Robotics
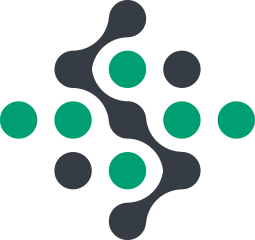
SMI, mechanical design and integration of robotic solutions
As a designer of special machines, our company has a strong base of skills in mechanical design, assembly and industrial automation. This gives us the flexibility and agility to create all-in-one robotic solutions that are perfectly adapted to your needs.
Depending on the level of complexity of your project, we implement all of our skills to develop the complete mechanical and robotic solution, or to integrate industrial robots into existing mechanics.
We guarantee the integration of the appropriate robotic solution for our industrial customers, by supporting them in all stages: definition, design, automation, robotisation.
With dedicated simulation software, we combine the 3D model of the complete machine and that of the robot(s). The trajectories and all the passage points are programmed and simulated, thus making it possible to validate the feasibility of the project and anticipate commissioning.
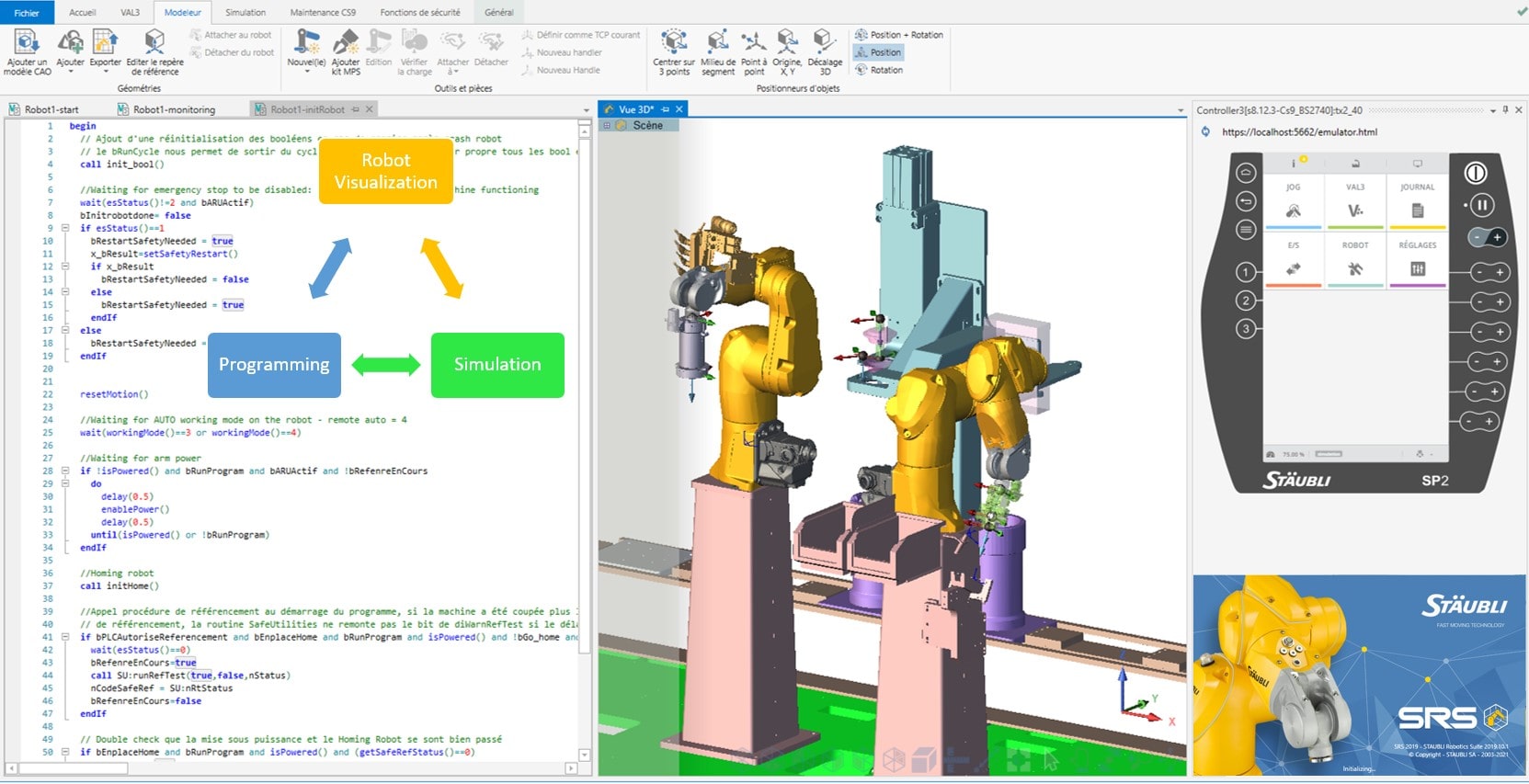
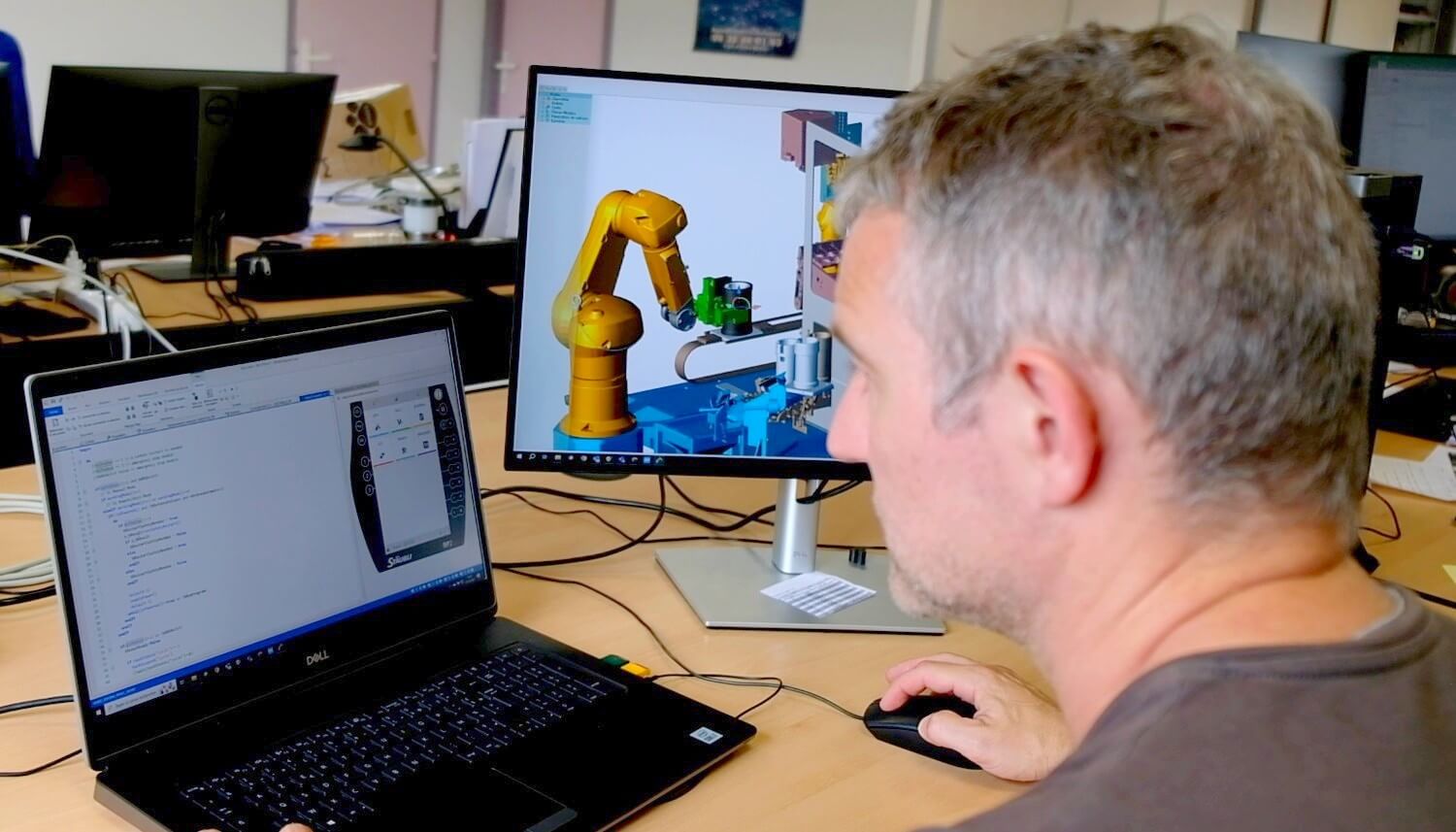
By taking advantage of the complete CAD model, it is also possible to ensure from the design stage that all the movements envisaged are possible, without any collision with the environment. At the study stage, it is also necessary to check that the robot can work with all degrees of freedom on all its axes and that there is no unreachable useful area.
