Industrial Automation
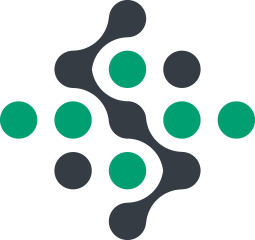
Programming of PLC
We have all the skills in electric and industrial automation within our design office to support you in your projects.
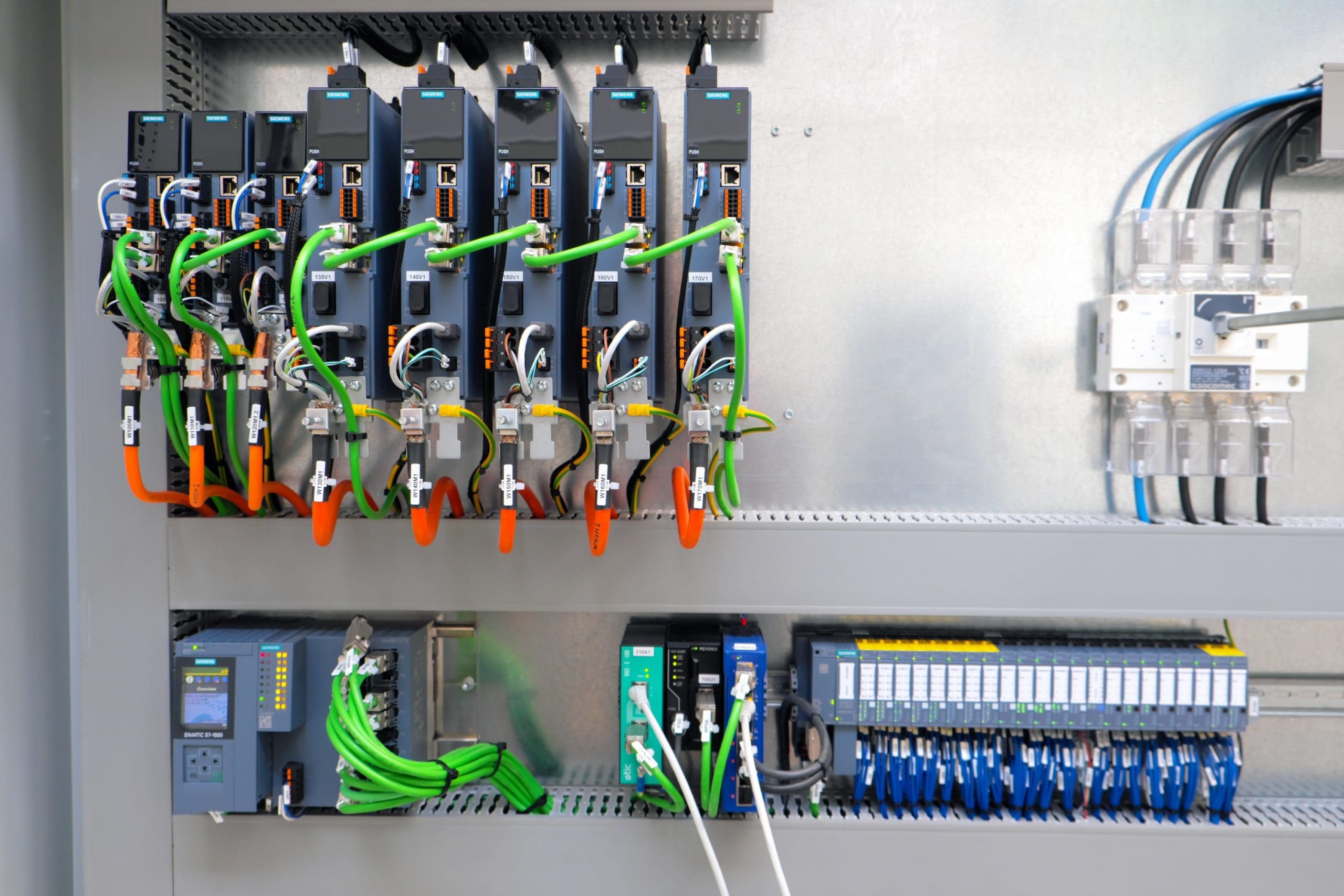
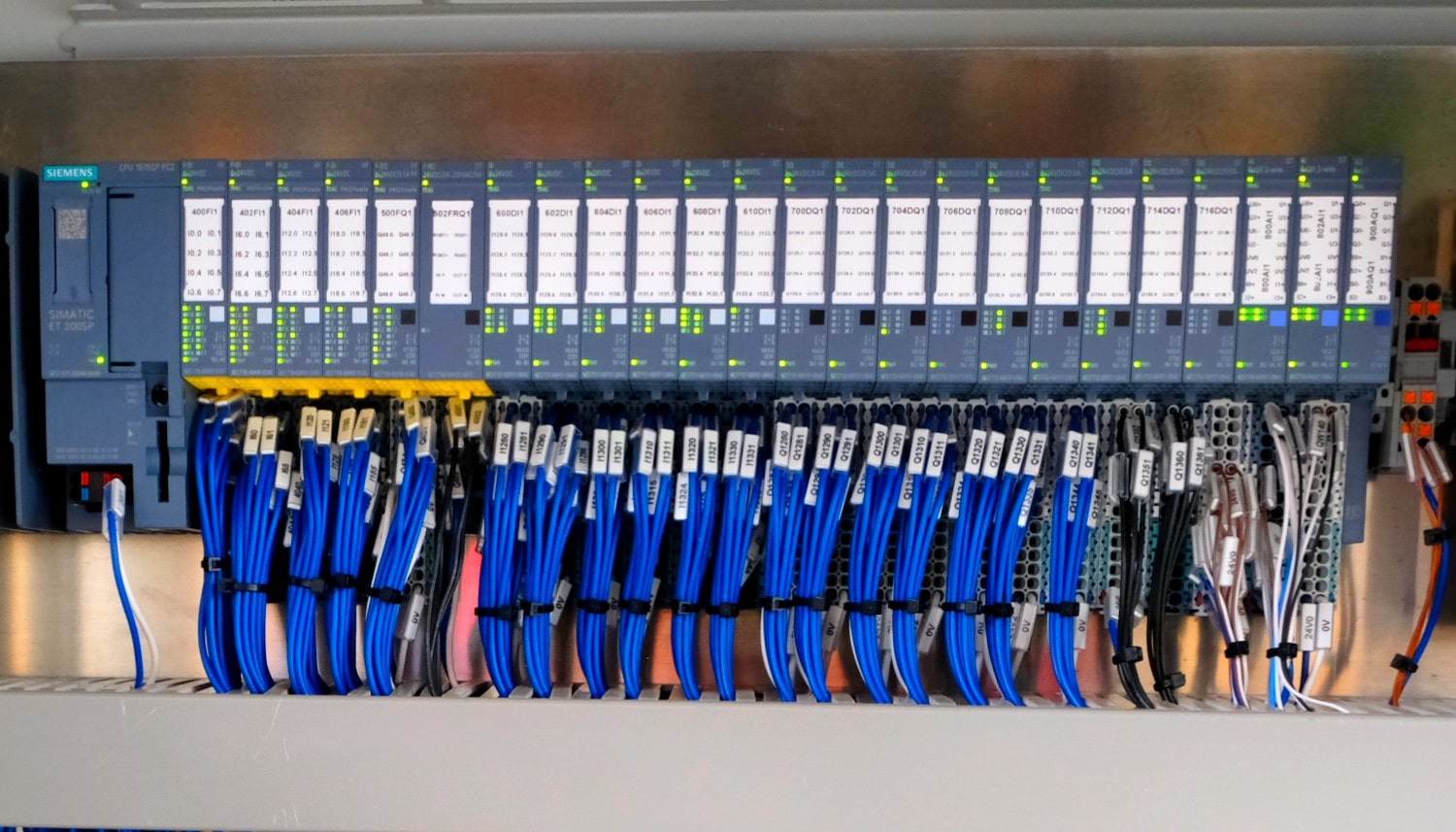
Examples of services in Electrotechnics & Automation:
- Functional analysis
- Dimensioning and selection of electrotechnical components
- Electrical and fluid schematics
- Fuse box design
- Detailed nomenclature of components
- Programming of automatons, dimmers
- Process automation
- Development of advanced HMIs that effectively support operator and maintenance personnel
- Possibility of remote control
- Interfacing with robot programs
- Pressure and temperature regulation applications, etc.
