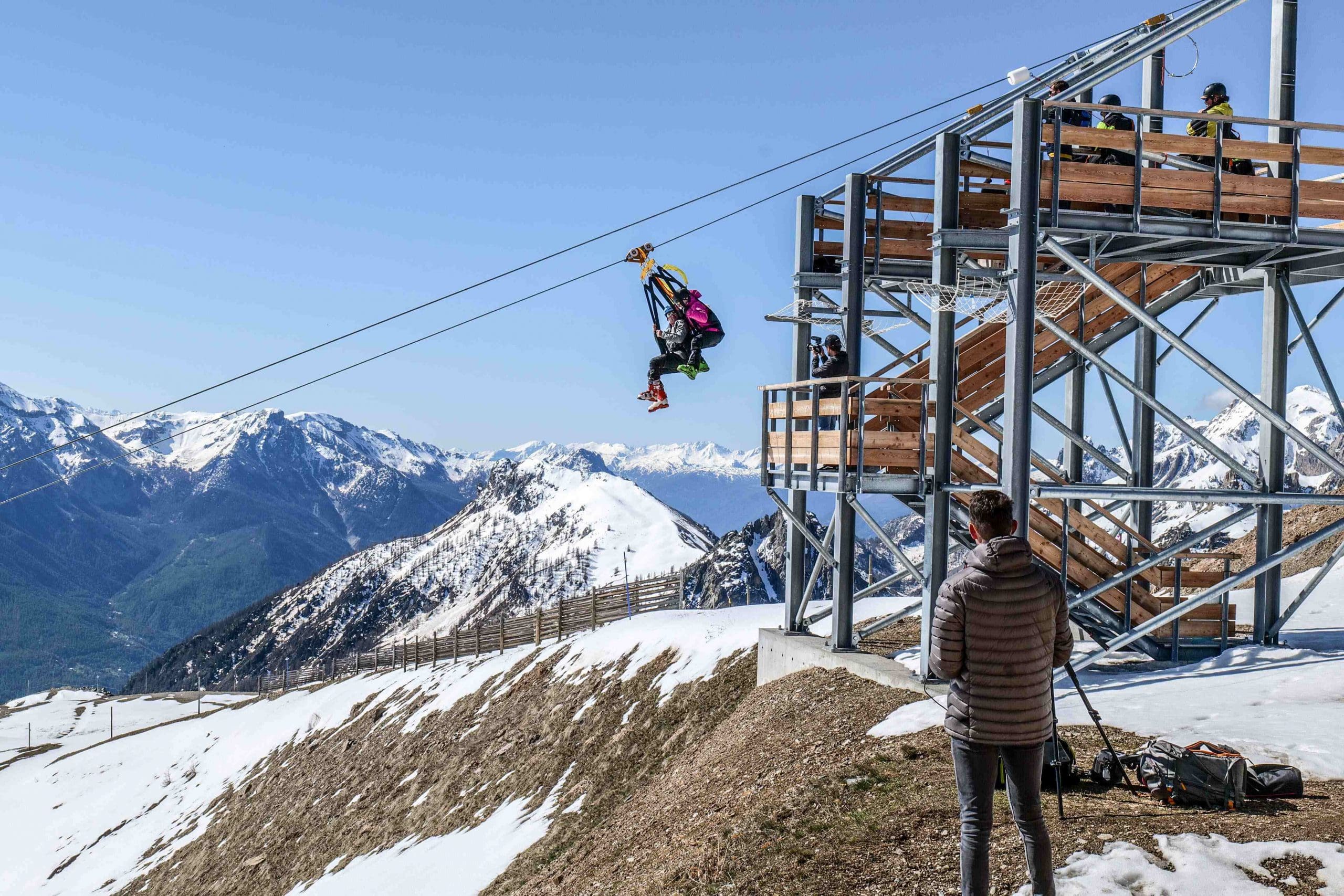