Calculations / Simulation
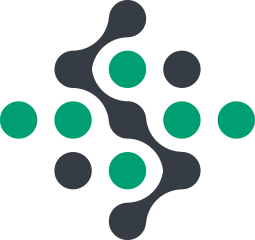
Le Sur-Mesure Industriel manages the modelling and digital simulation of your system
Do you need to rely on a competent company to carry out your modeling and simulations? You can count on us. Our team, made up of technicians and engineers, is at the service of any company looking for calculation services, problem analysis, and system sizing.
Are you facing operational hazards on equipment? We can bring a fresh perspective to your issues, collect data, analyse it by calculations, and offer you solutions for improvement and innovation.
Do you want to study the feasibility of an idea, a concept or even create new equipment? Sur-Mesure Industriel manages the sizing and modelling of your system.
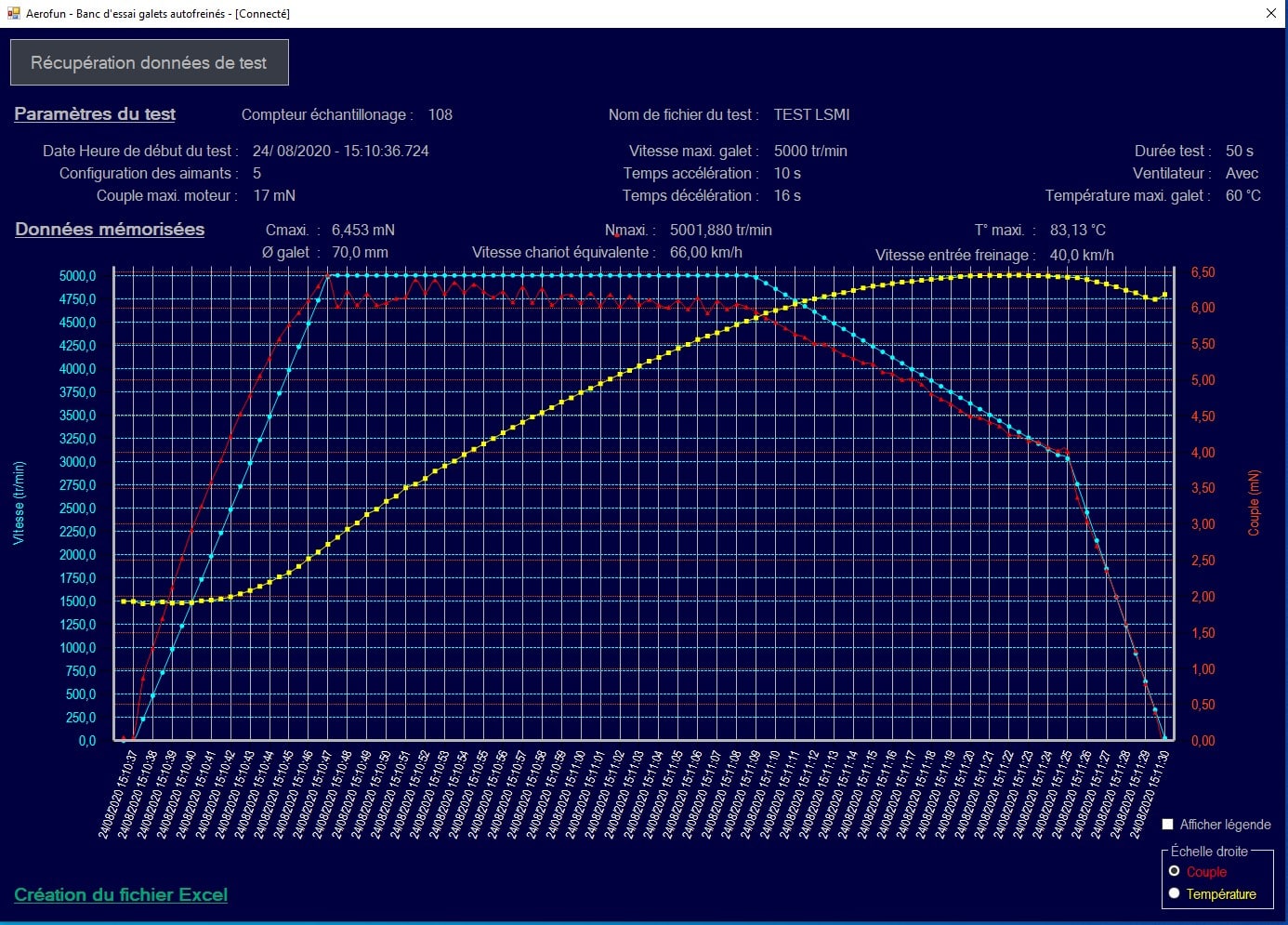
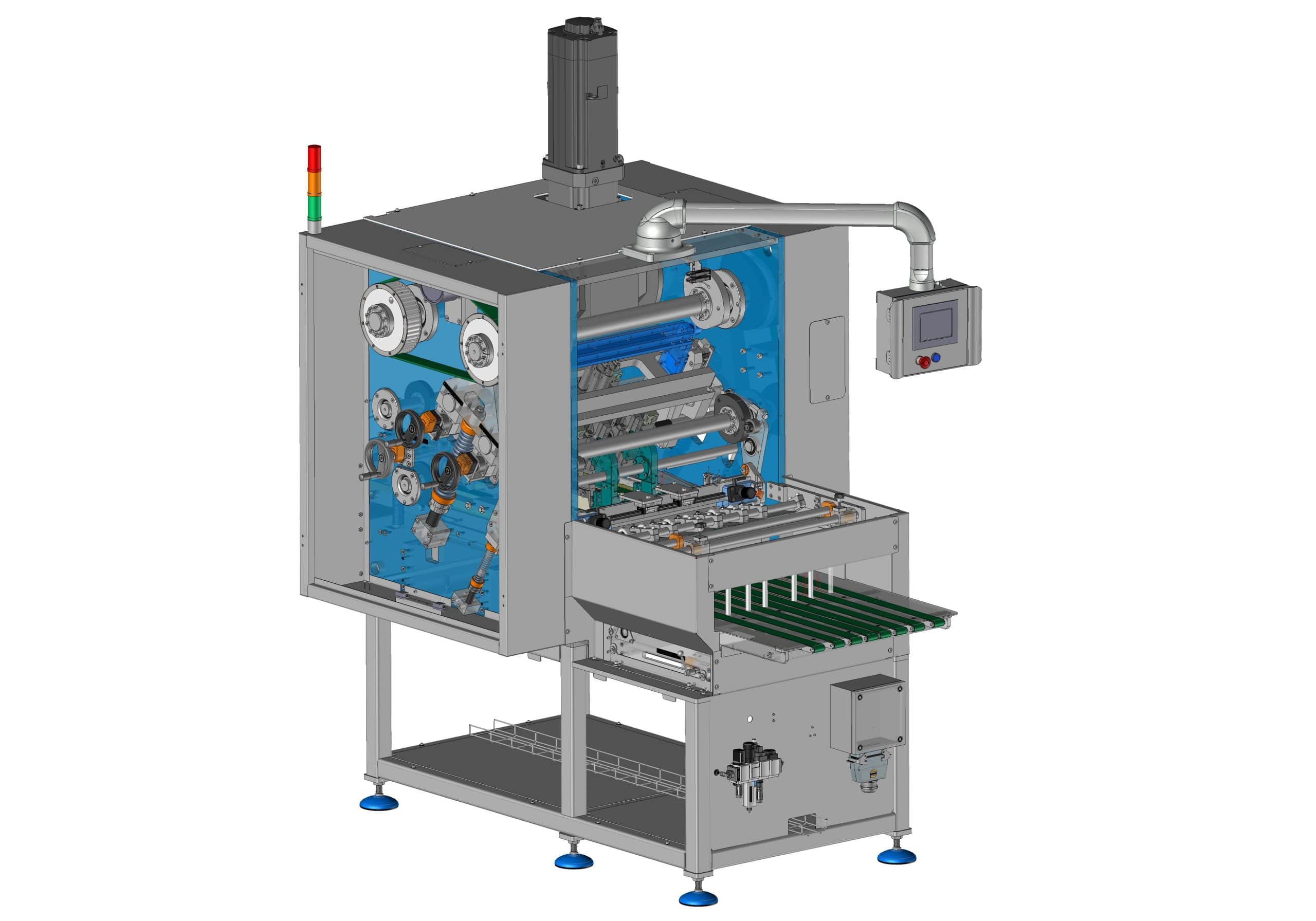
Mechanism modelling, kinematic and dynamic simulation
Using our CAD design software, we model complex systems and simulate their operation. Assemblies are created with their degrees of freedom, thus making it possible to animate the movements of the different components of a piece of equipment.
Thus, complete kinematics of machines or industrial processes can be created digitally in order to verify sequences for example, or obtain calculated values for forces, torques, speeds, accelerations.
This data is then used for the determination and sizing of components. It also makes it possible to offer a very explicit animated visual for communications with customers.
Material resistance
Software and IT also allow us to digitally verify the mechanical strength of certain parts subjected to significant stresses using finite element calculation modules, FEM. By having precisely entered the physical and mechanical characteristics and properties of the material considered in the dedicated technical software, we can simulate different load cases: force, pressure, imposed displacement.
We also know how to appropriately define the mesh, blockages, supports, and reactions in order to obtain a representative, coherent and viable simulation. These simulations are based on a mesh of the parts and indicate in the form of results, the deformations, deflections and mechanical constraints obtained within the part studied.
These techniques are very useful for validating the geometries and materials of the designed parts, or seeking to optimize the mass/resistance ratio for example.
