Consulting / Continuous Improvement
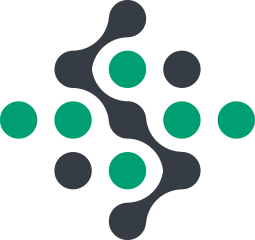
Purpose and Process of a Consulting Analysis
- Offer a neutral perspective on current production principles.
- Collaborate with internal or external continuous improvement teams.
- Gather objective and subjective data.
- Analyse the request within its context and propose recommendations.
- Formulate and test hypotheses against internal constraints.
- Identify relevant and innovative ideas.
- Test suggestions (through digital simulations, lab tests, prototypes, etc.).
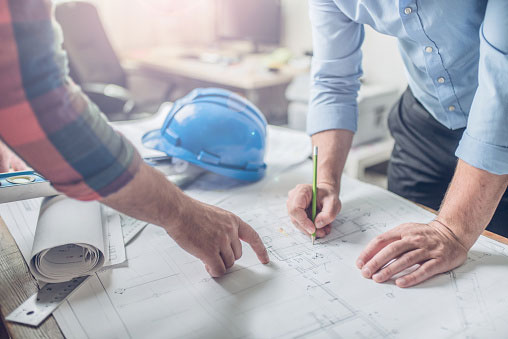
We provide our clients with an external perspective and expertise while ensuring confidentiality.

Within the scope of continuous improvement
We can intervene alongside or after analyses based on methodologies such as Lean Manufacturing, Six Sigma, Lean Sigma, or Kaizen, to complement the company’s continuous improvement efforts.
