Industrialisation
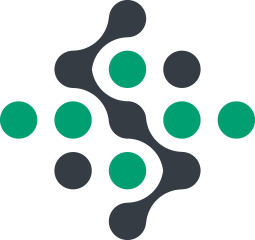
Industrialisation of products or systems
Industrialisation involves designing products while considering all stages of production required for their realization.
This includes selecting production processes and methods, assessing industrial feasibility, equipment capabilities, economic constraints, production volume, expected finish quality, and more.
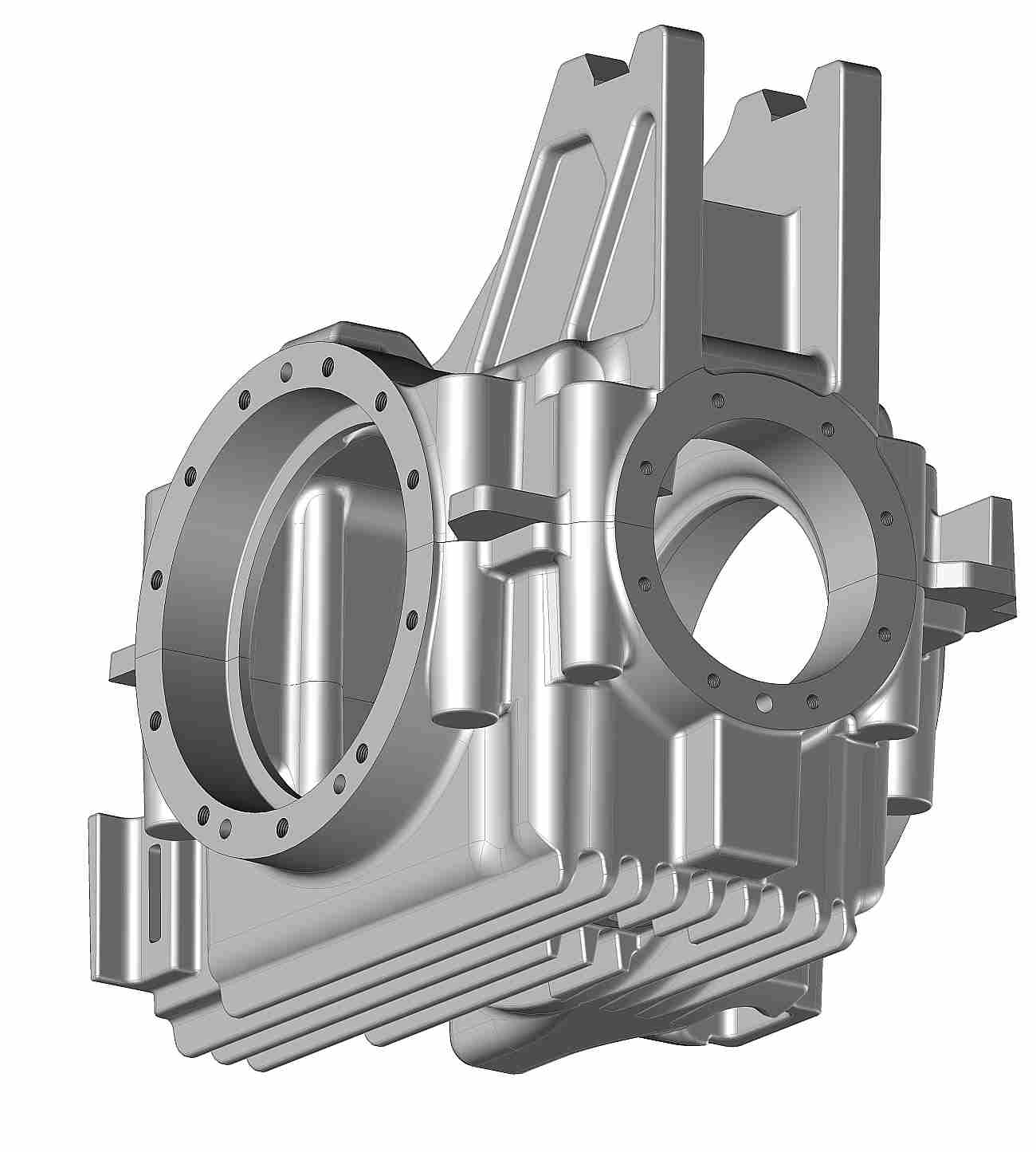
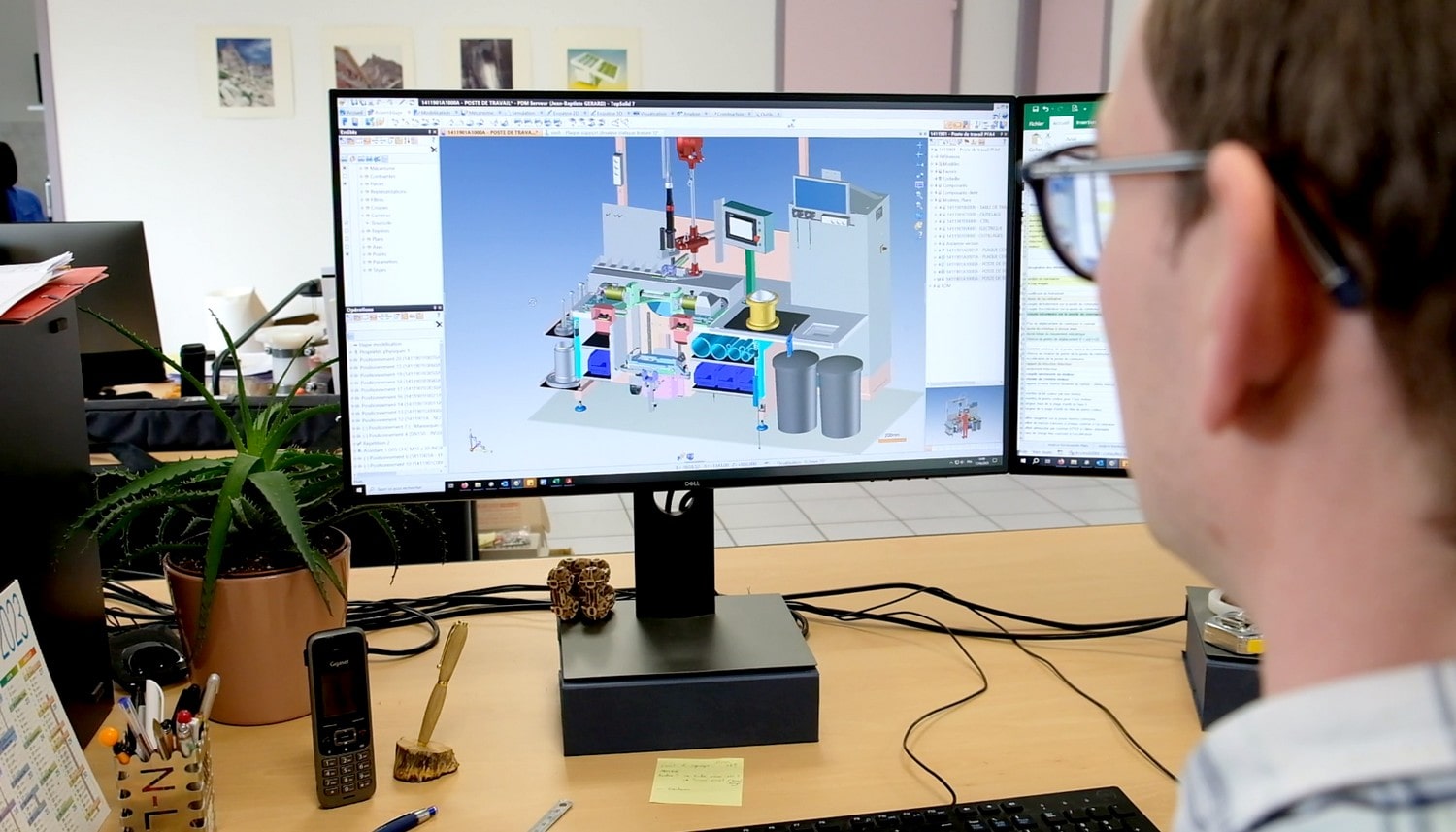
Our support for industrializing your products
Traditionally, an industrialisation department within a company prepares serial production for equipment developed by its R&D or design office.
In an outsourcing context, we act as a contractor or service provider to manage the R&D portion in collaboration with the client, with the goal of industrializing the design of equipment by directly integrating functional requirements, manufacturing methods, and cost targets.