- Retrofitting / modernising electrical machines
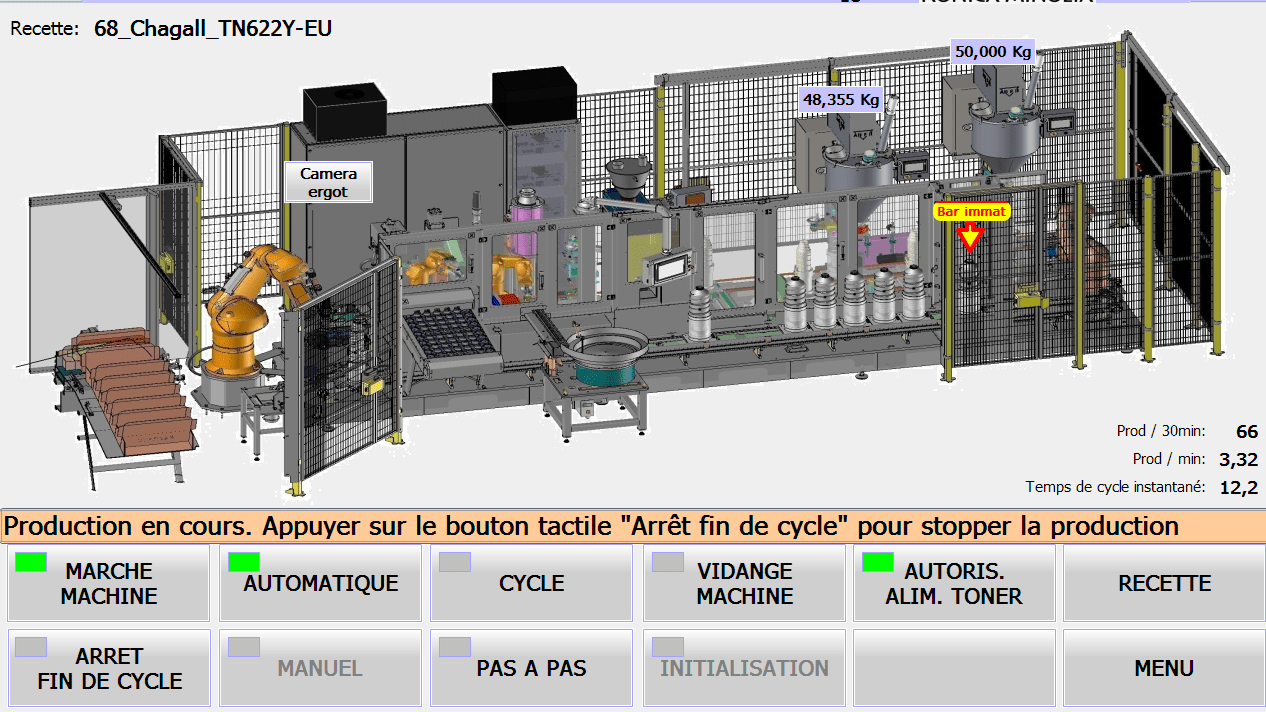
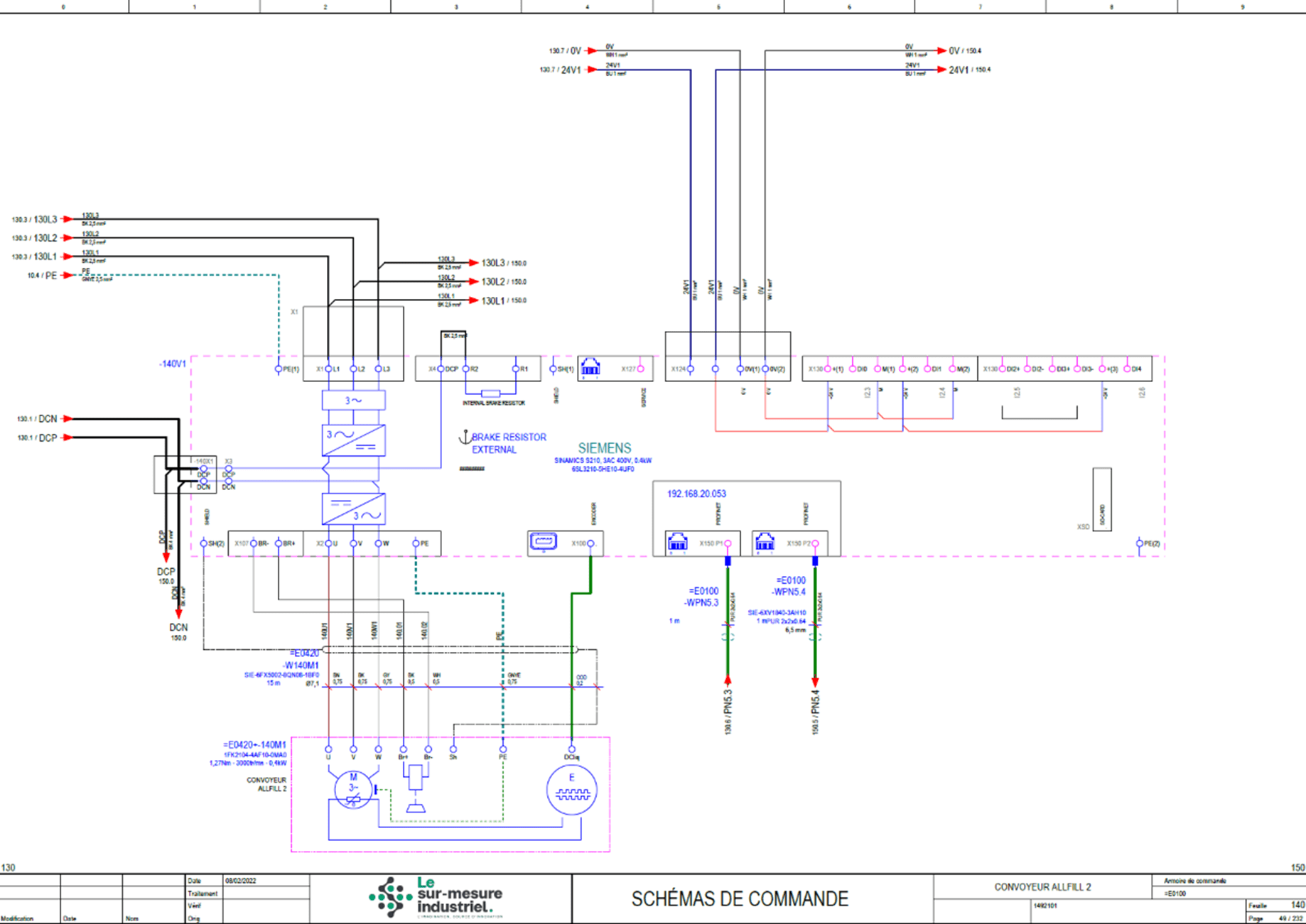
Automation of your operations
For the automation of processing, assembly, packaging operations, or for any other project that involves the programming of automatons, you can call on our company. We are experienced in the selection and implementation of suitable equipment and technologies to meet your specifications or industrial issues.