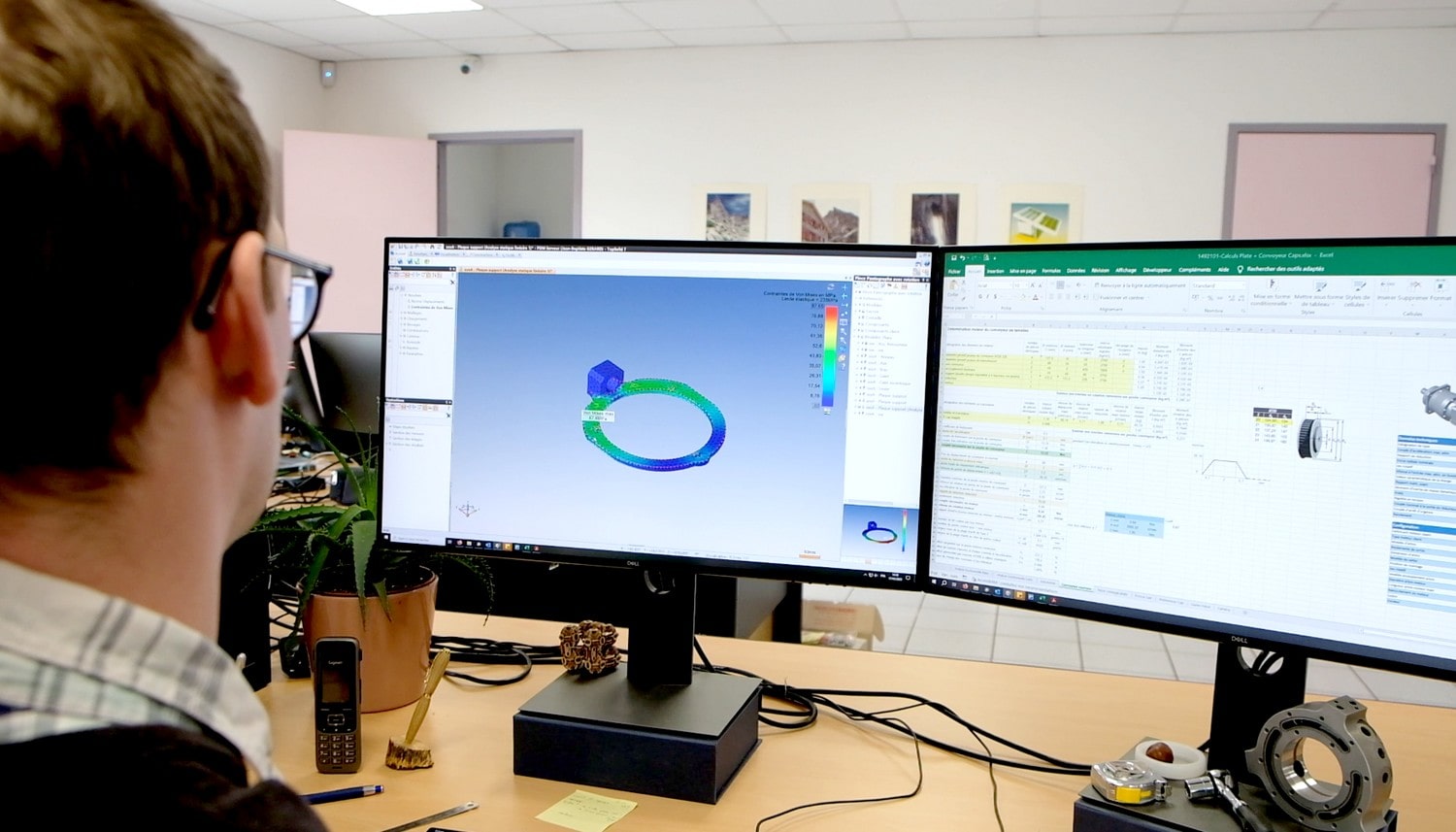
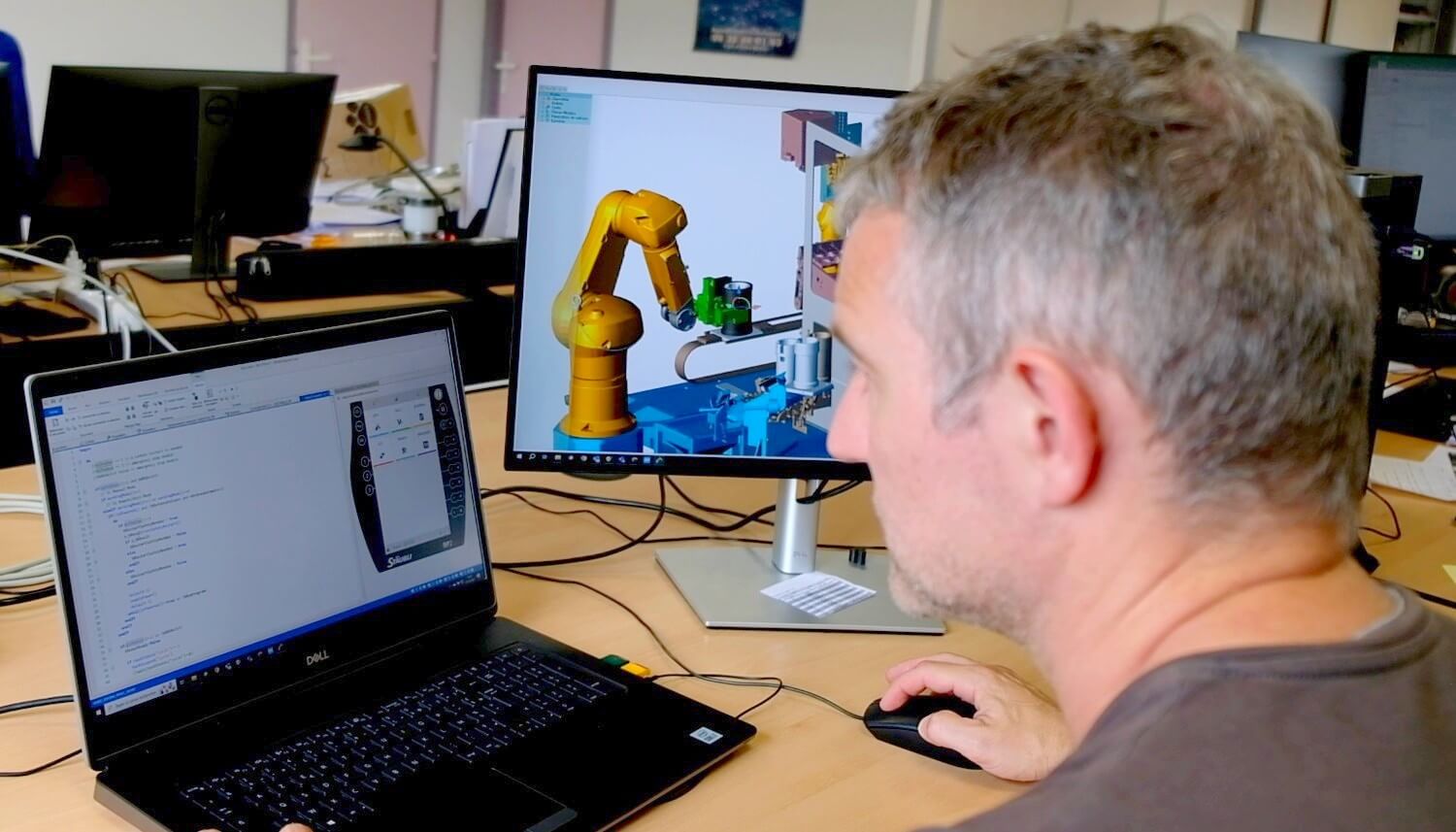
Robotic simulation
Our software dedicated to robotic programming for industry allows us to simulate the operating cycles of one or more industrial robots in their 3D environment. This allows us, in the pre-project phase, to carry out simulations of robot trajectories and movements in order to study the feasibility of a project, estimate cycle times and pre-size industrial robots.
These software simulation tools then allow, when the project is more advanced, to test the progress and execution of the complete robot program, taking into account the detailed 3D environment and digital exchanges with the PLC. These steps aim to anticipate the commissioning phases, to verify and optimize the operation of the complete robotic system.
Advantages of calculations and simulations on digital models