Industrial equipment, examples of pure industrialisation projects:
- Optimizing functionality and manufacturing costs for a range of vision control machines
- Designing casings for a range of injection moulding machines
- Developing an airport trolley distribution terminal
- Modelling heat pump casings
- Design and layout (manufacture and assembly) of an all-stainless steel grill based on concept drawings industrialisation of an automatic quality control machine based on an initial prototype
- Industrializing an automatic quality control machine from a prototype
- Equipment design
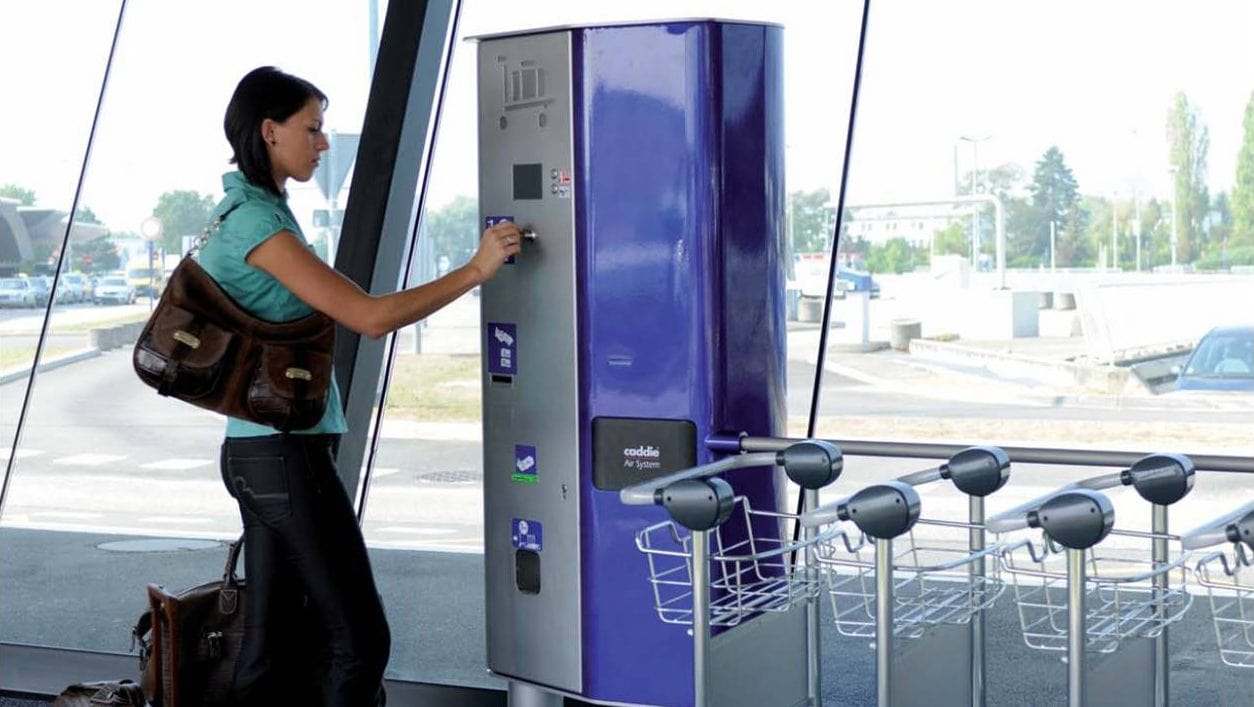
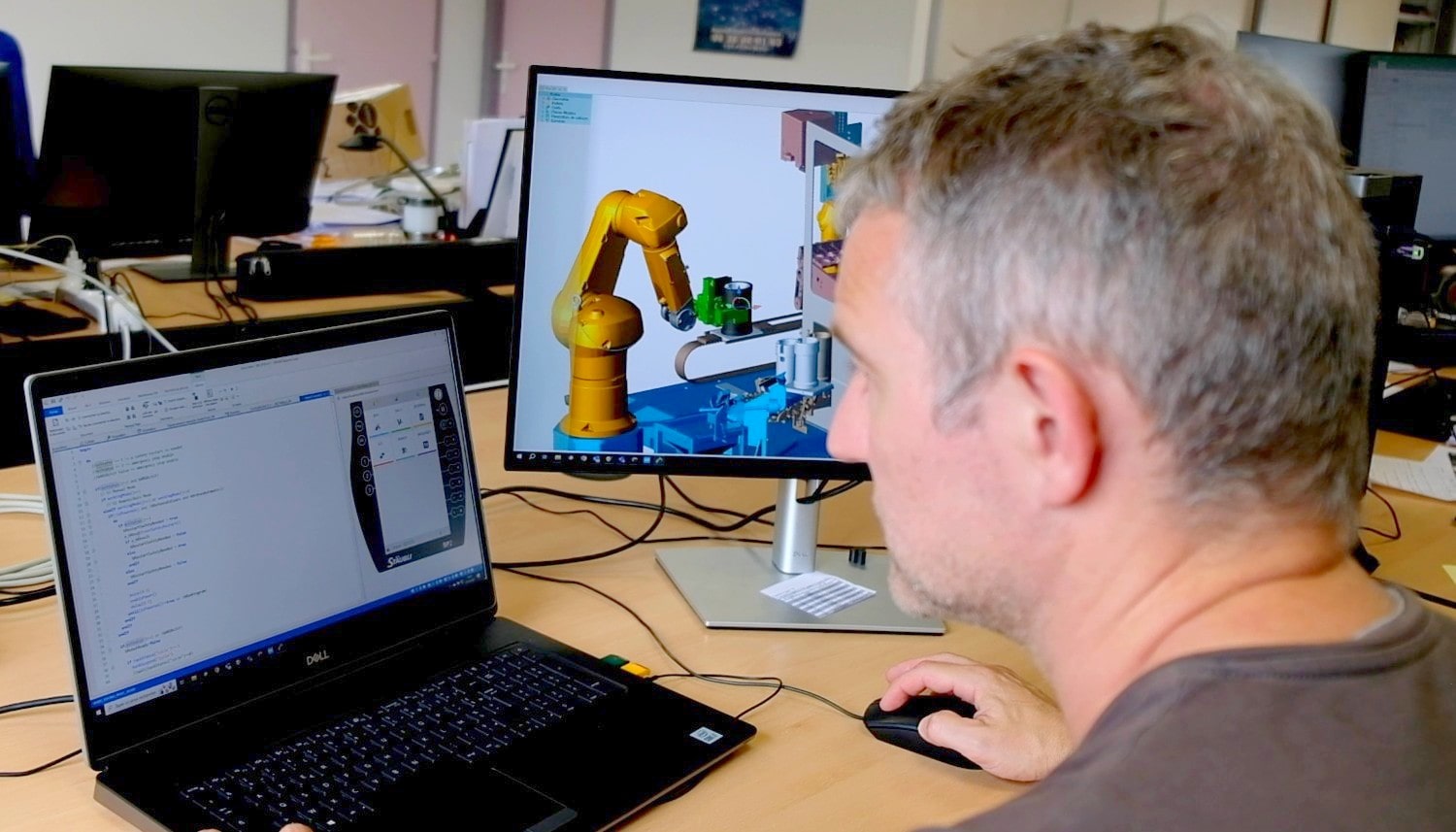
Our services
We put all our expertise and skills at your service, with the aim of finding the best technical and economic compromise to optimize the production costs of your products or machines.
Industrialisation studies, execution, and commissioning
Very often, our service extends to the production of prototypes and small series, enabling us to validate the functionality of the equipment and the technical and economic constraints of production.
We supply all the product design documents with the equipment: CAD design, detail and assembly drawings, parts lists, electrical and pneumatic diagrams, source programs, user and maintenance manuals. This represents a huge advantage for the validation and series production stages of the various systems studied.
We support you in the development of the industrial equipment we supply, as well as in the maintenance and upgrading of the equipment, to provide you with a turnkey service.