During the studies and according to the expected functionalities of the equipment, our team selects and sizes the most suitable automation components. The electrical and fluid diagrams as well as the detailed electrical cabinet designs are then produced on our high-performance computer software.
Then comes the programming and development of our machines with clear objectives: reliability, performance, robustness, flexibility, easy maintenance.
For what applications?
The applications involving PLC are multiple and varied: process regulation, sequence of operations, use of various sensors and actuators, interfacing and communication with other equipment or supervision, automation of controls, setting mechanics in motion, programming of movements, industrial robots, testbed, etc.
Discover our areas of expertise
Le Sur-Mesure Industriel supports you in your projects, ensuring the design, manufacture and wiring of your machines. From studies to delivery, commissioning, training and maintenance.
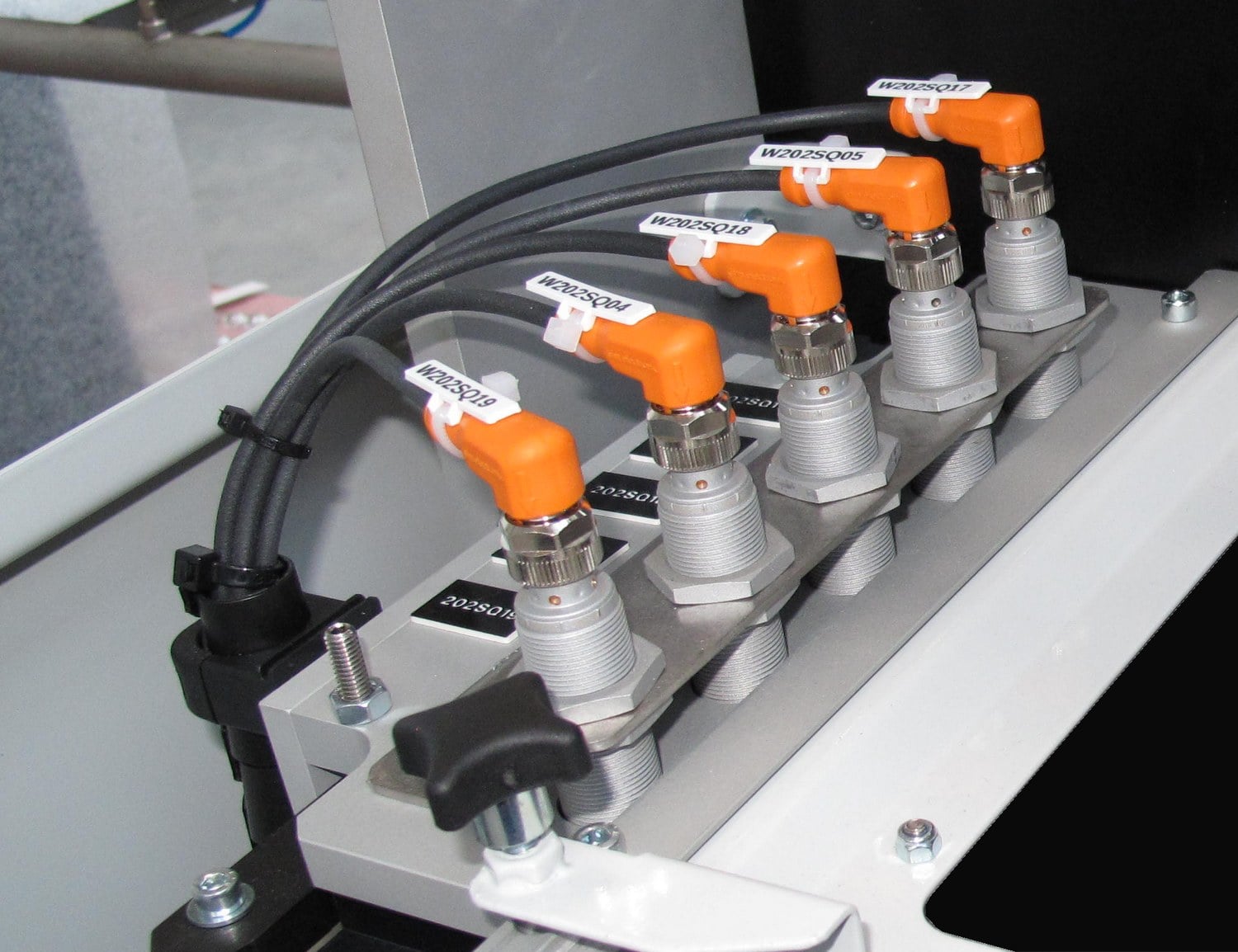
Automation and programming in pictures:
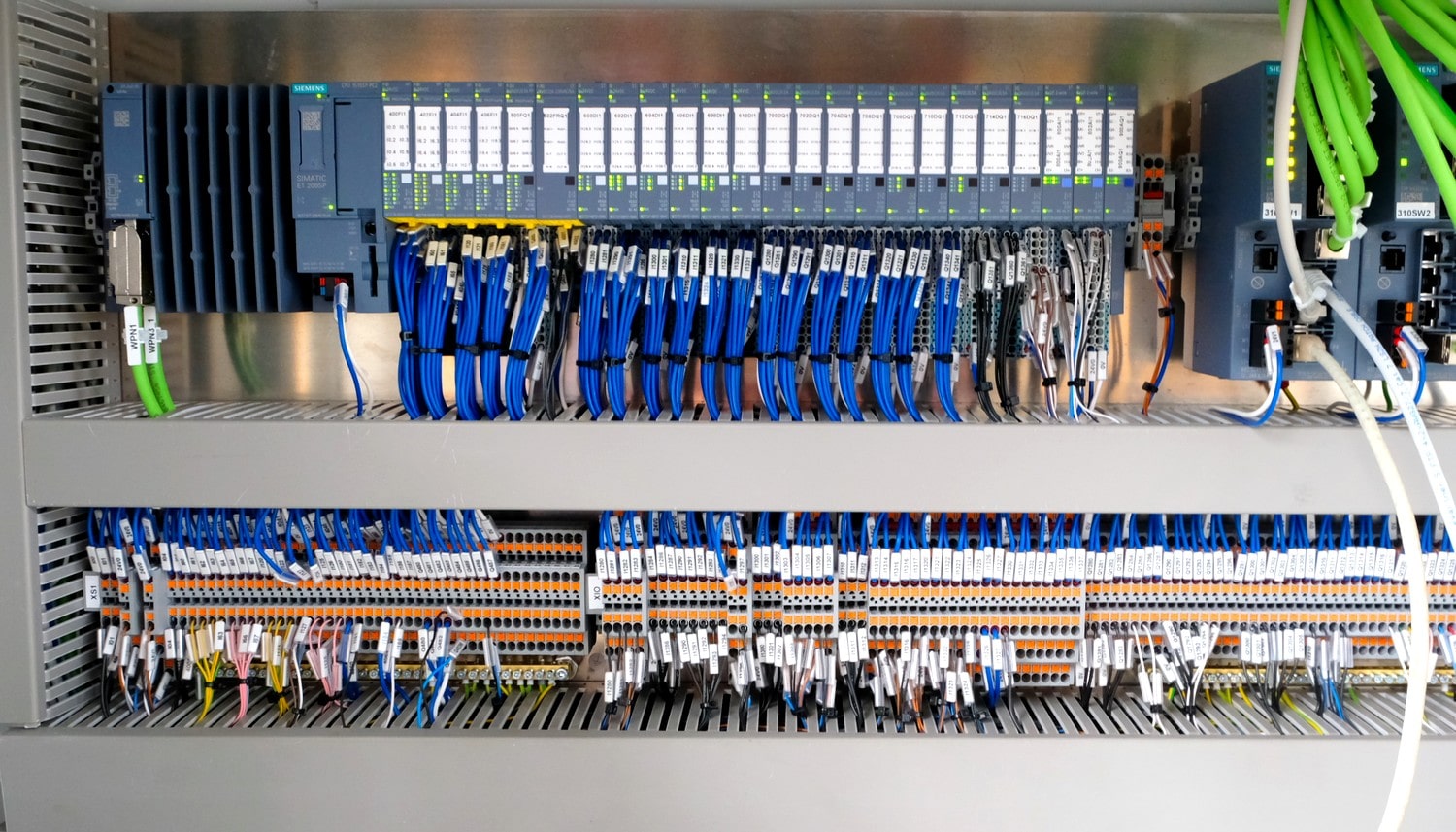
Creation of automated systems
- Servo motors, brushless motor control, dimmers
- Programmable automation and industrial computing, Human-Machine Interfaces
- Process regulation and instrumentation (temperature, flow, pressure, humidity, force, etc.)