Specialized experts in these analyses organize working groups, formalized measurement and analysis tools, prioritize issues and actions, and verify the efficiency and coherence of implemented solutions
At our level, we collect information from management and production personnel to propose technical solutions.
Prioritization of functions to be automated in pharmaceutical equipment, based on different criteria:
- Workload difficulty
- Precision
- Control capabilities
- Automation cost
Improvement of continuous industrial processes in papermaking, food processing, steel tube production:
- Enhancing safety
- Implementing quality controls
- Integrating new technologies
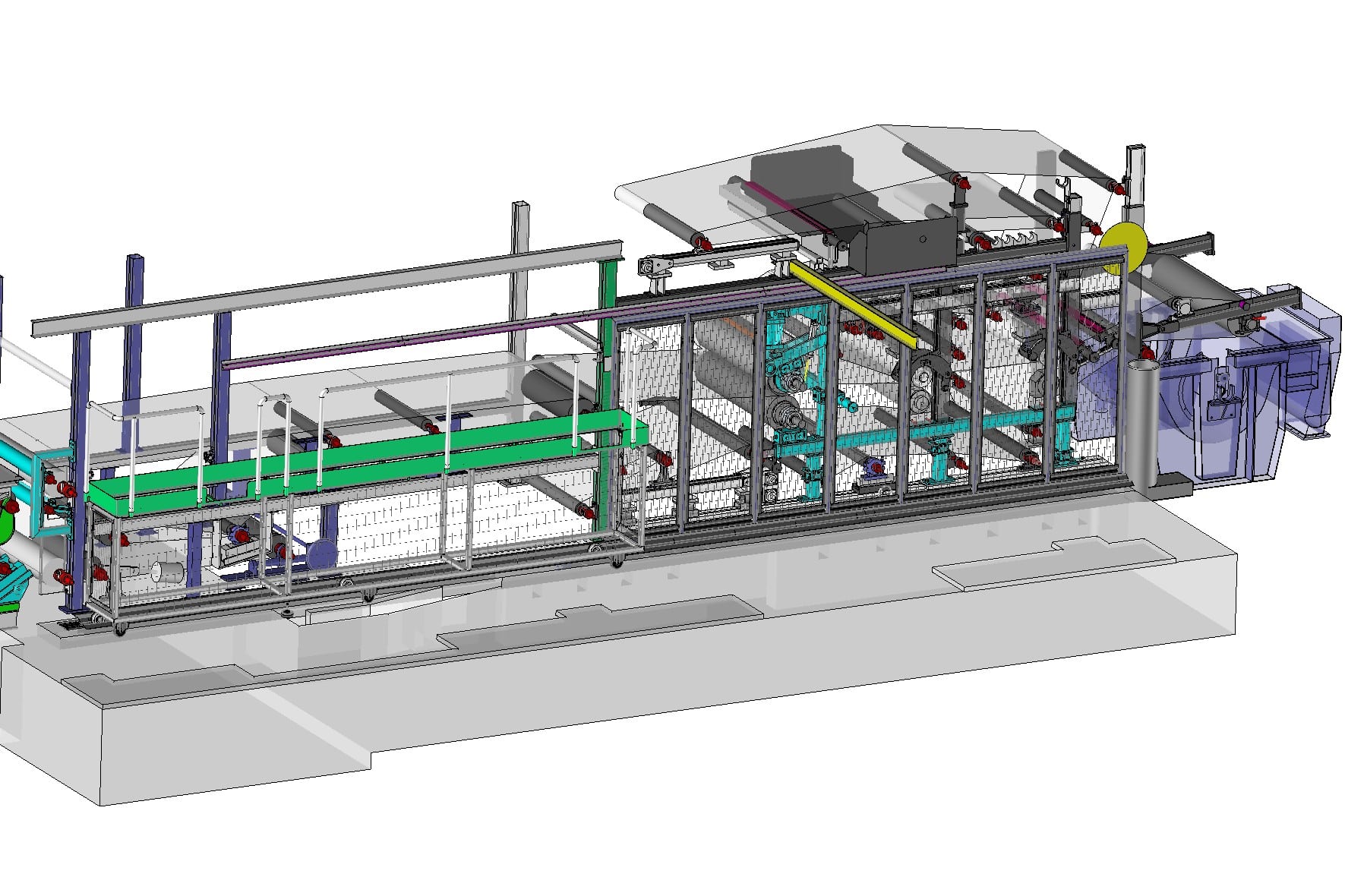
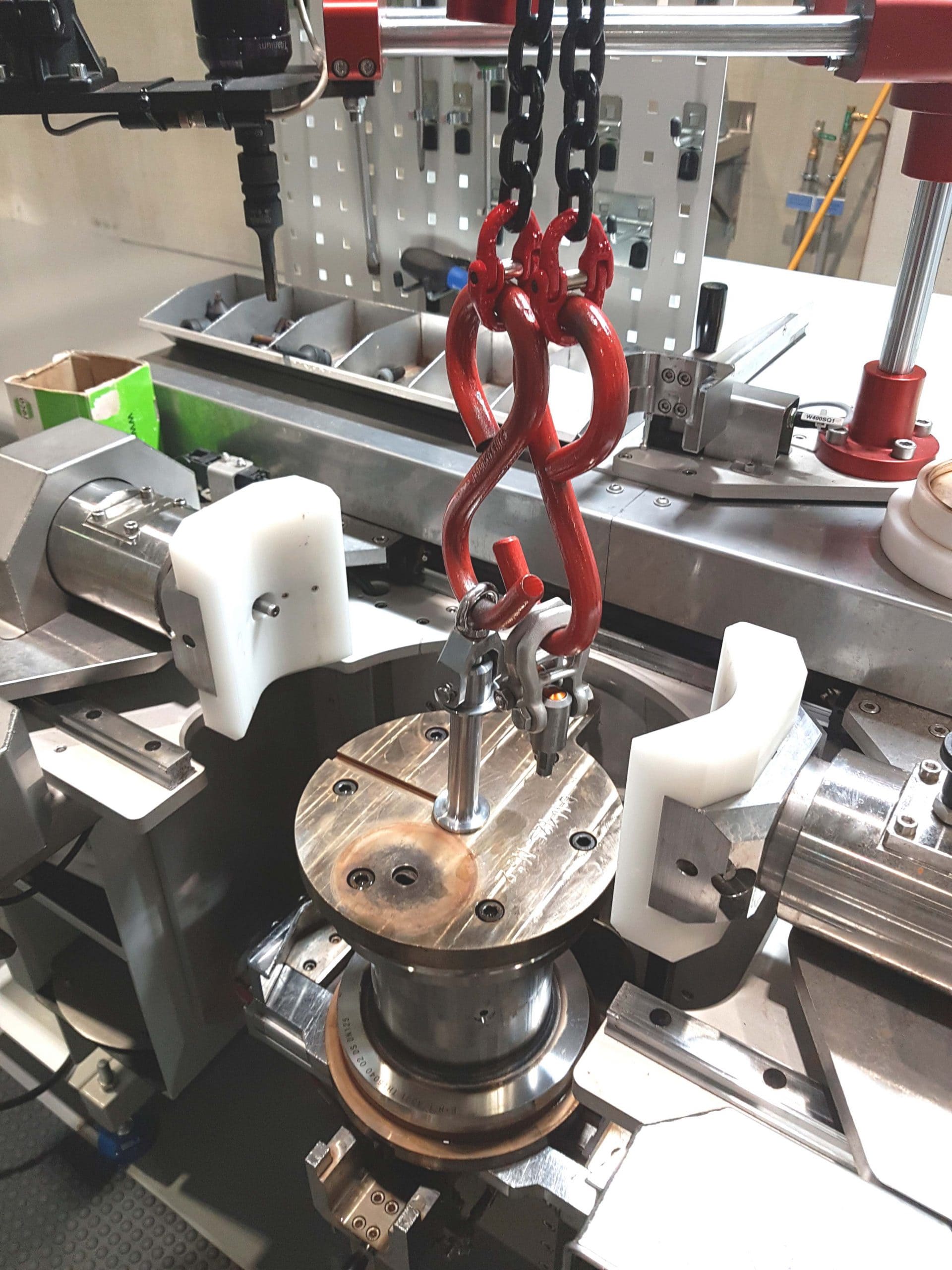
Example of actions:
- Advising and guiding clients toward specific suppliers or manufacturers
- Redesigning workstations
- Improving workstation ergonomics
- Balancing workload distribution
- Simplifying operators’ tasks
- Integrating advanced technologies
- Designing innovative solutions and equipment