Obtaining data and information through modeling, simulation or calculation allows us to reduce development costs, thanks to the anticipation or prediction of phenomena that would be observed on real equipment.
Simulation reduces the time associated with prototyping and testing, and helps speed up the development of a product or equipment by working on virtual models. It also allows the behavior of a part or system to be studied via a purely digital model to validate a technological choice, or with the aim of optimizing it and making it more efficient.
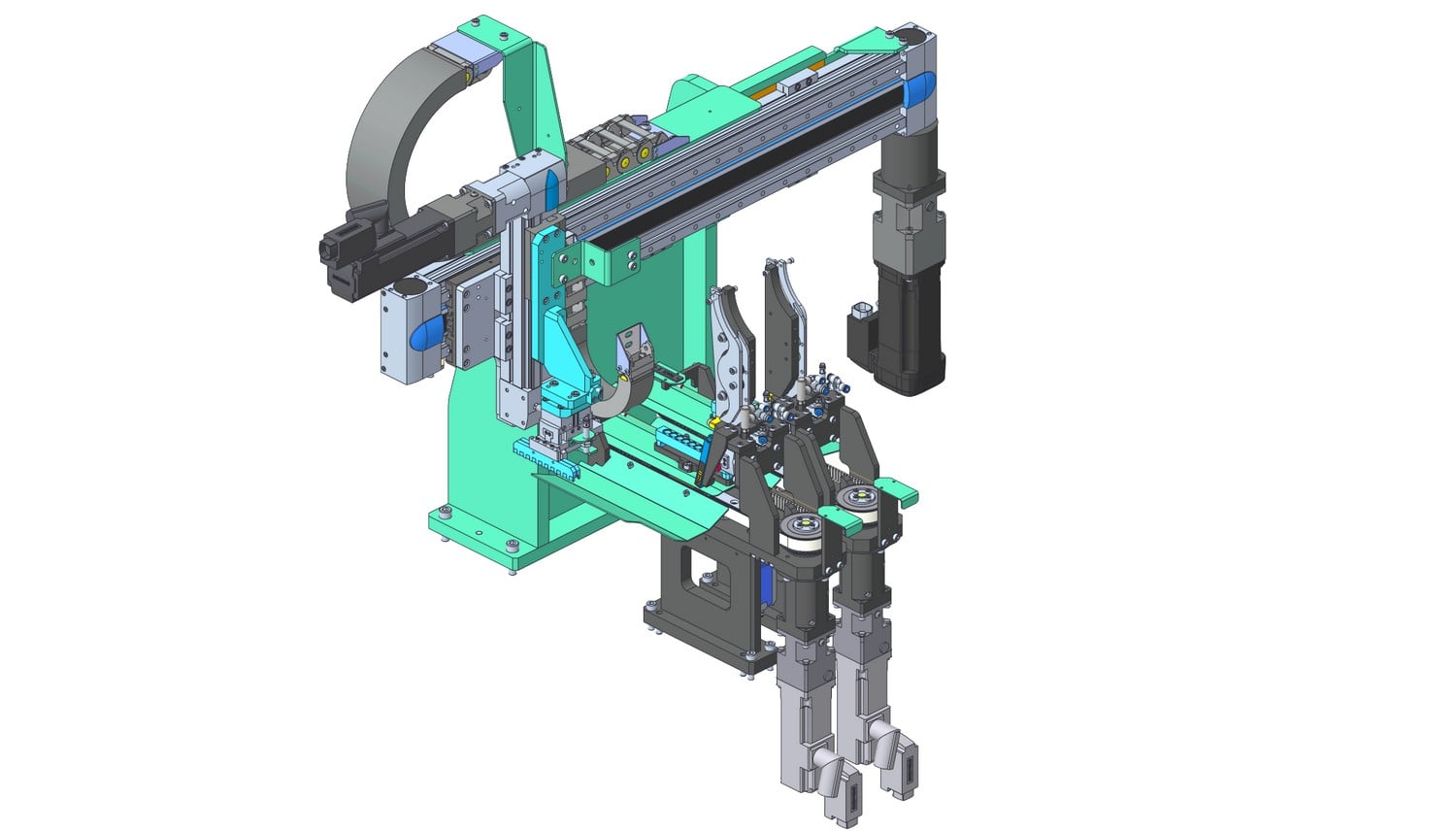
Calculation and simulation for the development of innovative equipment or processes
In our engineering profession, calculations are often present from the beginning of projects. Indeed, during feasibility, numerical approaches in different fields make it possible to give the orders of magnitude of dimensioning, rates, ranges of use, etc.