For each work cycle, we program the speeds and accelerations of the axes, taking into account the limit on-board loads, in order to ensure the maximum longevity of the robotic arm.
During installation, we optimize on-site in real conditions, the trajectories, accelerations, and sequences, in order to meet the target cycle time objective.
Versatile integrator: Mechanics, Automation and Robotics
In the integration or creation of equipment or a line, it often happens that the developers and installers who deal with mechanics, industrial automation and robotics are people from different companies.
At SMI, the team at your service has all the skills! A considerable advantage in terms of efficiency and development time.
Indeed, in a robotic solution, the interface between all these disciplines is essential and it is very advantageous to have a permanent link between the mechanic, the automation engineer and the robotics engineer in the same company, and this, until commissioning.
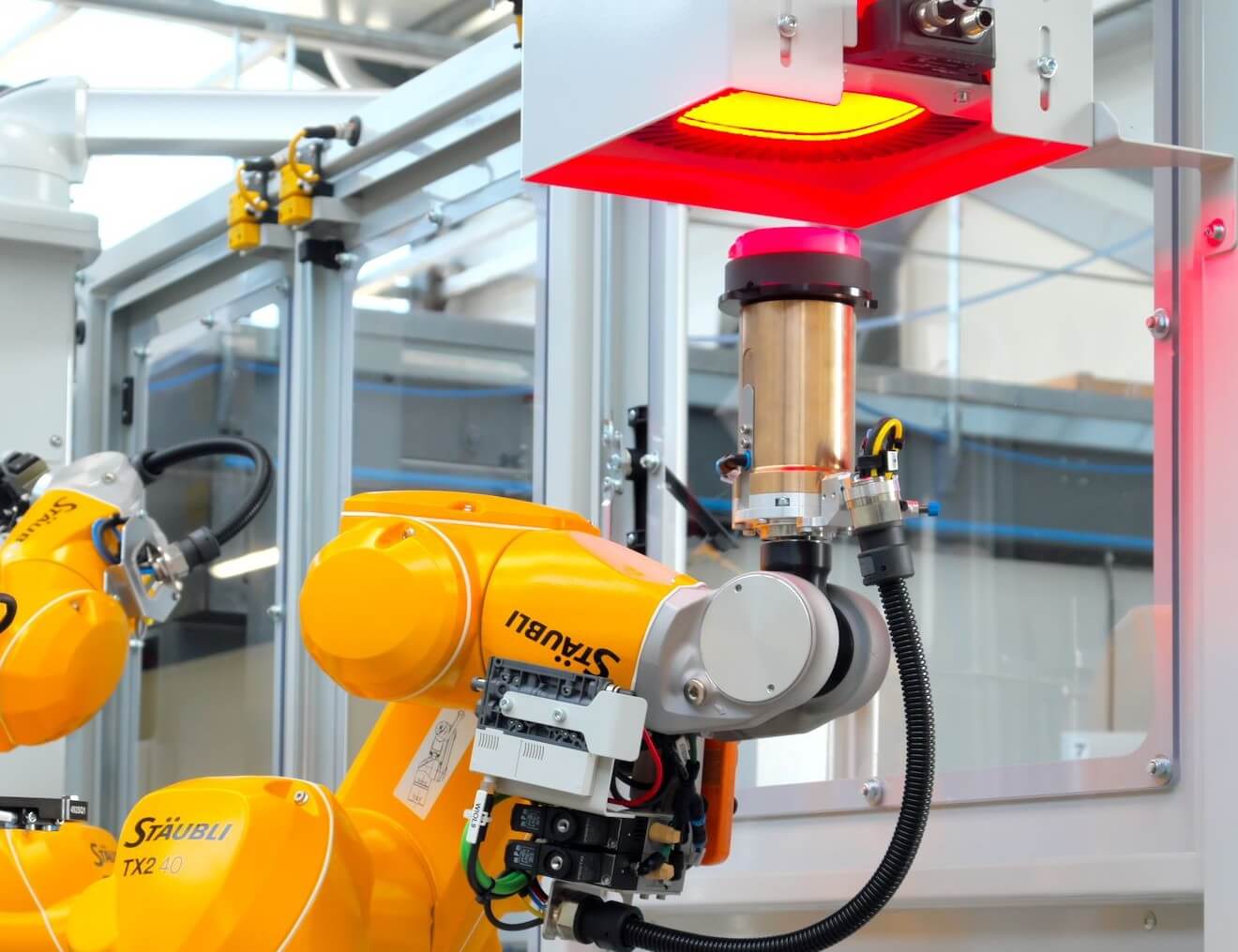
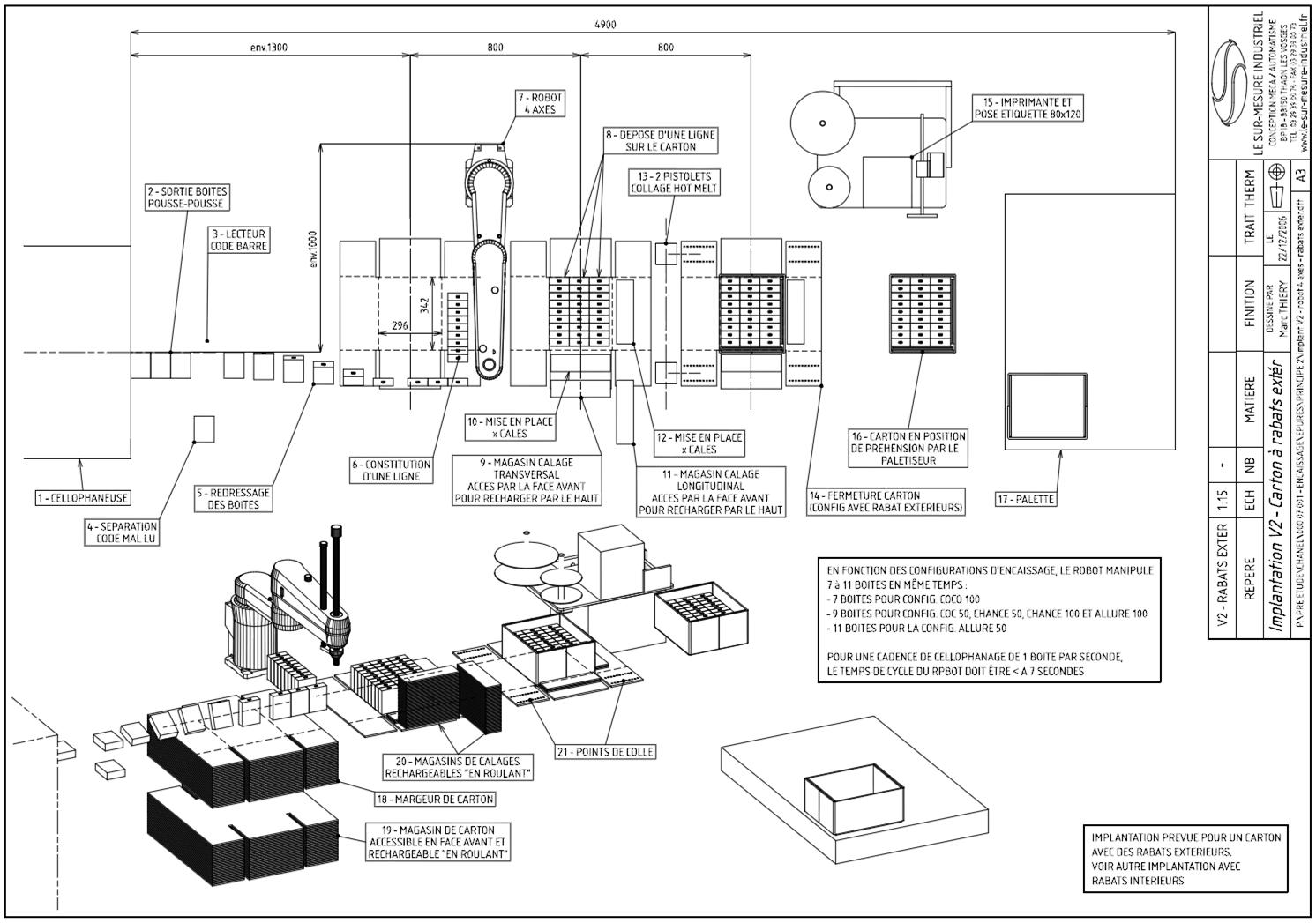
Who is robotics for?
The integration of robotic solutions is aimed at all types of companies and in all sectors of activity.
- Are you an SME or an international company and you want to create or modernize a robotic production line?
- Are you a distributor or manufacturer of industrial robots and you want to rely on reliable and efficient integrators for the study, programming and implementation?
- Your company has a manufacturing and assembly process that is well established, and now that it is robust you are looking for integrators or machine manufacturers to automate it in order to gain productivity and reduce costs?