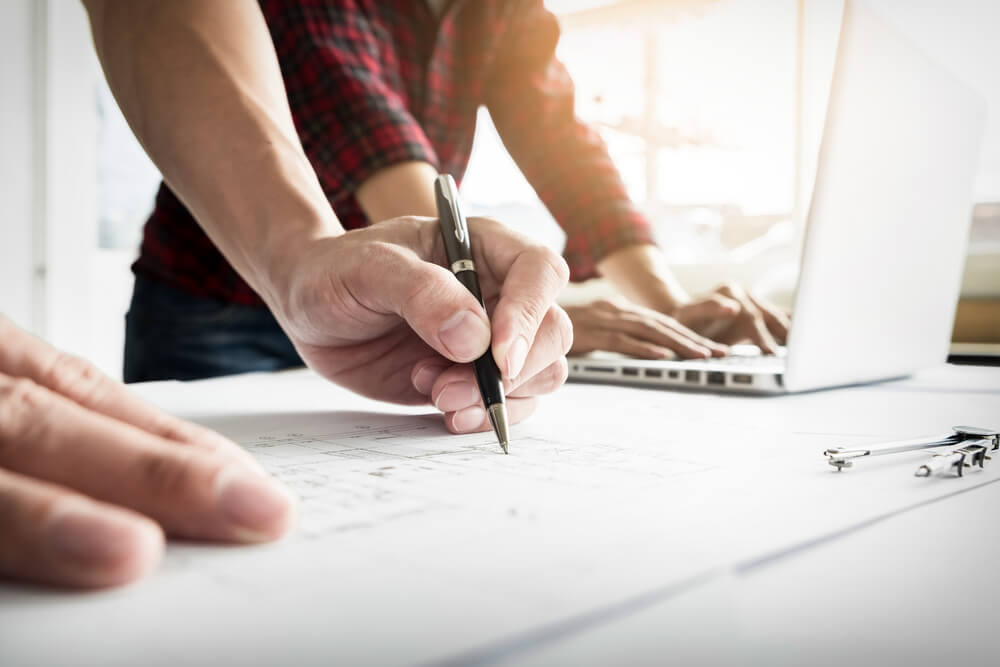
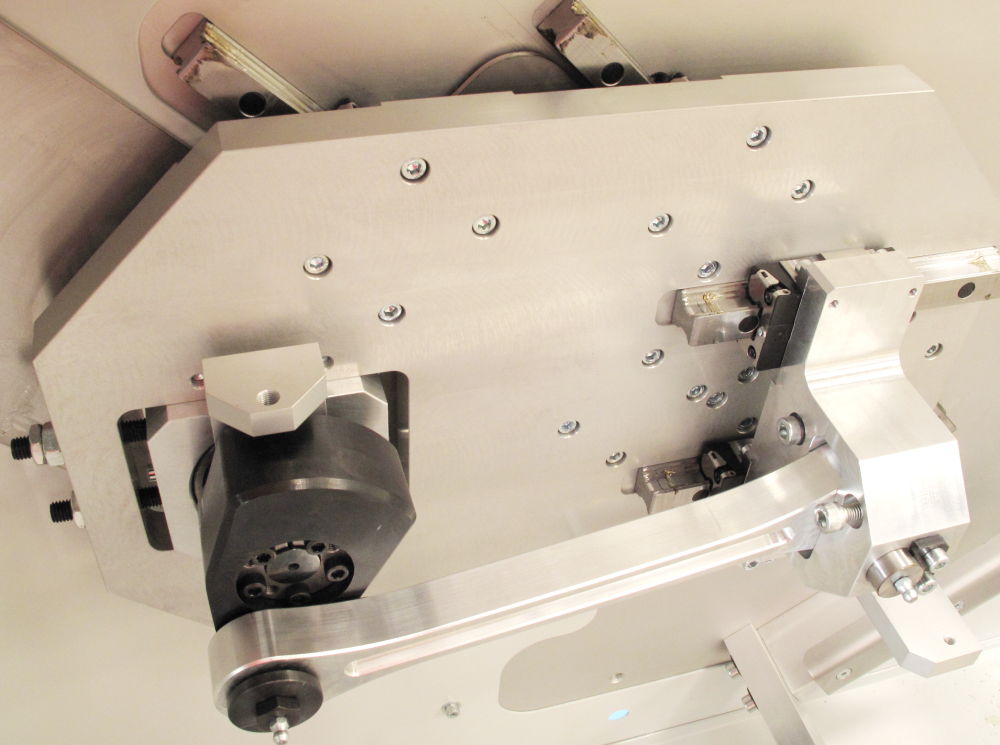
We supply industrial equipment
Serving industries and their production, industrialisation, maintenance, quality and continuous improvement departments, Le Sur-Mesure Industriel designs and manufactures industrial equipment for many companies in France and around the world.
We deal with a wide range of subjects, from ideas, requirements and specifications, through the design and production stages, to commissioning and after-sales service. We have a wide range of skills: mechanical engineering, electrical engineering, pneumatics, hydraulics, automation, robotics and machine vision.
Evolving or addressing new needs
To develop or complete your workshop, or to meet a new need in your company, we design and manufacture special machines, equipment, tools, checking fixtures, measuring equipment and testbeds.
This includes creating entire assembly, packaging, or production lines, automating functions, modifying machines, and improving workstations.
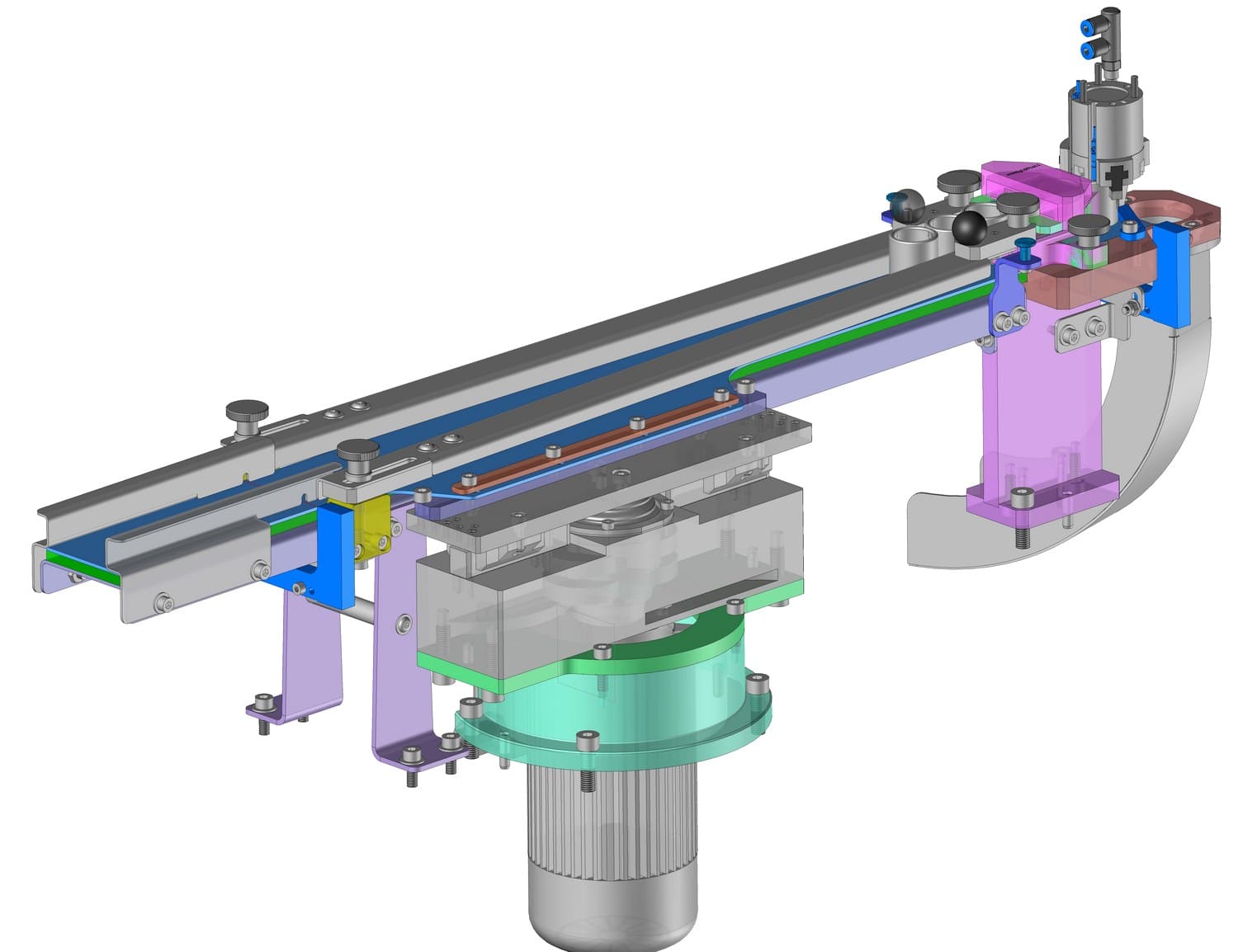