Calculations make it possible to quantify numerous physical data on the system studied, to understand the phenomena which govern its operation, and to determine the limits of use.
Calculations allow us to quantify numerous physical data on the system studied. By more or less complex modelling, we can deal with different scenarios, different load cases, different stages of operation in order to guide or validate technological choices for the design of a product or equipment.
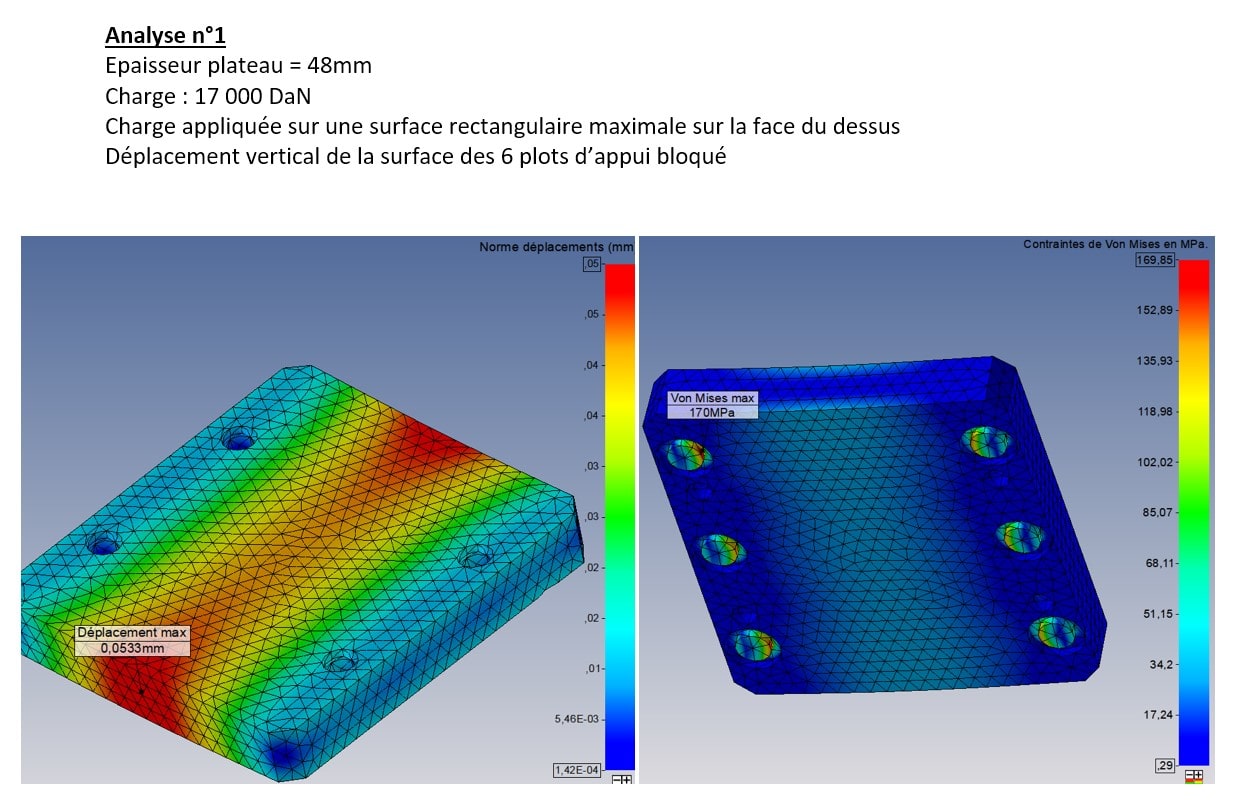
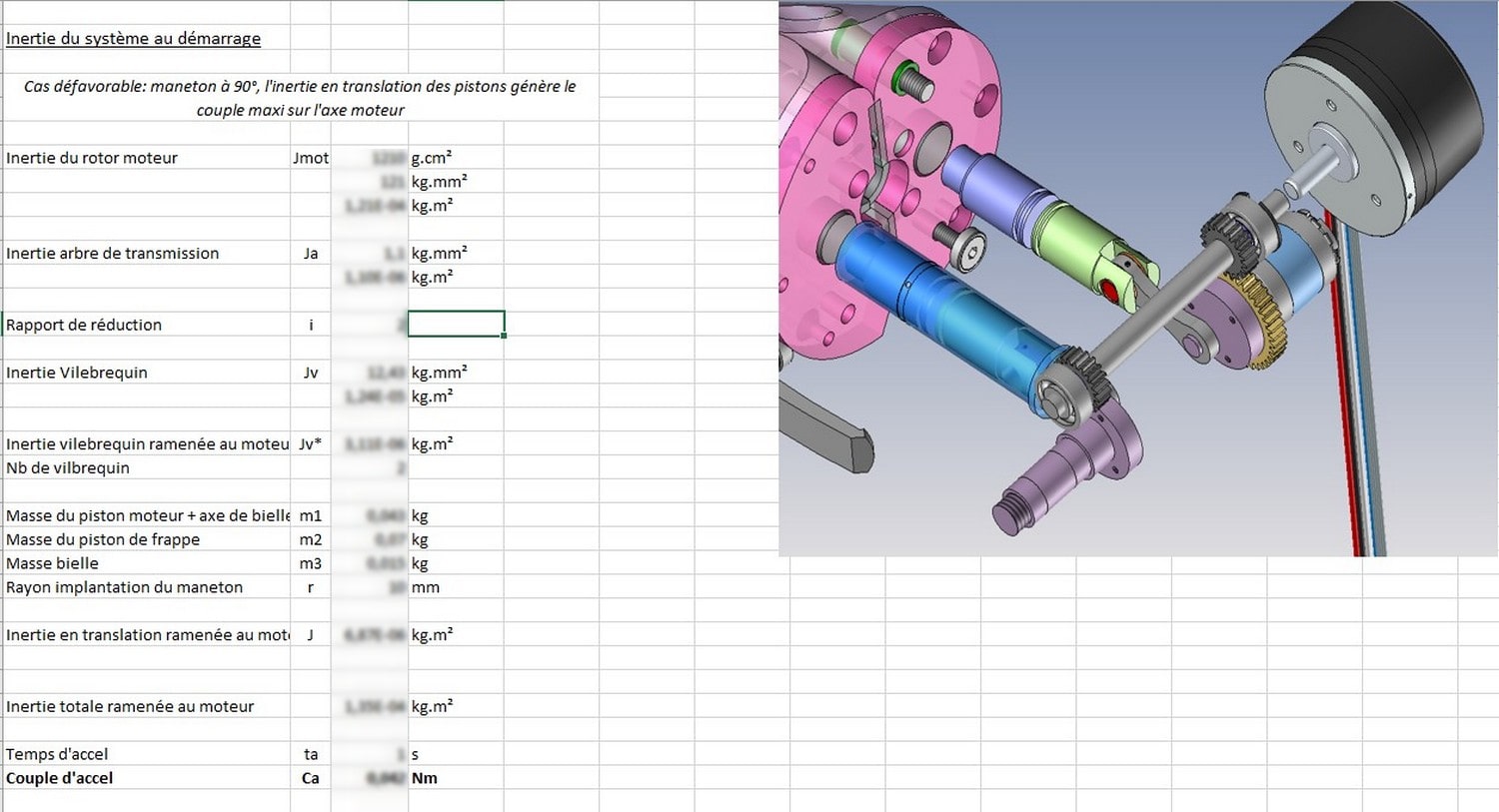
Before any production step, simulation and calculations generally provide very good control of the key parameters in order to achieve a functional, resistant and efficient production more quickly. Digital simulation allows, via specialized technical software, to test different concepts, understand phenomena, anticipate and optimize the operation of equipment by working on its digital model.
On industrial systems or more complex approaches, a prototyping phase can consolidate the simulations, by providing additional answers through testing. After collecting and recording the test data, the analysis of these also involves the use of software and methods of interpretation and formatting.
If necessary, we can develop data analysis and processing systems, for example using LabView, or create calculation routines with Matlab to process more complex modelling equations and resolutions.
Validation of numerical simulations
Any calculation is based on a certain number of reasonable assumptions or simplifications. Prototypes, models, or any other test device can be used to confirm the results of the calculations in real life or to correct the simulation if reality differs from the digital model and the simulated behaviour.