- Your manufacturing process requires repeatability, reproducibility, manufacturing precision and humans are reaching their limits, especially when it comes to handling heavy objects or with high rates?
SMI: Integrator of industrial robotics solutions
Le Sur-Mesure Industriel, established in France, supports you in the realization of your project, from simulation to on-site commissioning.
There is no question of the robot replacing humans, but it is essential to relieve operators of arduous tasks that have consequences on their health while improving the productivity of companies. We help you implement robotic solutions and technologies in order to prevent risks and gain speed and quality.
With our skills in mechanics, industrial automation and robotics, we have all the tools in-house to be the integrator who provides you with the turnkey robotic solution you need.
We also develop custom gripping solutions for our customers (pneumatic grippers, vacuum technology, grippers with servo motors and instrumented by sensors, etc.).
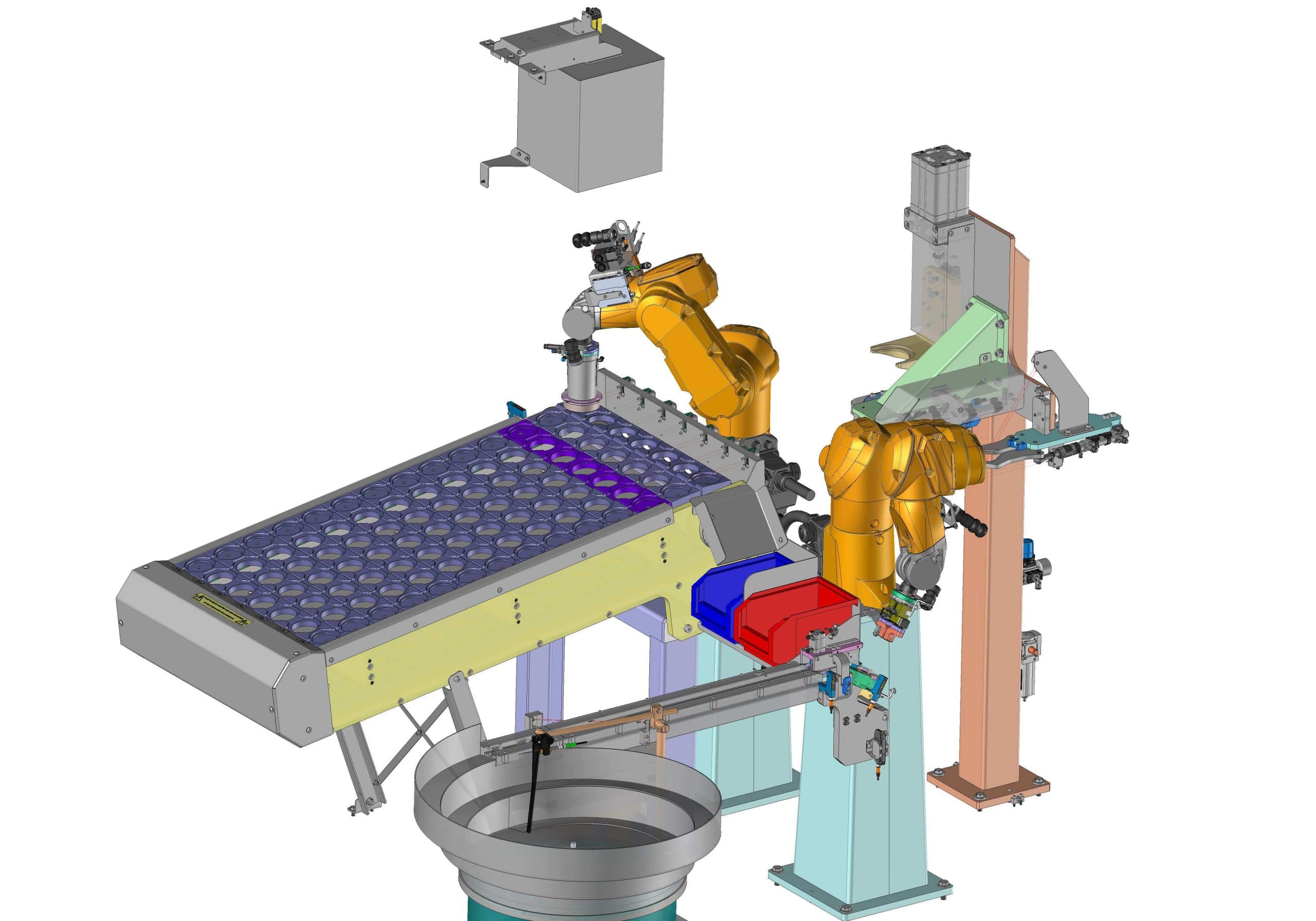
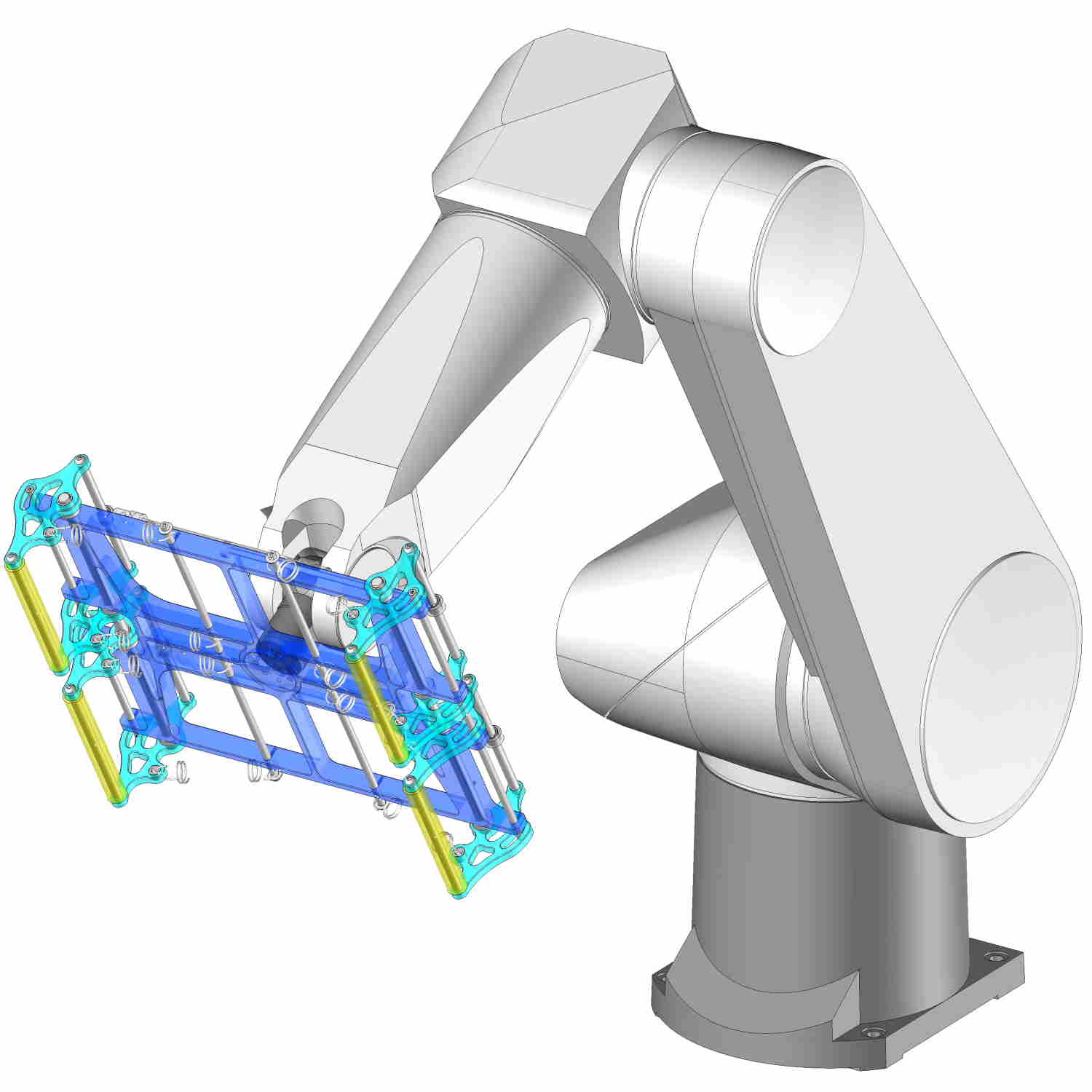
Feasibility
We help you clarify your needs if necessary by studying the possibilities with you via essential preliminary design work: determining the size of the robot, simulating trajectories, amplitudes and stresses on the axes.
It is possible at the preliminary design stage to simulate the different approximate cycle times according to the movements envisaged. This gives a clear vision of the possibilities according to the objectives.
Obviously, the clamp closing times, communication with the PLC and other latency times inherent in the technical reality of the installation will be estimated at the start and then confirmed after installation
The benefits of robotic solutions for our customers
Increasing the capacity of a production line
Safety of handling heavy loads
Accelerating the speed of a production line
Securing human errors
Automation of operations
Prevention of MSDs, musculoskeletal disorders
Support
Combination of technologies
Different cutting-edge technologies can be combined to perform various operations: industrial vision with robotics for keying, orientation, part sorting, defect detection, unpicking.
Do not hesitate to tell us about your projects and entrust us with your studies.