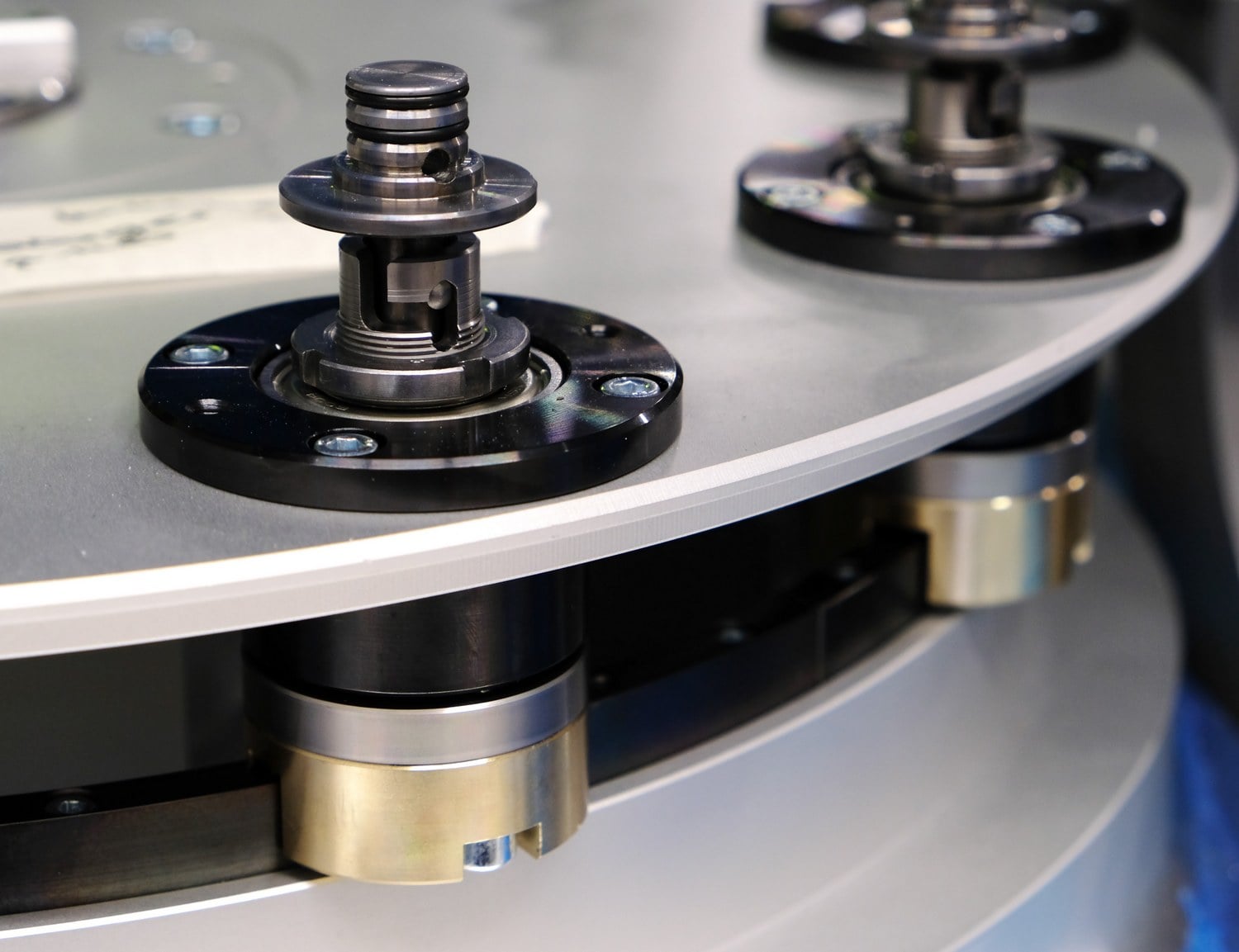
Design and supply of industrial equipment for production, control, packaging, etc.
As a machine builder and supplier of industrial equipment, our company is located in the Vosges region of eastern France. We develop production, manufacturing, inspection and packaging resources for our customers in a wide range of sectors.
We build machines that are adapted to the specific requirements of the field of application and the products concerned.
Furthermore, we carry out studies on transformation processes and trials to provide innovative and relevant technical solutions, as well as defining the right equipment according to your specifications and expectations.
Industrialisation and production processes
Based on specifications, a concept or an innovation, the first steps towards mass production of a product are the design studies and the prototyping phases. The purpose is to define all the technical and design details of each component, obviously taking into account the means of production and manufacturing costs.