Throughout a project, calculations validate the technical choices and selections of the various components that make up a machine. Indeed, the physical data and expected performances are the basis of our sizing notes of all types:
- Resistance of materials (matting, bending, traction, shearing, etc.)
- Cycle time, cadence
- Servo motorsmovements, motorisation
- Mechanical transmission elements, belts, chains, ball screws, bearings, reducers, couplings, guides, springs, gears, cams, etc.
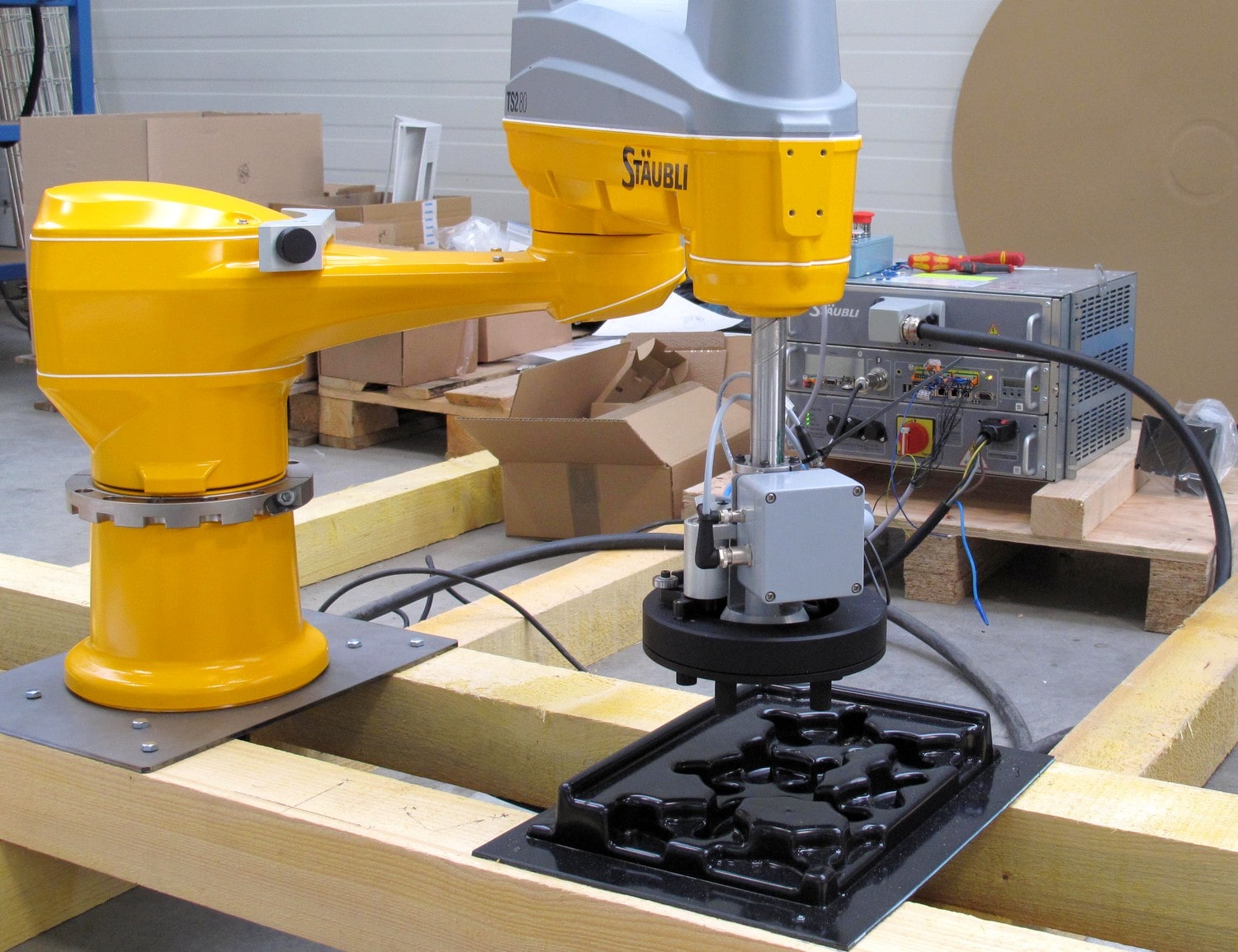
Specific calculation sheets according to the application
- Equipment sizing, cadence, time diagrams, autonomy, estimation of yields, etc.