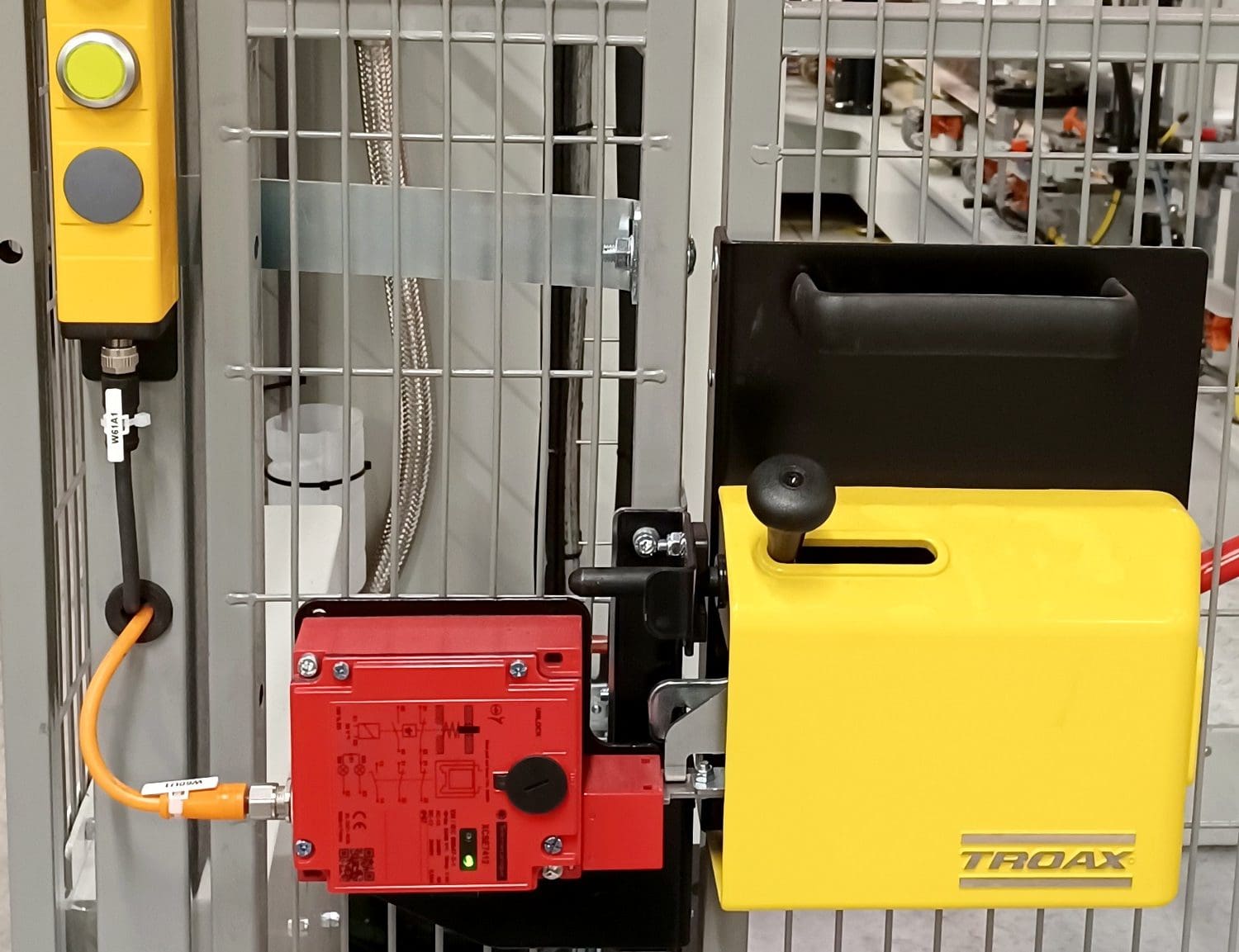
Safety at the heart of every robotic solution
Robots are motorized organs with a high kinetic energy during their movements, it is essential that humans are protected from the risks inherent in their use.
Different safety solutions can be implemented depending on the risks, needs and constraints. If proximity to operators is unavoidable, the use of immaterial barriers or laser scanners makes it possible to define zones in which the robot will switch to slow speed or stop.
The design of fully enclosed and locked robotic cells represents the ultimate safety solution. With the management of access and door openings on demand, this allows for total security of the work area.
The speeds, accelerations, and work spaces are defined and programmed by the robotics engineer in the controller. These settings cannot be falsified by an operator, inaccessible on an HMI, which guarantees the safety of the machine and people.
In addition, in order to meet safety requirements, periodic referencing procedures can be applied. The robots come to present themselves in front of a safety sensor after a defined number of cycles. The positions of the axis encoders are compared with the initial positions of the machine, which checks for the absence of position drift during production.