- Industrial networks and communication
- Pneumatic and hydraulic energy, distribution islands
- Industrial robot
- Machine vision cameras
Digitalization and industry 4.0
At the heart of the installations, we very often integrate control systems in order to monitor the important characteristics of the products processed or of the equipment itself. The automation systems that we develop display, communicate or record production data: counters, defects, operating mode, rate, reject rate, etc. Depending on the need, we can also propose the use of an industrial computer system, for the acquisition and processing of larger volumes of data.
The digitalization of equipment allows the exploitation and analysis of data collected via network connections with other remote systems and equipment.
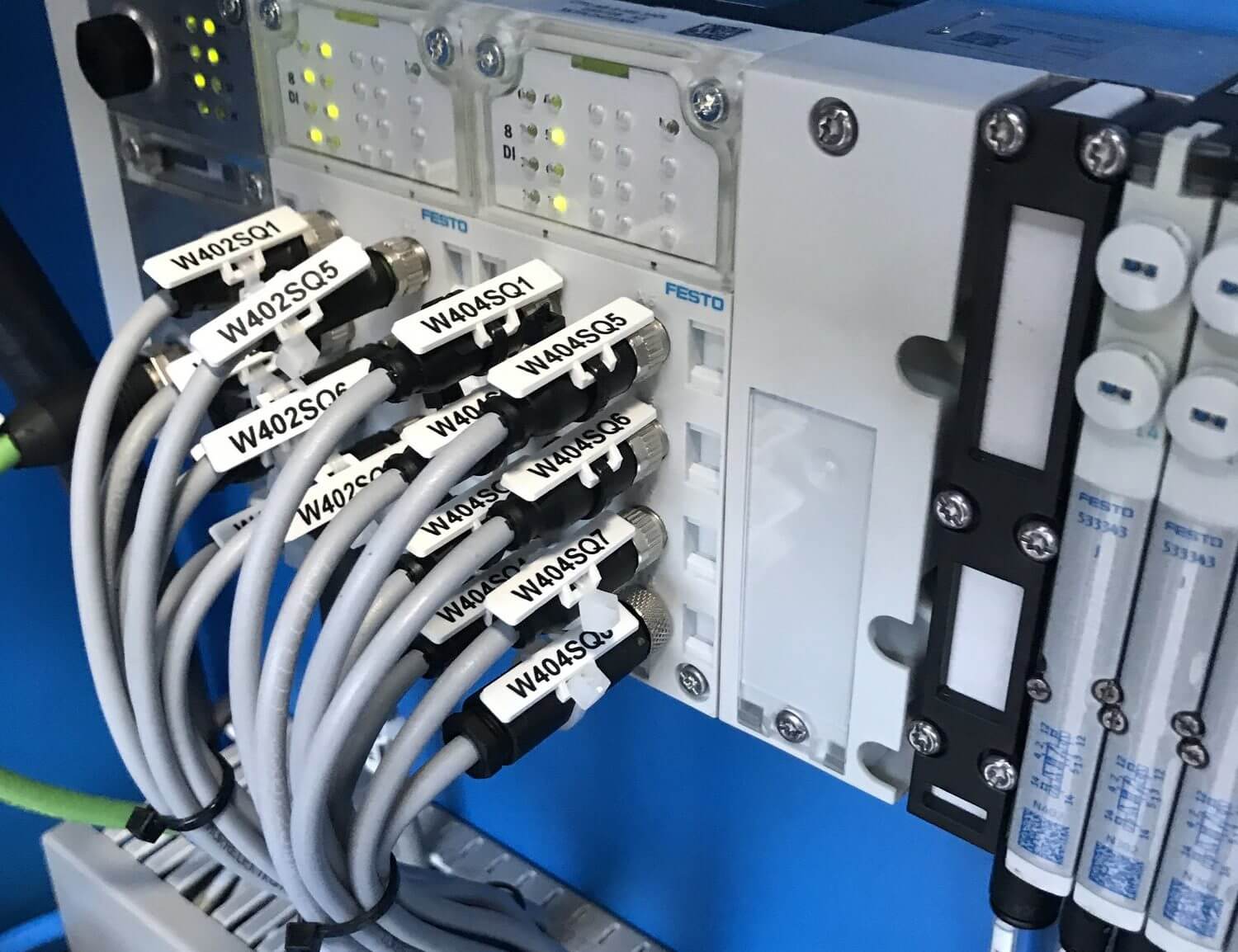
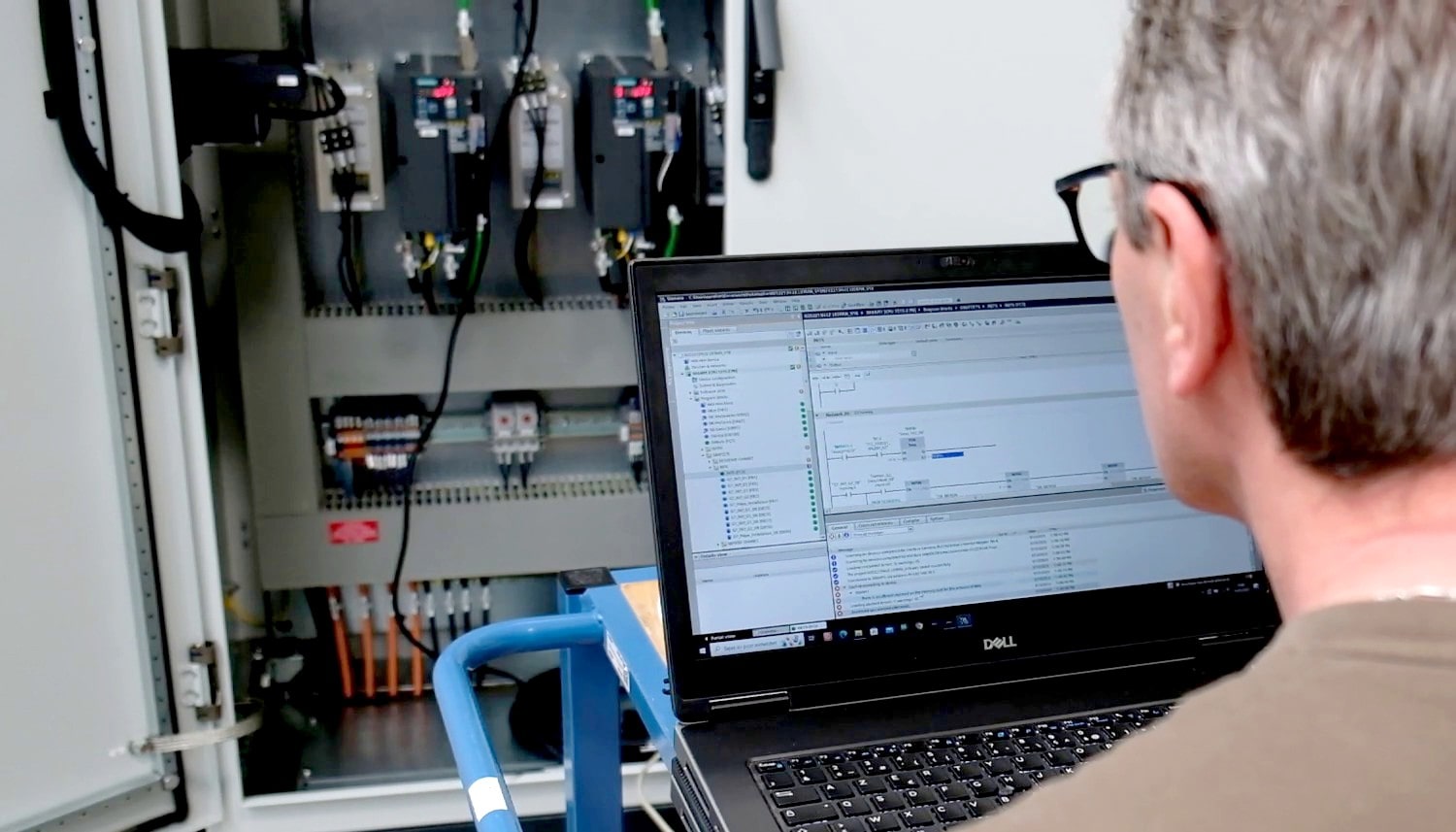
Remote connection
After the commissioning of an installation, our team obviously remains at your service for any after-sales service request.
For these needs, the connectivity of the equipment we develop also represents a great advantage after delivery: a diagnosis or troubleshooting is sometimes possible remotely, which ensures you minimized downtime! If necessary, an engineer or technician from our team can also remotely carry out additional training for system users.