It is very important to take into account the entire life cycle of a product or machine when designing it:
Manufacturing, methods, assembly process, quality control, packaging, transport, dismantling, maintenance and recycling.
We support clients by analysing these stages to implement optimisations early in the lifecycle of the equipment or the product.
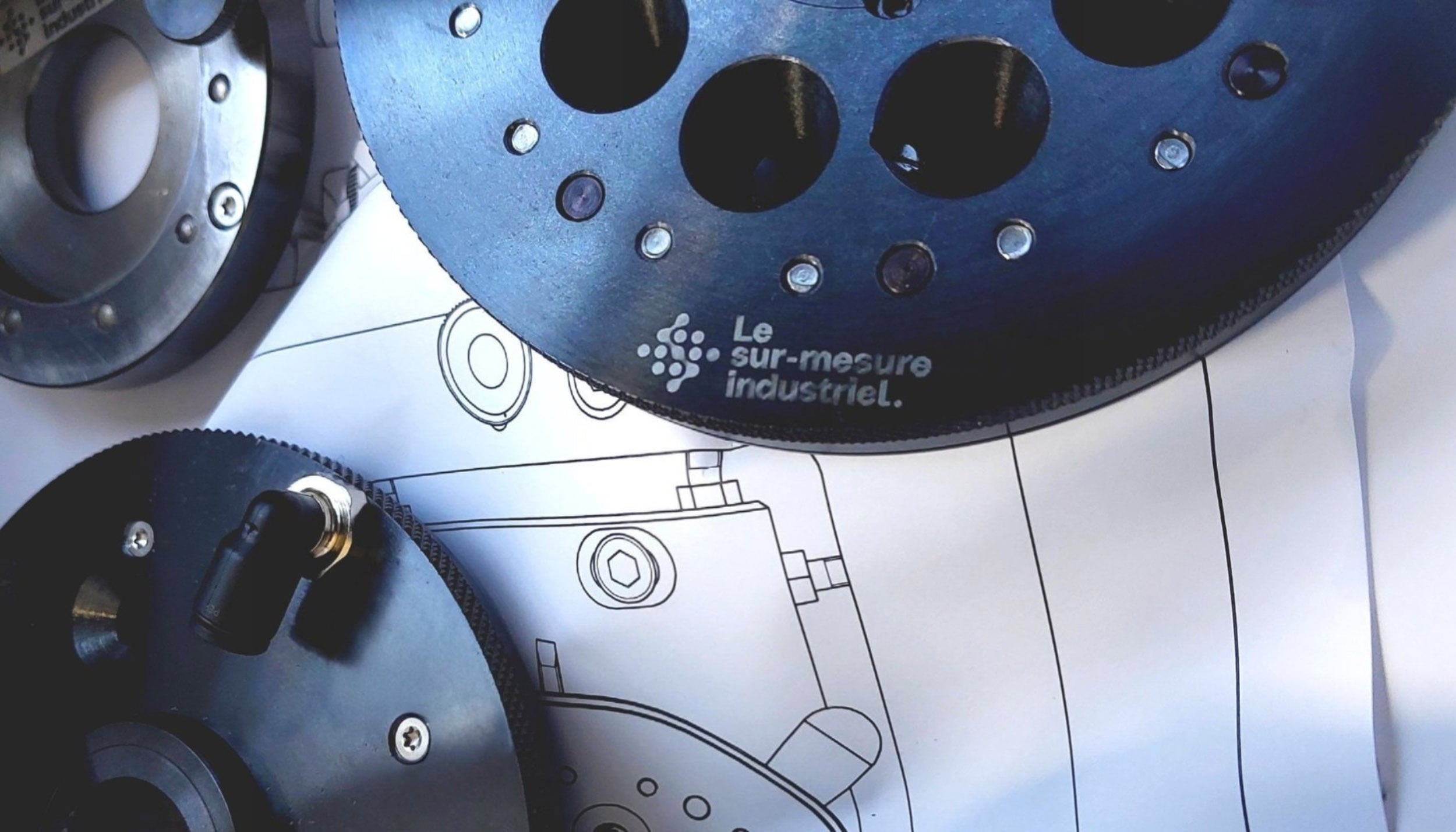

Design for manufacturing
We integrate manufacturing functions early in the design phase to anticipate and optimize fabrication stages:
Sheet metal work, mechanical welding
The parts obtained by sheet metal or mechanical welding are designed with the “sheet metal” functions of CAD, integrating the concepts of material, bend loss, bending V, unfolding, constraints linked to cutting, etc.
We design the parts with all the details to facilitate subsequent production, such as the integration of mortise and tenon joints to position and locate the sheet metal parts of a mechanically welded assembly.
With these design methods, the shapes are integrated directly into the cutting process, optimising preparation time, simplifying part positioning and improving repeatability and precision.
Machining and other processes
For machined parts, or for any other means of production, we adapt the shapes and design to ensure technical and economic feasibility and to satisfy the expected functionality: integration of the radius of milling cutters and machining inserts, clearance grooves, surface finish, material, coating, treatment, etc.
The same applies to the design of moulded parts, integrating drafts, fillets, parting lines, etc.
Furthermore, our digital design tools enable us to send files that can be used directly for prototyping or manufacturing by our suppliers in France. We regularly generate files for direct 3D printing, water-jet cutting, laser cutting, folding machines and CAM systems for machining.