- Determination of actuators and sizing of motorisation and transmissions (brushless motors, electromechanical, pneumatic, hydraulic components)
- Mechanical calculation of all types: resistance, deformation, static, kinematic, dynamic
- Expansion, assembly by shrink fitting
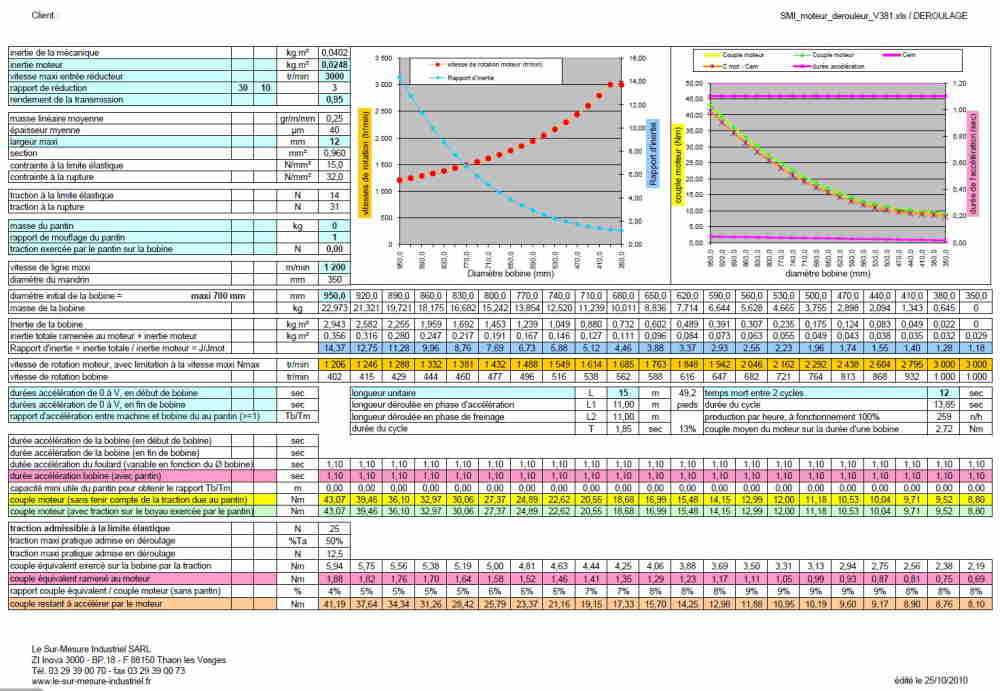
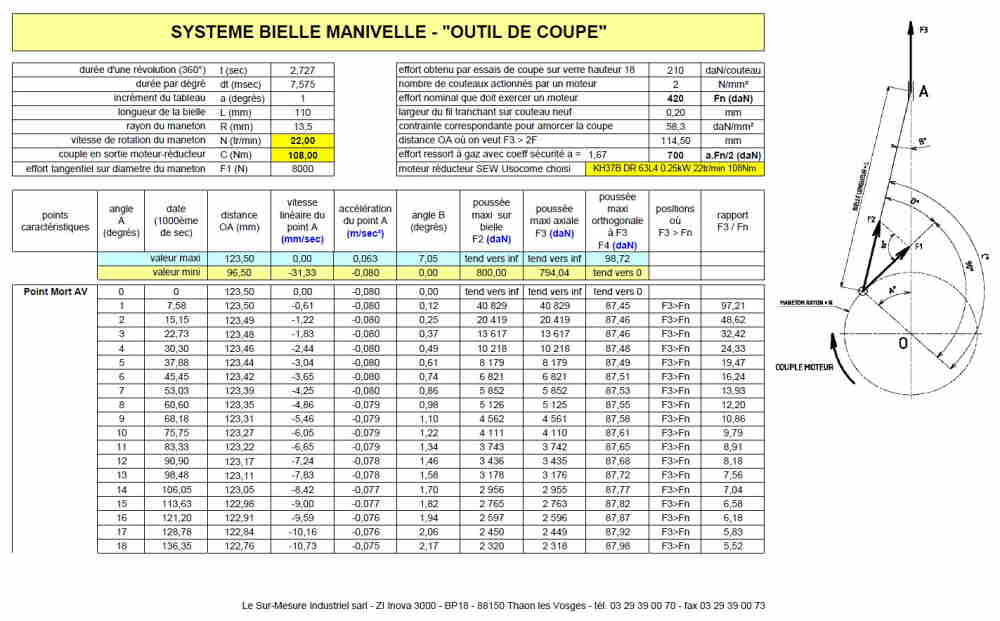
- Cam tracing, laws of motion
- Determination of magnetic couplings, vibration damping
- Study and development of processes, unwinding, winding, deformations, cuts, etc.
- Development and configuration of braking stations for zipline trolleys
- Sizing of presses
- Heating, cooling, pressure regulation
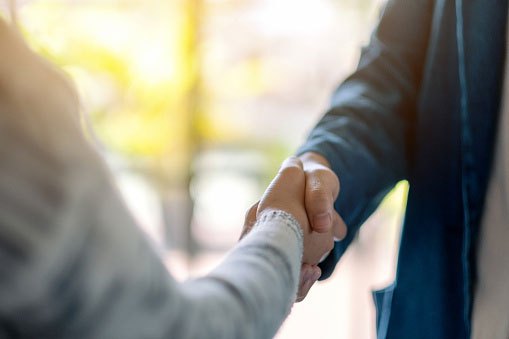
Partnership calculations
Indeed, some applications may require the use of specialized applications, subject to user licenses that we do not have. These software programs also require specific skills and expertise for their correct operation.
In some cases also, the meshing of large parts or assemblies becomes limiting with our available software and hardware resources. The simulation would be very long or even impossible. In all these cases, we prefer to subcontract the work to partners:
- Dimensioning checks and reports according to specific codes on finite element models: Large assembly, Eurocodes, lifting, etc.
- Advanced numerical simulation in vibration analysis, acoustics, fluid mechanics, aeraulics, heat transfers, thermodynamics