Sizing and configuration of servomotors
For a given application, our engineers and technicians study, select and size the motors as well as the transmissions and the control chain during the design phases. We produce technical calculation notes in order to correctly configure the drive system according to the forces and torques involved, but also the speeds and accelerations expected for the moving parts.
Some examples of the use of servomotors and drives in our industrial machines:
- Servo motors and translation or rotation: precise and dynamic movements
- Press axis: stroke and force control
- Winding: tension and speed management
- Drive of conveyor mechanism, elevator, etc.
- Assembly robots, handling robots, etc.
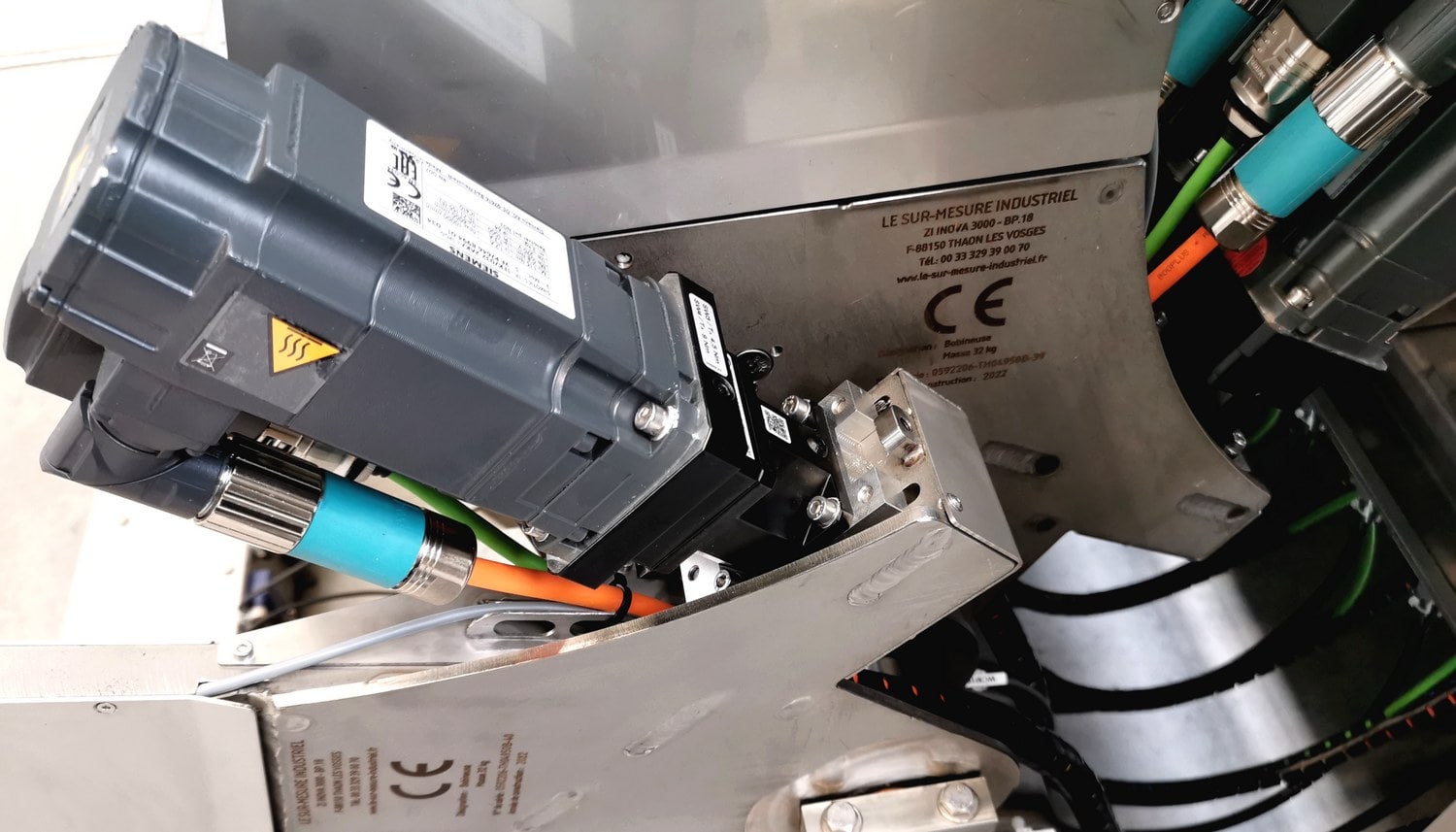
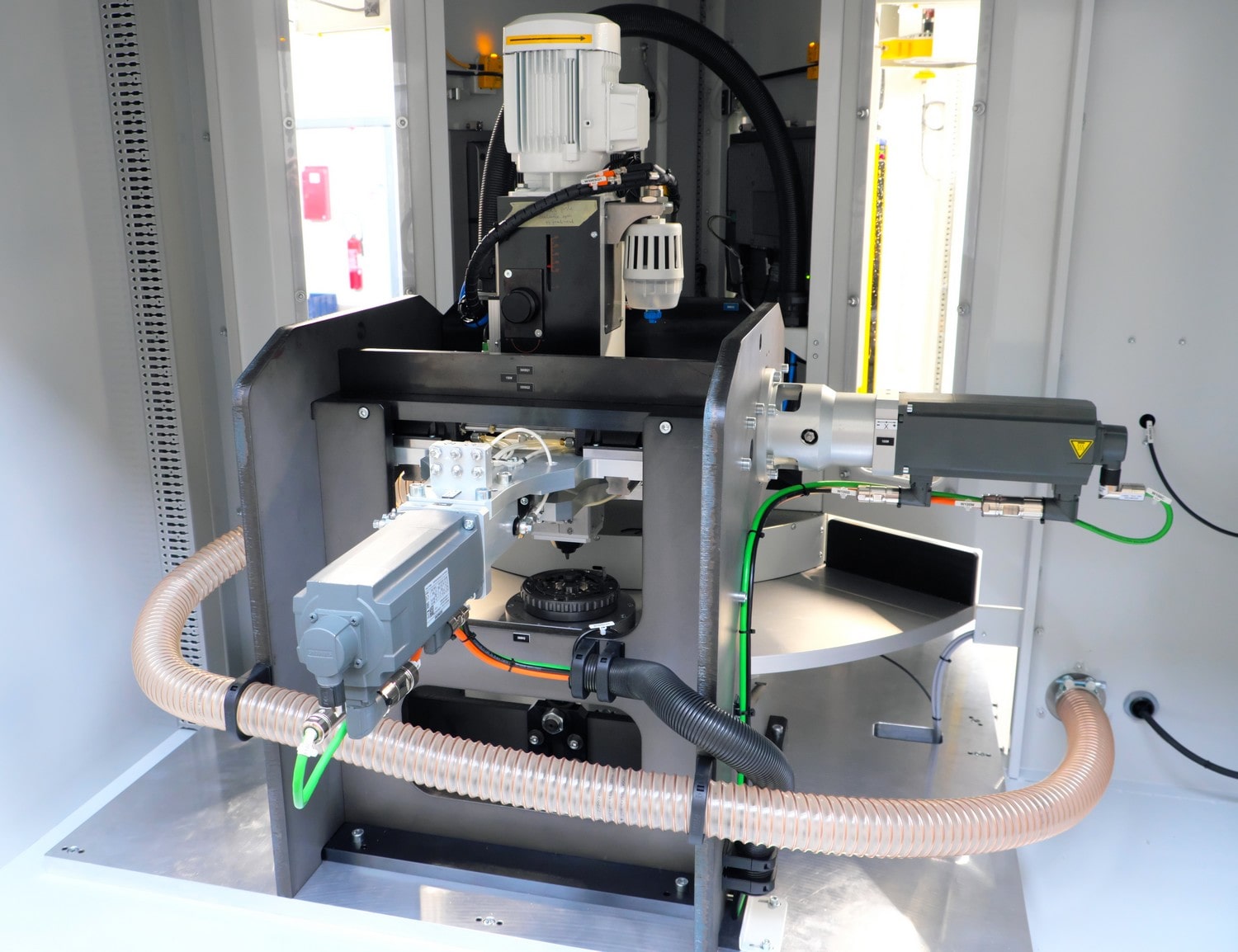
Simplified settings thanks to automatons
Industrial automation makes machine settings easier for you. For many pieces of equipment, it is very useful to store different sets of parameters in a computer, entered in a program or programmable recipes.
This allows you to change production very quickly, by calling the right settings for the product to be processed. This type of setting also gives flexibility to the equipment because it is possible to subsequently create new sets of values, to correspond to another reference, or another application for example.