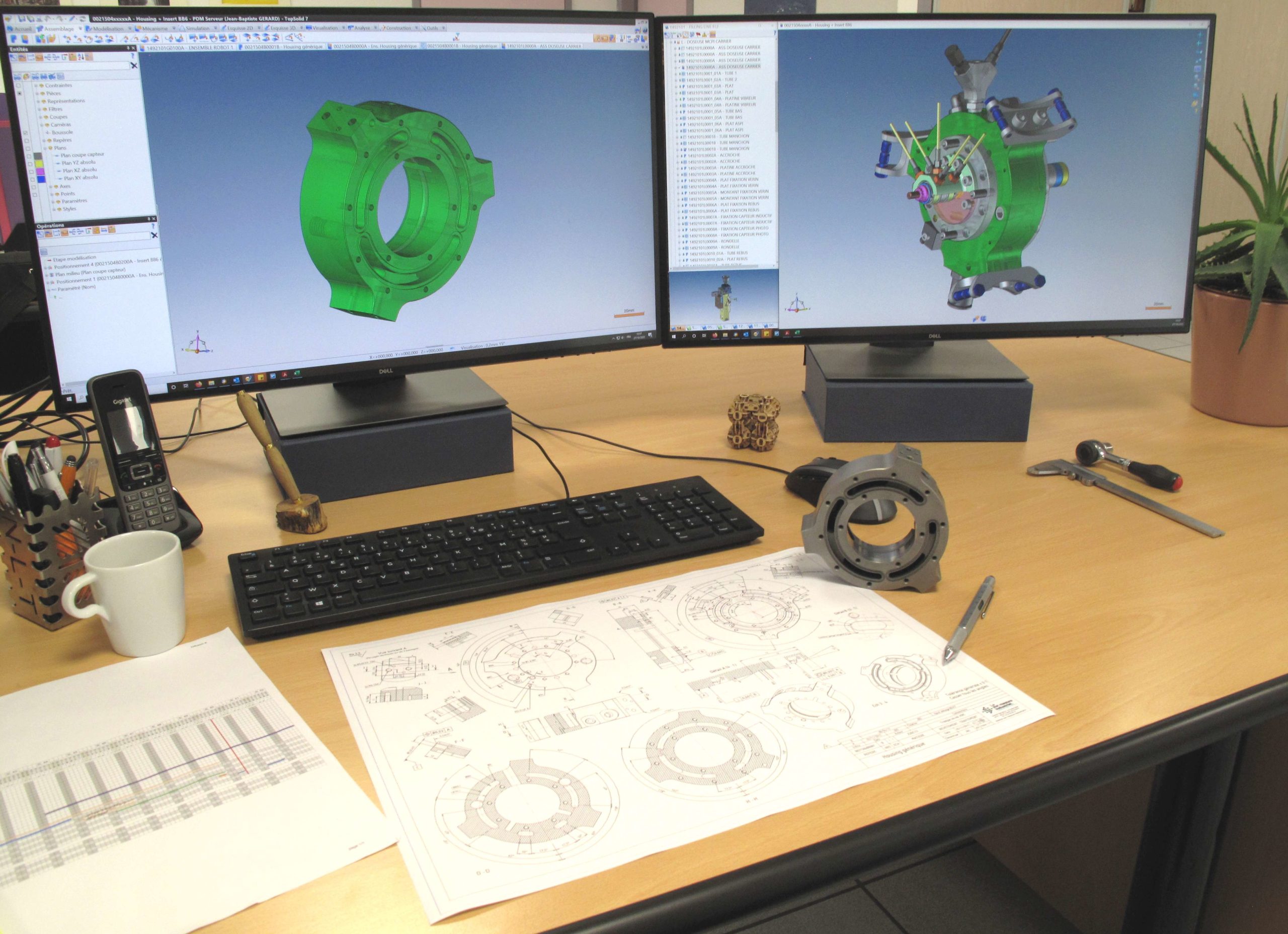
Transport, delivery and maintenance
In the same way, the industrial equipment designed by our company takes full account of the constraints associated with its transport and installation at our customers’ sites. Depending on the mode of transport that will be used, or the constraints of routing and passage through factories, the machine gauges are adapted.
For example, we design machines whose sub-assemblies can be dismantled, or chassis made up of different structures that can be reassembled on site.
We take particular care in considering maintenance operations on our equipment by providing access and possibilities for dismantling the various elements. The adjustment procedures are communicated, the diagrams and the precise and durable markings on the cables and pipes also allow easy maintenance.