The parameters can be different dimensional values from one part to another, different instructions depending on the chosen test, a robot or camera program call associated with the products being produced, etc. The management of these manufacturing recipes is done via PC, HMI, or directly in the programmable controller.
Automated production
Thanks to automation, it is also possible to set up compensations or automatic adjustments on industrial processes. Thanks to the use of a measurement, control or detection system, the PLC uses the values and makes adjustments or generates alerts.
With correct configuration of instructions, thresholds and actions, the equipment becomes more autonomous, more reliable, easier to control, and the regularity and quality of production are improved.
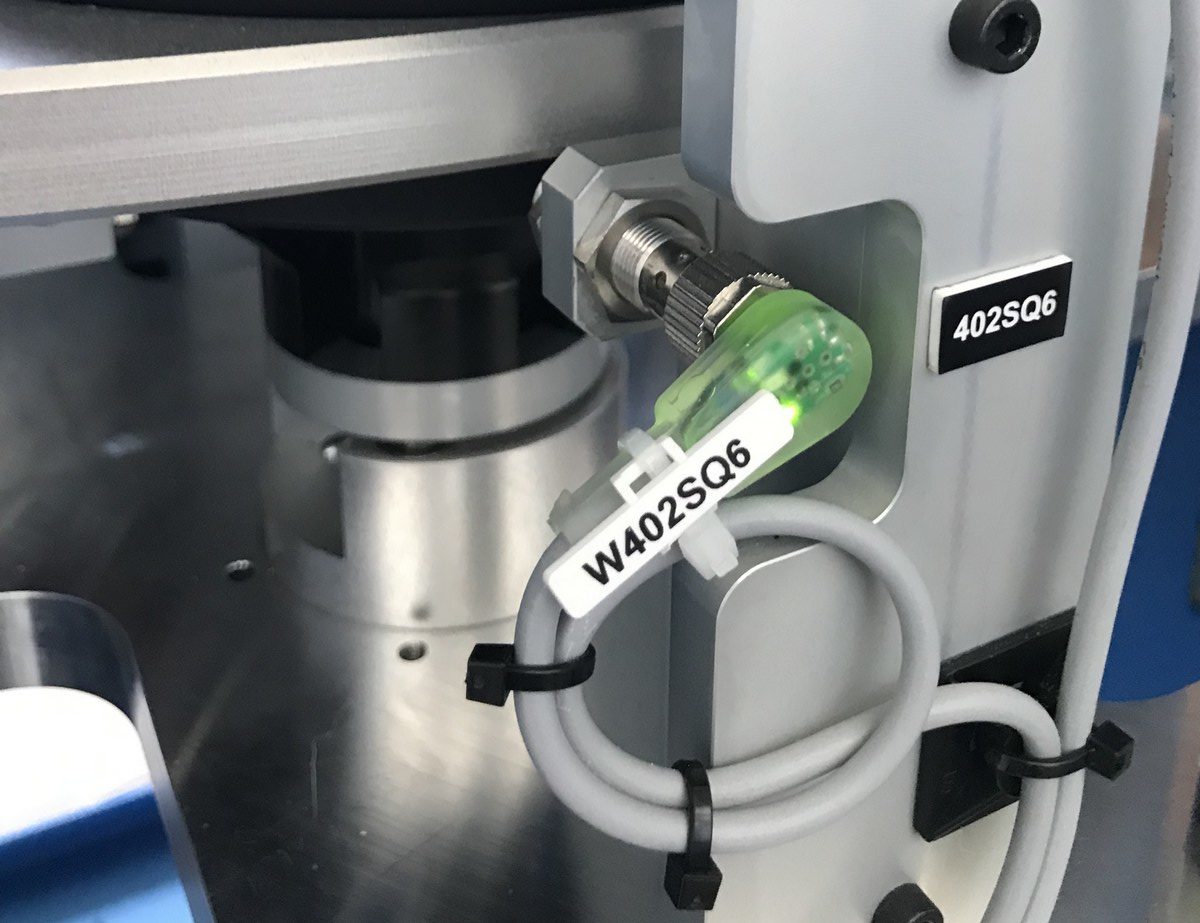
Functional analysis and automation of systems
Collection of information on operation
When we study and produce automated industrial equipment, we take care to analyze its entire operation. Indeed, by exchanging a lot with our customers, it is important to define how the machine will behave, according to the different situations and possible interactions.
During these phases, it is very important to involve and consult the different users: production, operator, quality department, maintenance, etc. The experiences of each, combined with our point of view as a machine manufacturer, will then contribute to the provision of a functional and suitable system.
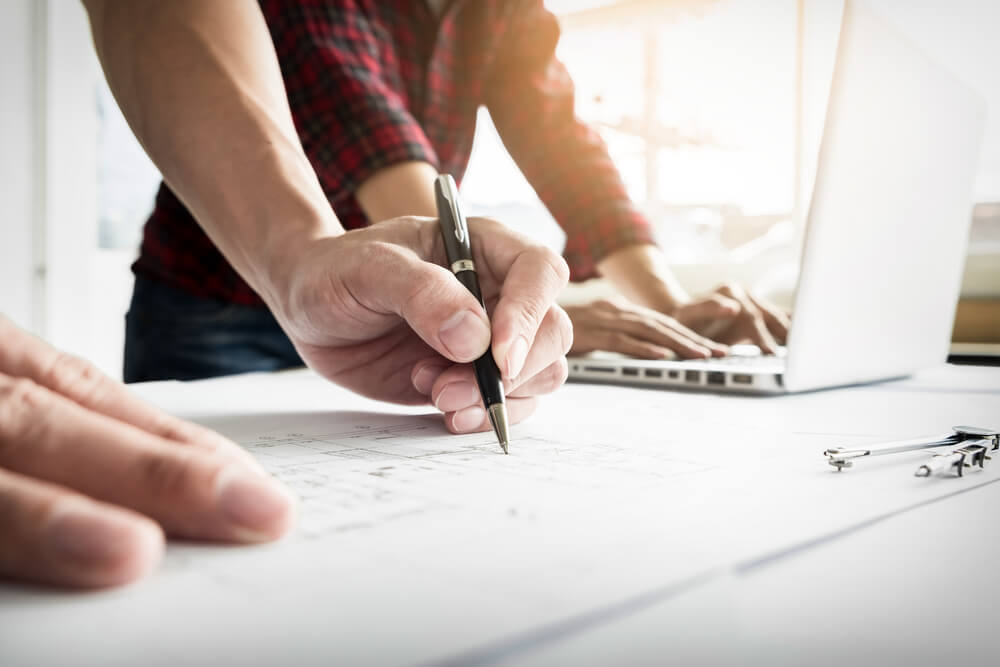
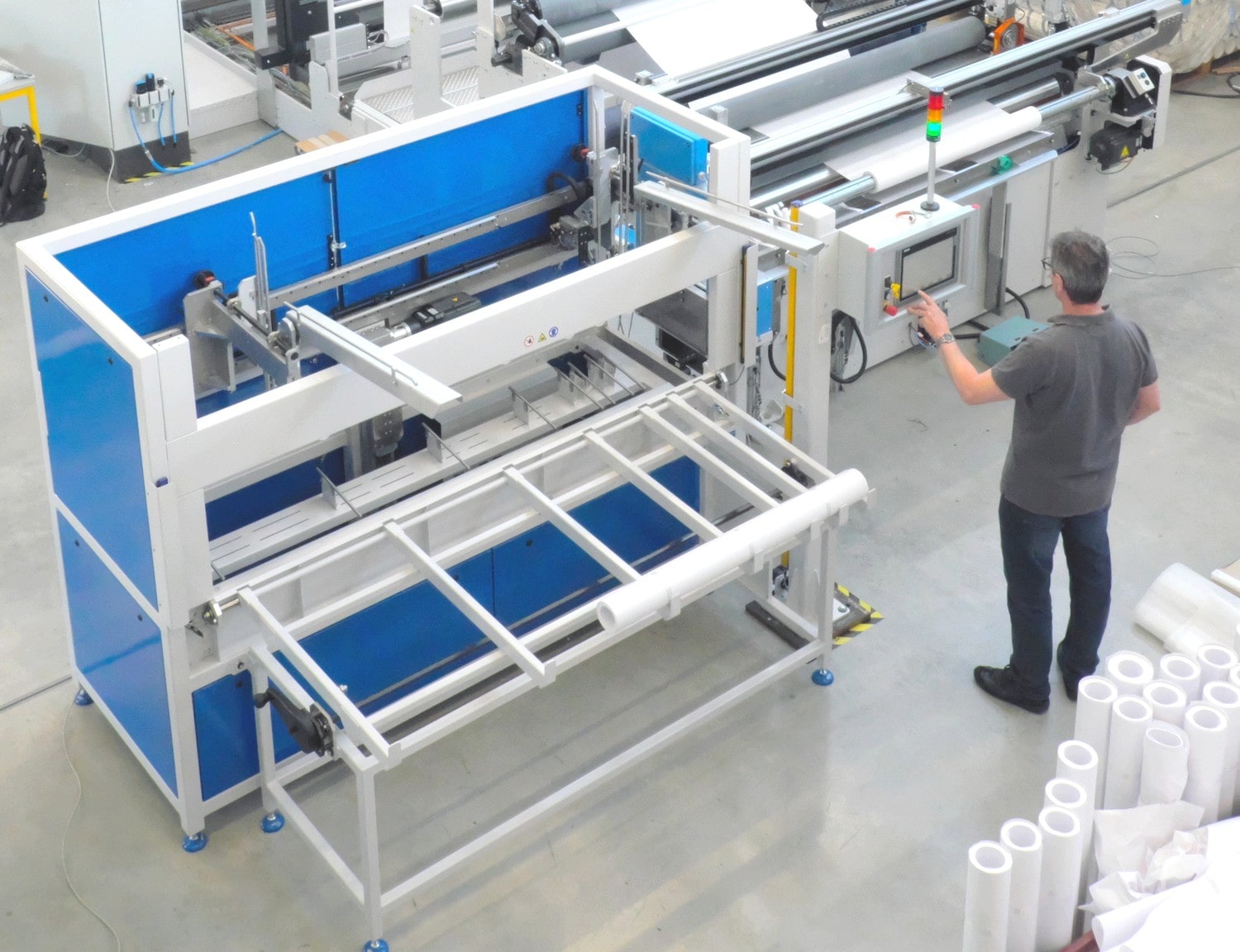
Programming of operating modes and interfaces
Our automation engineers program different operating modes for the equipment: initialization, calibration, normal automatic cycle, draining, manual mode, cycle resumption after shutdown, alarm and fault management. Generally, the machines are controlled via HMIs whose different pages are also created by our team. They effectively support the operator and maintenance personnel for the different interactions with the machine, thanks to clear and accomplished presentations.