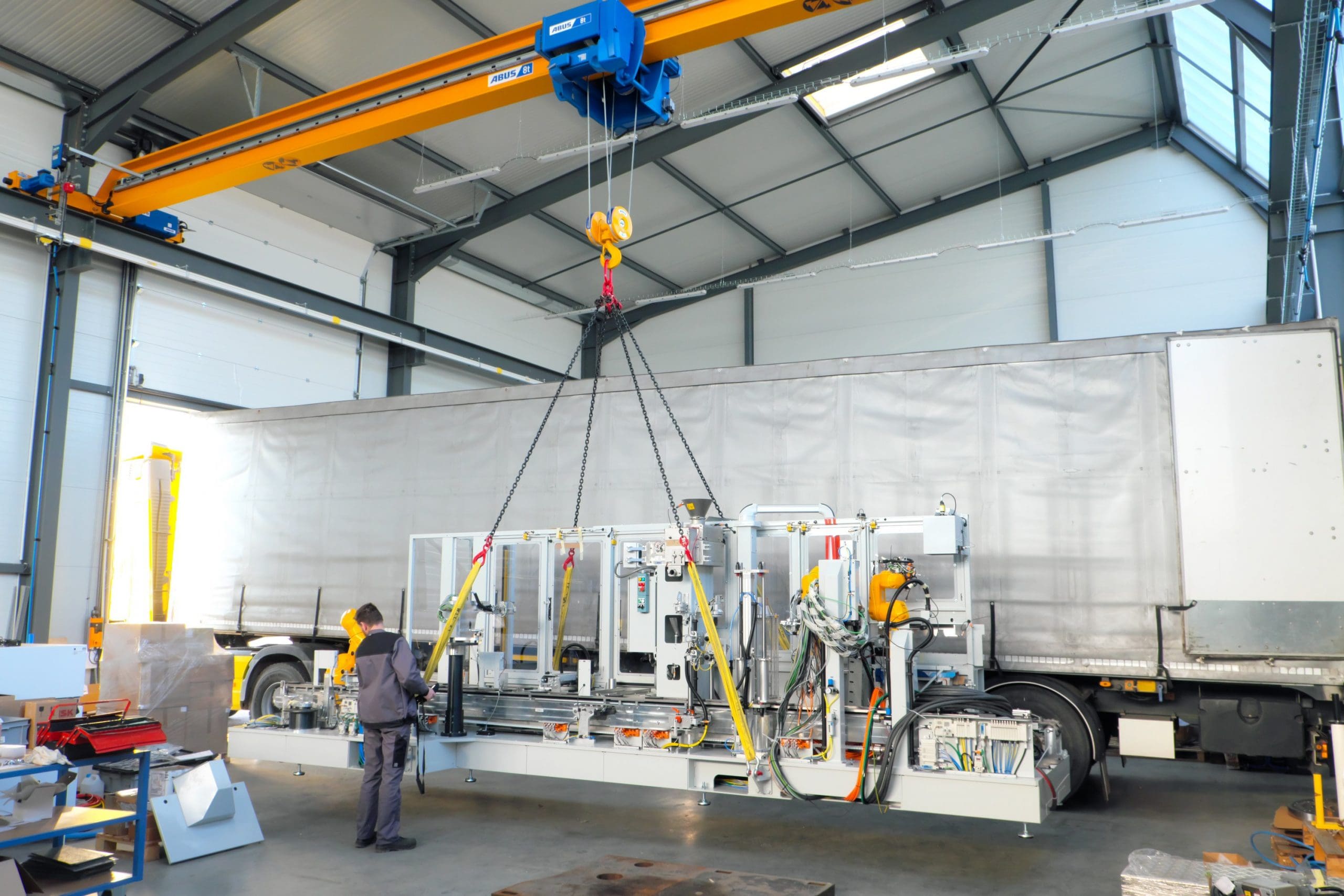
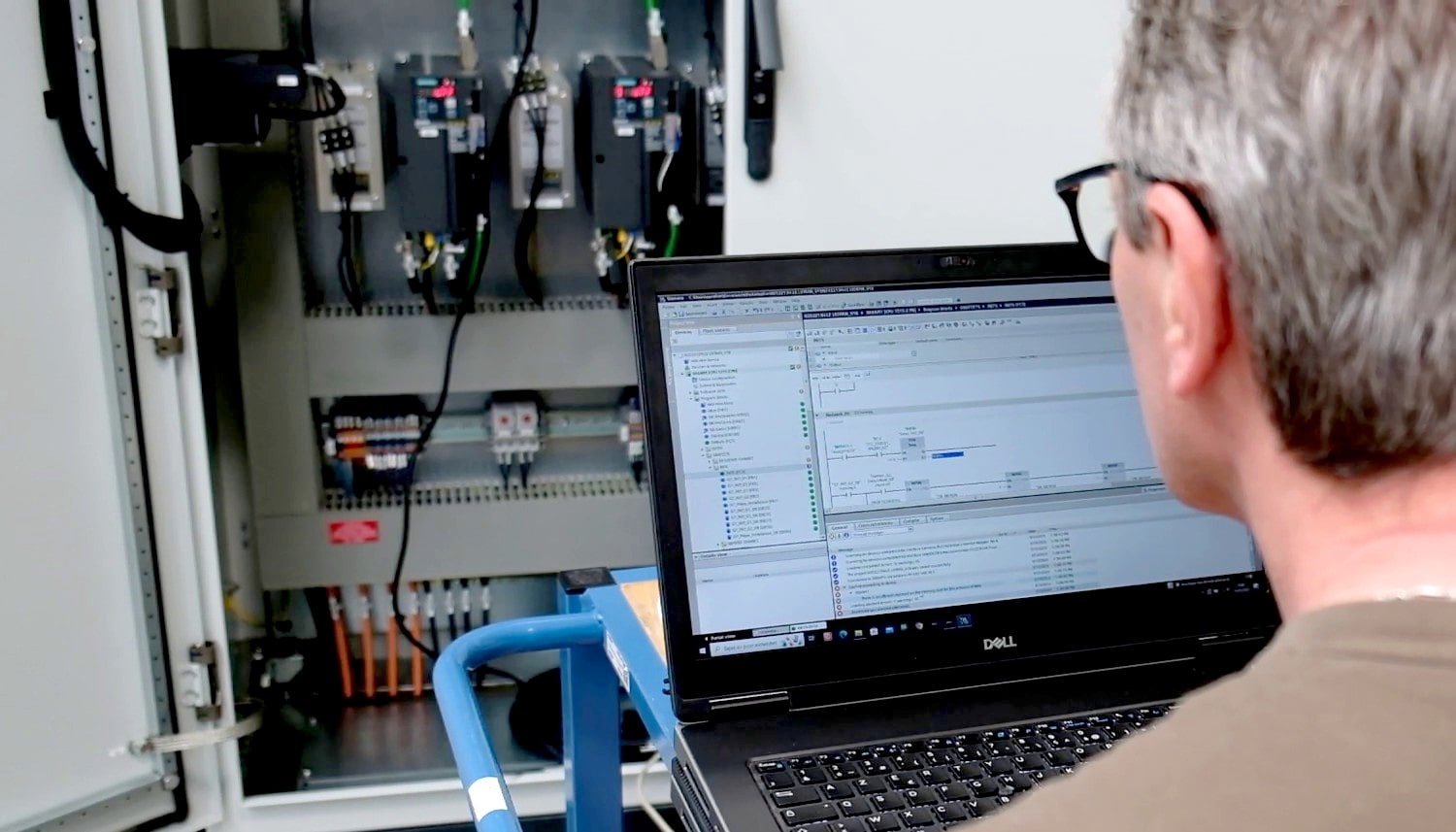
Connected industrial equipment
ding you up.
Industry 4.0
This means, for example, that key process parameters can be continuously monitored, deviations observed, alerts generated, problems targeted with a view to correcting them, and valuable information provided for preventive or corrective maintenance, as well as for improving the reliability of industrial equipment.
Remote connectivity
Frequently asked questions about our industrial equipment
What business sectors does Le Sur-Mesure Industriel work for?
Our company works for all sectors of activity, mainly industrial, but not only. You can find an overview of the areas in which we have already successfully completed numerous projects.