Automation service to support your teams
Our automation engineers obviously program the machines we design and manufacture. They can also manage subjects that only require their skills in electrical engineering and automation.
This is the case, for example, when they make modifications to existing programs, add functions, or when they replace electronic components during complete retrofits of machines and electrical cabinets. These subjects require studying the available documents and programs on a case-by-case basis in order to offer you the most suitable services.
As part of new projects, our automation engineers can also step in to temporarily lend a hand to your teams for the programming and development of industrial equipment and installations
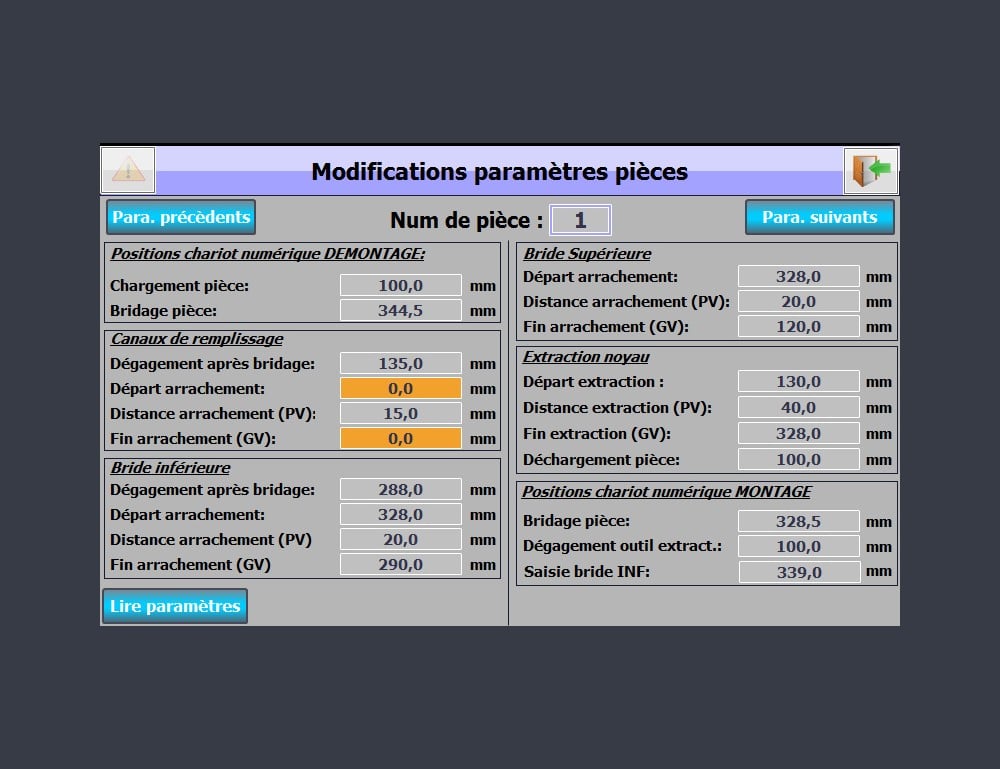
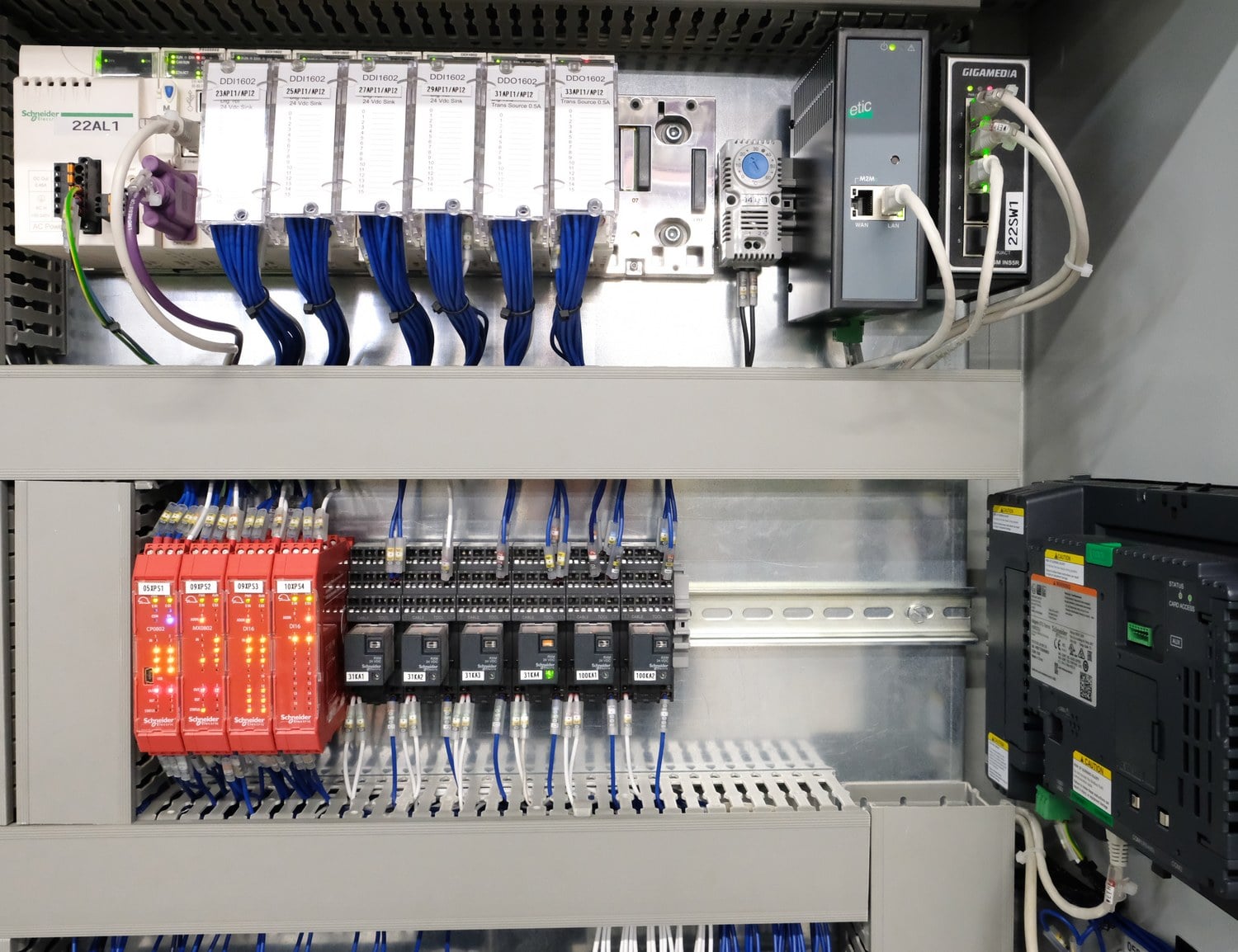
Safety of industrial equipment
We also pay very particular attention to the safety of the equipment users. From the feasibility stage, then throughout the mechanical, electrical and programming study, the risks are identified, evaluated and treated.
Our design office determines the appropriate technical solutions to reduce or eliminate dangers: sensors and safety chain, programmable safety automation, analysis of performance levels, choice and implementation of safety equipment.
Le Sur-Mesure Industriel designs installations that comply with the various applicable regulations or recommendations (labour code, directive 2006/42/CE, ergonomic guides). We conduct risk analyses and produce the EC declaration of conformity for our machines.